What New Technology Bodes for the Energy Value Chain
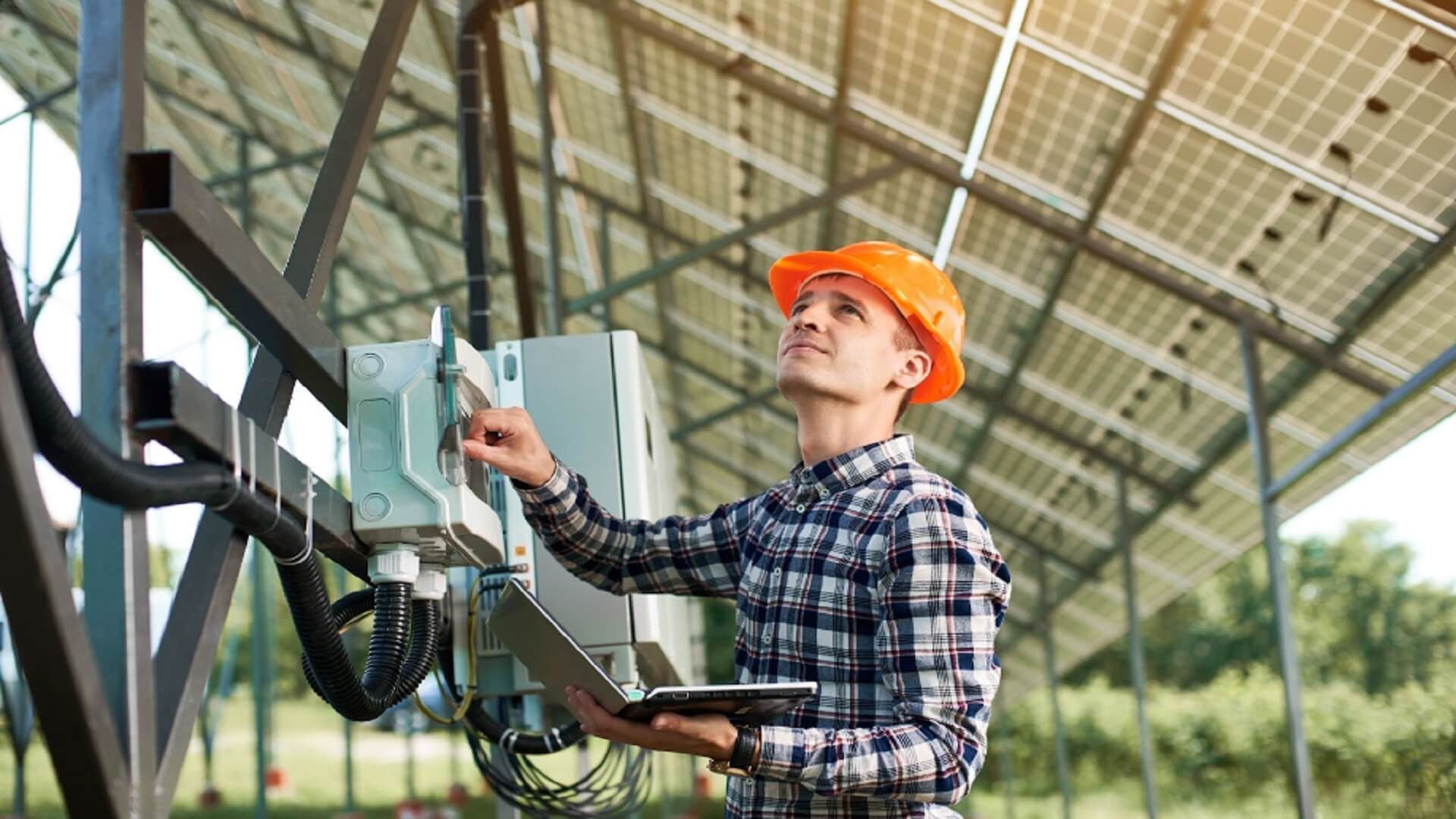
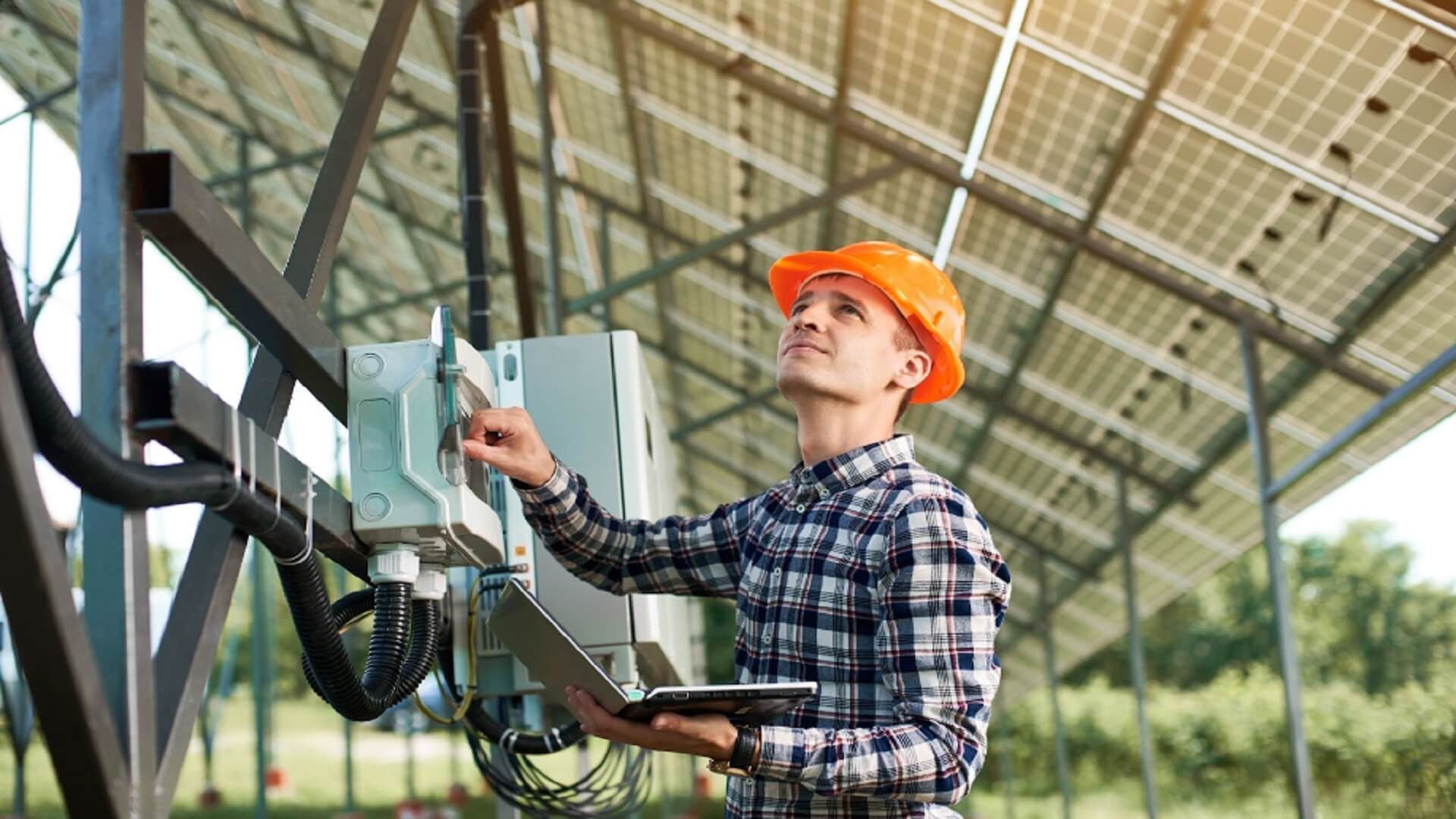
The energy sector is a vital component of modern society. However, as production ramps up, companies are faced with new challenges. The service sector struggles to keep up and find new ways to minimize costs and maximize profits.
