Ineffective Materials Management Techniques You Need to Move Beyond
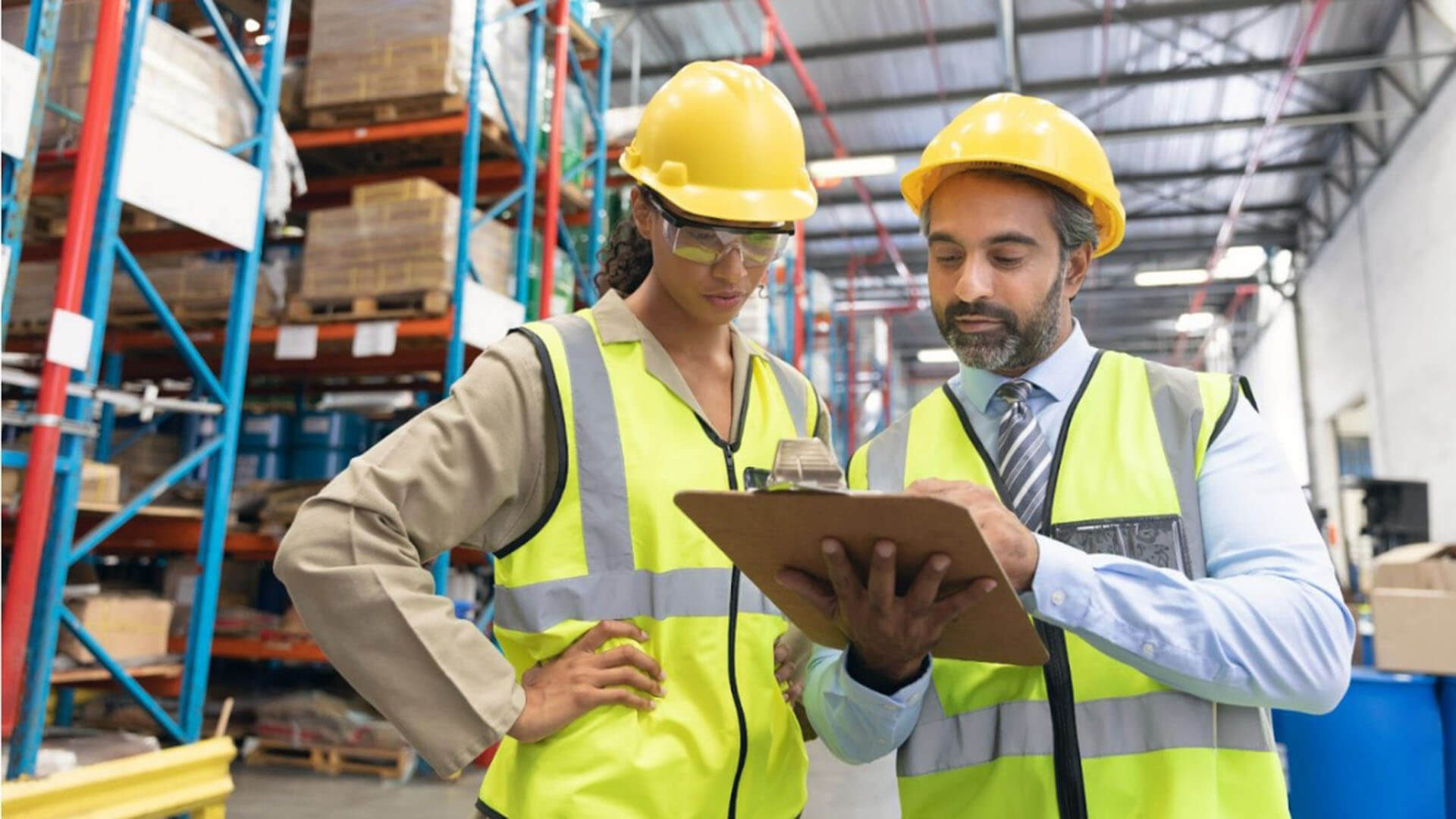
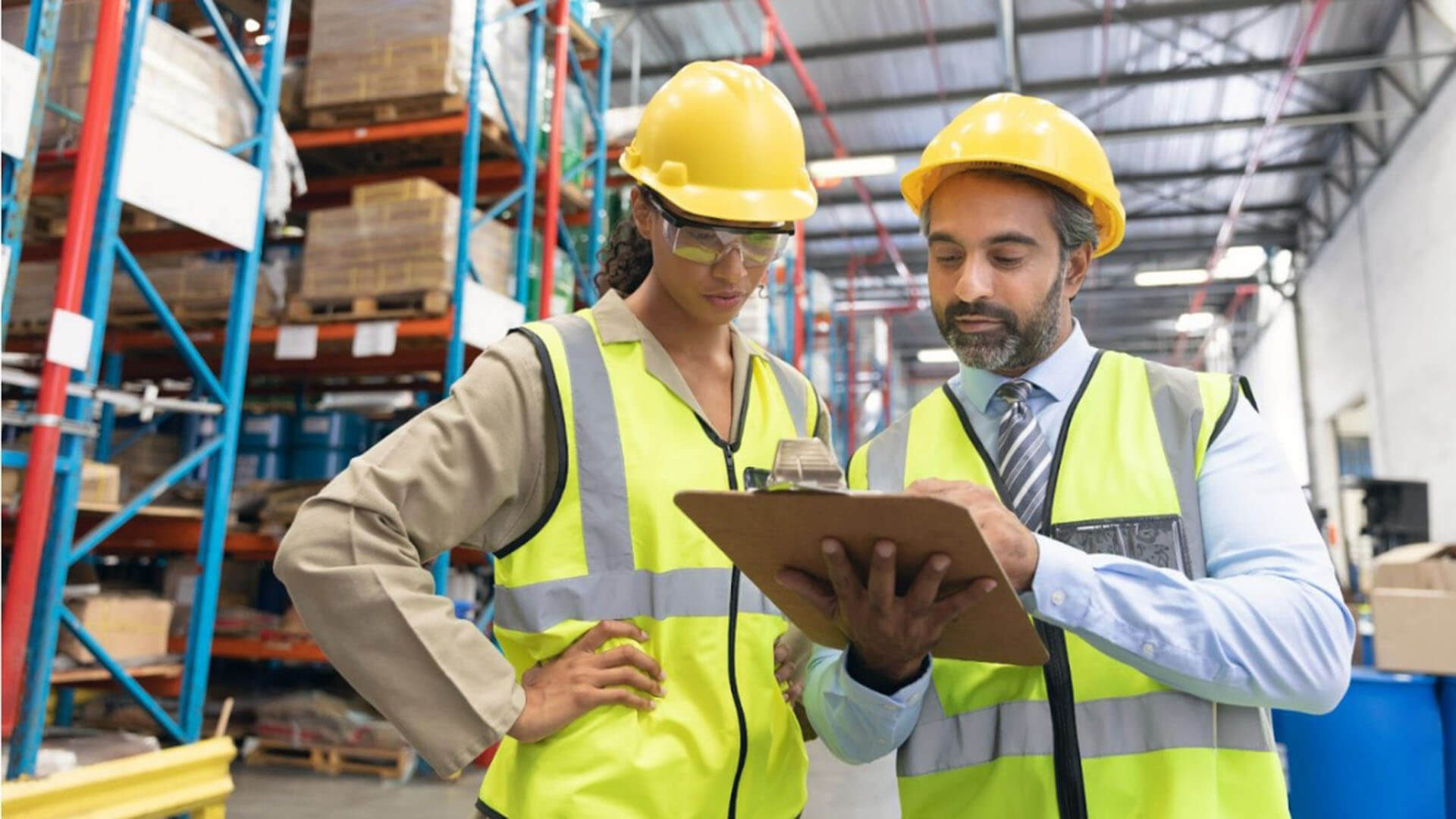
Materials management is a crucial component in the manufacturing process, whether it be delivering raw materials from suppliers to manufacturers or managing the spare parts needed to ensure finished products make it out the door.
Without a proper modern materials management strategy, businesses risk a litany of mistakes such as out-of-stock and overstock situations, missed shipments, mis-picks, and spoilage.
As such, it’s important to implement effective materials management techniques to not only keep MRO inventory at optimal levels but also minimize costs and maximize profitability.
Let’s take a look at three types of materials management strategies that you can use to have more inventory control in your business.
1. ABC Analysis
The Pareto Principle states that 80% of consequences come as a result of 20% of the causes, establishing an unequal relationship between the inputs and the outputs.
