EAM System vs. MRO Optimization: What You Need to Know
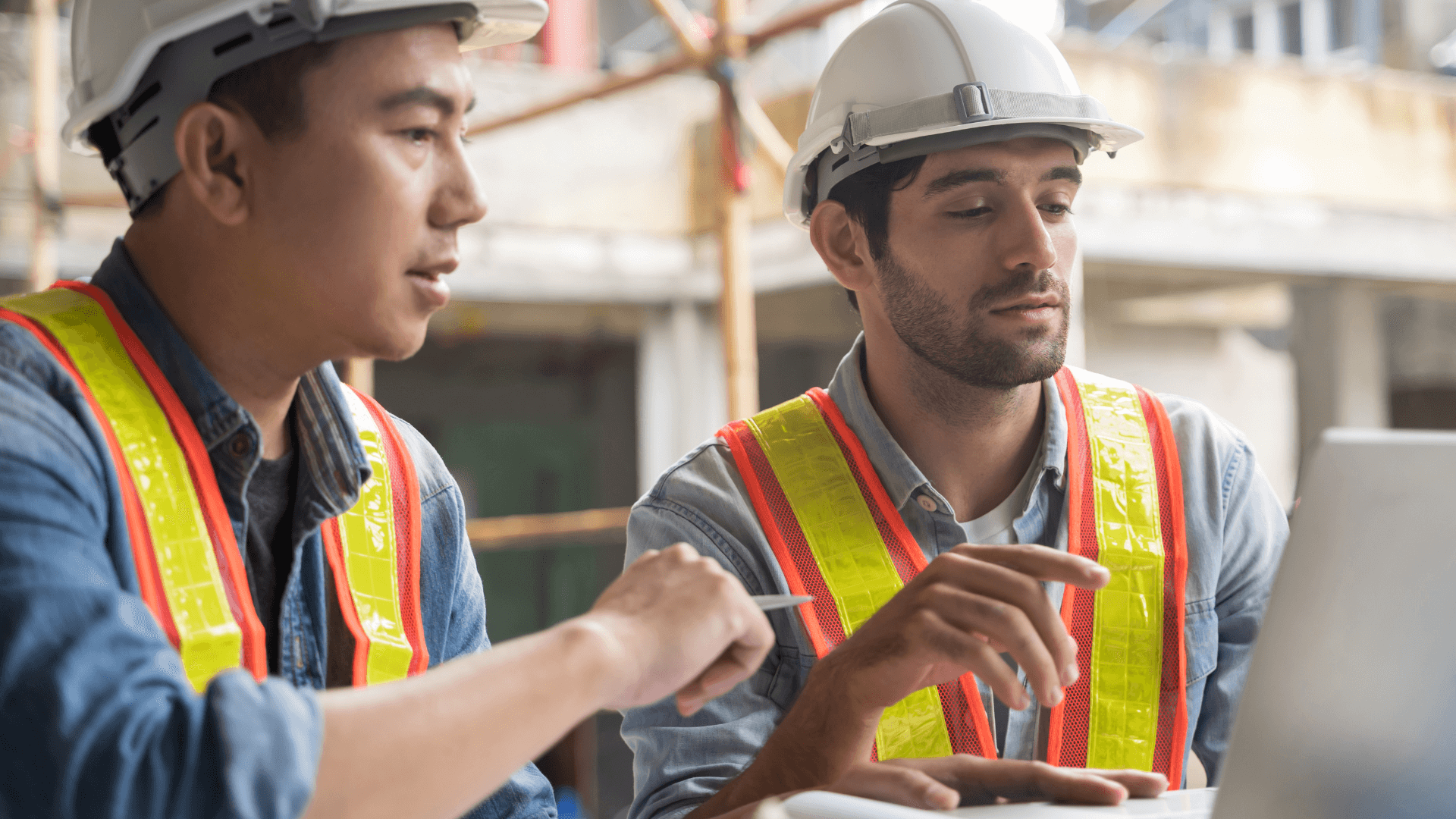
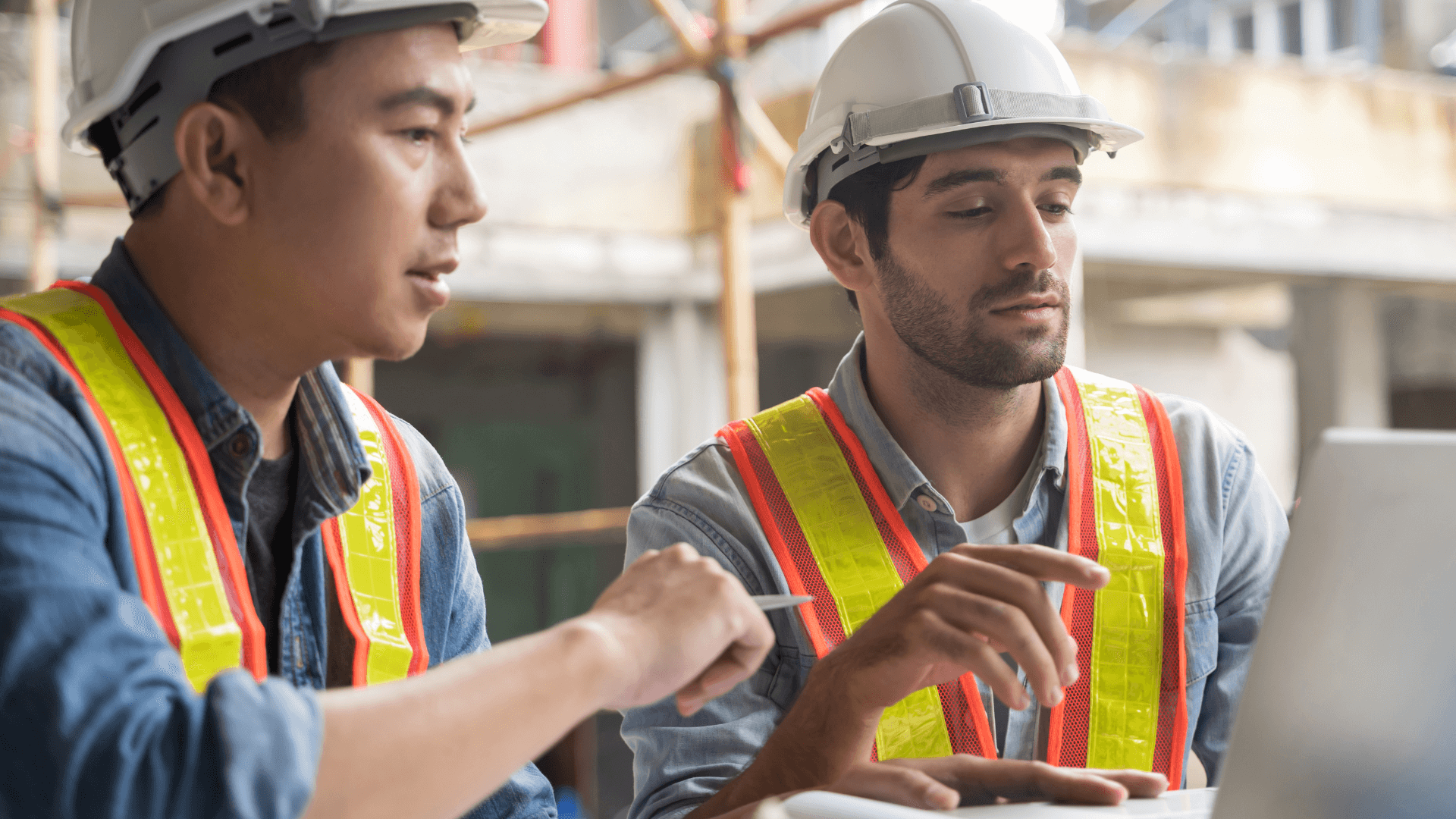
When it comes to supply chain operations, two asset management and optimization software systems stand out: Enterprise Asset Management (EAM) systems and Maintenance, Repair, and Operations (MRO) optimization software. While both aim to increase equipment efficiency, reduce downtime, and lower maintenance costs, there are significant differences between the two.
In this article, we’ll explain the key differences between EAM systems and MRO optimization solutions in order to help you determine why a combination of both solutions may be the asset management strategy best suited for your operation.
Determining which asset management strategy is best for you
What is EAM software?
Enterprise Asset Management (EAM) software is primarily used to help organizations manage assets from end to end, starting with acquisition and maintenance, all the way up to disposal. This tool can help organizations that are seeking to optimize asset performance and use by increasing visibility.
EAM software generally has the following features:
- Asset tracking
- Asset maintenance scheduling
- Asset performance analytics
- Automatic reporting
What is MRO optimization?
While EAM software systems can help organizations increase the longevity of the assets they have on hand through maintenance planning and reporting, they often do not include detailed spare parts and maintenance material management capabilities. This is where MRO optimization comes into play. MRO optimization is designed to help teams streamline their maintenance and spare parts inventory data to simultaneously reduce costs without introducing new risk of unplanned downtime. In addition to spare part inventory management, MRO tools also offer these insights:
- Total value of spare parts on hand
- Duplicate materials and min/max safety stock recommendations
- Material sharing across network of facilities
- Procurement and supplier insights
MRO optimzation can also provide advanced functionalities, such as hub & spoke scenario models, which uses data analytics and machine learning to determine the best methods for centralizing MRO and spare parts. This helps organizations reduce downtime and avoid costly, unplanned maintenance.