Here’s how new technology impacts existing energy value chains and how companies can leverage them to meet their growing energy needs while taking on energy sector challenges.
Keeping up with booming energy needs
Avoid sector disruptions
Efficient communication with oilfield service providers and vendors is an integral part of avoiding sector disruptions. Many businesses still make the mistake of using siloed communication pathways with their suppliers, creating unnecessary roadblocks.
These small disruptions can lead to a larger domino effect, setting operations back, and ultimately leading to overspending, operation downtime, or compliance challenges.
A system that doesn’t facilitate smooth collaboration with relevant stakeholders is doomed to fail. Streamlined record keeping and information sharing is the only way to make your organization resilient in turbulent markets and to hit the ground running again when things take a slight detour.
Keep projects low-cost to see high returns
Unplanned production outages and inventory spending are the largest contributors to your total costs. But, finding a happy balance between being prepared and saving on parts can be a challenge.
It’s part of the reason why operations turn to outdated materials management strategies, like “just-in-time” inventory keeping. Waiting for an asset to reach its point of failure to order replacement parts is not the best maintenance strategy. It leads to production delays and can put your operation in the hands of suppliers with delayed shipping.
Rather than relying on these outdated models, more operations are turning towards intelligently recommended materials management instead.
Carefully scheduled maintenance that is both routine and optimized allows operations to continue to run smoothly, without seeing operation costs skyrocket. It prolongs the lifespan of your assets without adding weight to your bottom line.
These recommendations are made based on historical data sets that identify assets that are low-use but high-cost. This quick insight alone breeds an opportunity for reinvestment, allowing you to see a higher return on your capital.
A growing interest in performance-based contracts
More and more operations are turning towards performance-based contracts that keep suppliers accountable. Using key performance indicators and shipping metrics, this new approach to negotiations helps procurement teams create a reliable supply chain.
Such contracts usually outline the following but aren’t limited to:
- Benchmark for performance
- Acceptable quality standards
- An overview of how performance will be measured
- Procedures, compensation, or responses to shipping delays
The problem arises when reported data is disparate, a common problem that can arise when sites use different reporting systems and vendors. The right materials management strategy should take existing contracts into account when creating a data collection system that returns harmonized and meaningful data.
Lean on smart solutions
Reduce costs with increased visibility
A lack of visibility is the single biggest factor that continues to rob organizations of opportunities for optimization. Most businesses have a partial view of their supply network, turning a blind eye to vulnerabilities in their system.
The right material management solution consolidates data across the entirety of your enterprise, including information from multiple departments, sub-units, storerooms, and locations, before aggregating it into a single platform. With a holistic view of your operation, you can identify bottlenecks that need attention before they lead to delays.
For instance, with data points from previous occurrences of downtime, you can identify which machines require the most maintenance. Coupled with powerful artificial intelligence and machine learning algorithms, you can use this historical data to create cost-efficient but effective maintenance schedules that prolong the lifespan of your assets.
It creates a system that thrives on predictive analysis, making it possible for you to receive insight regarding future downtime events, too. Not only does this help avoid delays, but since you’re not hoarding replacement parts based on estimated guesswork, you can also cut costs.
Make communicating easy
A cloud-based solution eliminates the need for traditional, proprietary systems that hinder the flow of information within the energy value chain. Unlike these disparate systems, a cloud-based platform avoids redundant, siloed data even on a location-by-location basis.
Unlike manual systems where individuals have to sift through spreadsheets and purchase order pdfs for information (which may or may not be accurate), users can easily access meaningful data in real-time that is both accurate and reliable.
By housing data in a single platform, it becomes extremely convenient to set performance benchmarks and use Key Performance Indicators (KPIs) to track performance. This not only makes it that much easier to convey progress to your investors, but it also helps avoid any chances of miscommunication.
Be ready for changes no matter what they look like
With so many changes in global political and economic circumstances, the road ahead can look uncertain. It proves that it no longer makes sense to rely on traditional methods against a dynamic market.
Embracing a digital transformation can make your operation more resilient and responsive, regardless of what lies ahead.
Learn more about how to mitigate your organization’s expensive data problem today.