In the context of managing MRO materials, companies typically spend 80% of the time attempting to draw insights from inventory data and only 20% taking action on it. Therefore, many never gain a true ability to see where procurement spend is wasted or risk to production exists.
With MRO ABC Analysis can help sort the items in your inventory into three categories according to how much they cost to hold and the overall usage metrics:
- Category A: the high velocity spare parts in your inventory that need constant replacing
- Category B: these products are on a much longer timeline between usage dates and maintaining overages can result in high carrying costs
- Category C: these products highly specialized, have high carrying costs, and longer lead times regarding replacement
Sorting the items into the categories listed above helps global manufacturers decide which materials they should optimize. This can help cut down costs associated with holding excess inventory, but unfortunately, most companies don’t have the internal ability to manage this complex process on their own.
2. Precautionary Overstocking of MRO
Many organizations carry way more MRO material than is needed to ensure they have enough safety stock on hand should a production outage occur. This has happened more frequently in recent years as supplier disruptions have created far longer than usual lead times.
When setting up the appropriate safety stock levels, manufacturers should consider the total cost of inventory, the total usage metrics, and any other shipping expenses before the next procurement cycle begins. As a result, manufacturers can reduce waste while ensuring production maintenance and repair operations won’t be hindered.
3. Just-in-time (JIT) inventory
Just-in-time is an inventory management method where you manufacture what is needed when it’s required in the appropriate amounts. The primary objective of this system is to restock new products just as they’re needed instead of stockpiling them. This strategy has been a major contributor to the global supply chain disruptions that presented themselves during the onset of COVID-19 pandemic.
This method not only keeps organizations from being able to produce the inventory levels to satisfy customer demand, it also resulted in higher costs as manufacturers sought methods to expedite critical materials they could no longer find while empty shelves across the globe resulted in missed sales.
Businesses who once had the luxury of attaining more freedom when it comes to cash flow now find themselves spending revenue on massive shipments that eat into profits.
Optimizing your inventory management with Verusen
Predictive analysis
Many SaaS solutions are integrated with Industry 4.0 tools such as artificial intelligence and machine learning that can help yield valuable insights from historical data.
Powerful algorithms can analyze large datasets that give information about MRO materials needed to keep your factories running. This data can be extrapolated to predict future needs so that businesses can know what items need to be restocked and new purchases of certain items can be skipped to reduce overages that are crowding the storeroom.
Businesses can prevent overstocking their storerooms and holding dead stock, which can lead to increased costs in terms of write offs of wasted working capital. Instead of relying on estimated guesswork, organizations can maintain optimal MRO inventory levels such that costs are kept to a minimum and maintenance needs are satisfied with our AI-driven MRO inventory platform.
Increased visibility
Material management software allows businesses to aggregate data across multiple tiers of the supply network into a single, personalized dashboard that not only provides insights but recommendations for optimization. Hence, businesses can gain a bird’s-eye view of the entire enterprise instead of a keyhole view of a subset of it, which makes inventory management that much easier.
For instance, a unified view of your supply network can tell you how much inventory is sitting in each storeroom, what the product composition is, what the inventory turnover rate is for each item, and so much more.
If stock levels for a particular product fall below a safety threshold, businesses can get immediate alerts informing them to restock. With just a single tap of your fingertips, you can make an order for another batch of stock without actually visiting the storeroom to know what the stock levels are.
Reduce the risk of production downtime
Production downtime must be quickly, yet carefully managed, regardless of the reason lines have been stopped.
Whether planned for maintenance or not, since production is halted, the plant will not be able to produce as much as it would during optimal conditions.
Advanced technology, such as artificial intelligence and machine learning, can be leveraged to minimize the supply chain risk of production downtimes on inventory. These tools can analyze past occurrences of production downtimes and identify patterns that can be used to predict future equipment failures with a high degree of accuracy.
Since issues such as machinery lubrication, contamination, misalignment, and the like are identified well in advance, these issues can be dealt with before a disruption occurs. Since this minimizes the amount of unplanned production downtime, manufacturing operations can continue with no issue. This means that businesses can meet and exceed OTIF levels to keep customers happy.
Harness the power of digitization
As a global manufacturer MRO inventory management is essential to give your customers what they’re looking for and stay ahead of the competition.
Investing in the right technology should be your first step in taking your materials management to the next level. To learn more about balancing efficiency and responsiveness through material management software, download the ebook on overcoming MRO challenges today.