Furthermore, MRO optimization can be integrated with other software solutions, such as enterprise resource planning (ERP) tools and EAM systems, to provide a comprehensive view of maintenance-related costs, risks, and performance.
Why MRO optimization is right for your operation
Organizations looking to harmonize spare parts, optimize costs, and reduce risks should consider adopting a purpose-build MRO optimization platform.
For those looking for robust tools that can offer actionable insights and recommendations without conducting a data cleanse or lengthy implementation time, a purpose-built MRO solution may be the answer.
These tools offer detailed insights for strategic inventory management and procurement using your data as it currently exists. Procurement and maintenance teams across industries are turning to these new tools, particularly those that can have you up in running in 90 days.
The benefits of a purpose-built MRO optimization platform
Supporting long-term, strategic maintenance scheduling
Intelligent MRO systems that are powered by Industry 4.0 tools such as artificial intelligence and natural language processing can process large datasets from multiple systems & instances and yield actionable insights from them. For instance, material management software can analyze spare part usage metrics and risk assessments, reducing the likelihood of unexpected downtime and costly repairs.
The software can also use existing data to help optimize inventory levels used in preventative long-term maintenance schedules. By adopting MRO optimization to support your systematic maintenance plan, organizations can ensure that their right parts are always available in the right quantities to keep equipment operating at optimal levels. This proactive approach to maintenance extends asset lifespans, reducing the need for premature replacement and lowering costs over the long term.
Inventory and asset management
An MRO optimization solution provides a centralized platform for asset material management, allowing organizations to track the maintenance history, performance, and other important details of each spare part across the network. This not only enables them to make data-driven decisions about maintenance and repair activities, but also helps optimize spare part inventory costs while reducing the risk of unplanned downtime and eliminating the need for high-cost inventory strategies like overstocking and just-in-time inventory management.
Intelligent MRO systems can also help organizations improve reporting capabilities. Cloud-based data collection and storage makes it easy to automatically measure, record, and save analytics in a standardized way across the entirety of an operation. This makes it that much simpler to share information internally and externally when the time comes.
The right system can make all the difference
Implementing an asset management optimization strategy can be a challenge. The right tools can help procurement and maintenance teams not only streamline processes but expand optimize your existing spare parts inventory and reduce downtime as well. Ultimately, it all boils down to picking the right tool to help your team meet its performance goals. To find out more about how MRO optimization can help your team succeed, check out our whitepaper on how you can reduce operational costs with MRO strategy.
Learn how you can streamline your supply chain processes through intelligent materials management.
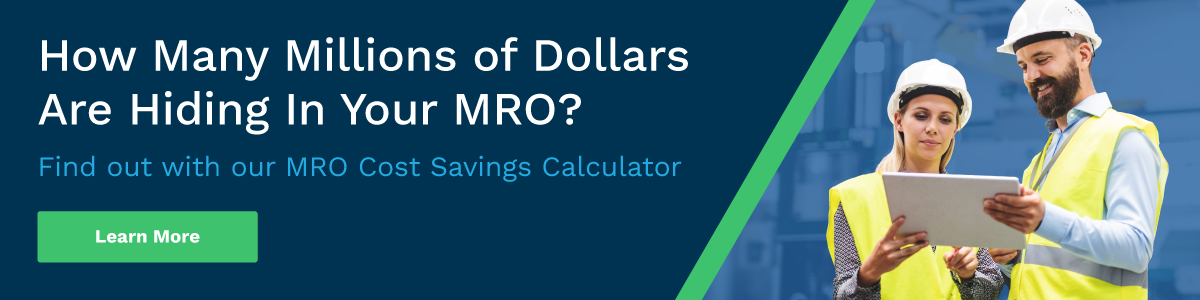
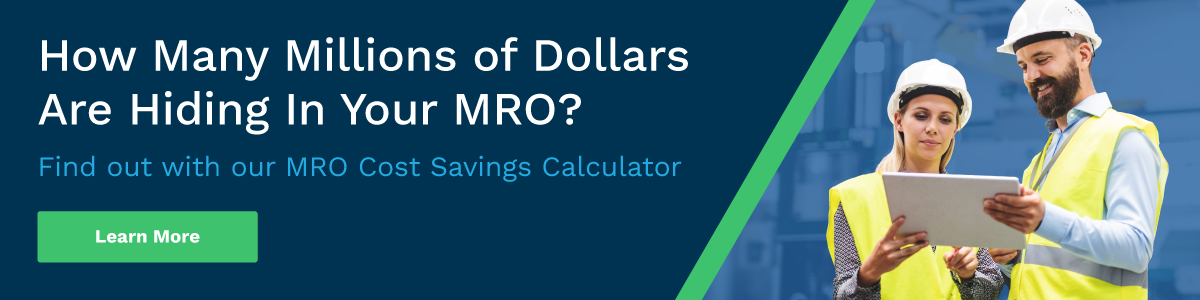