Building Best Practices and Strategies for Manufacturing Maintenance
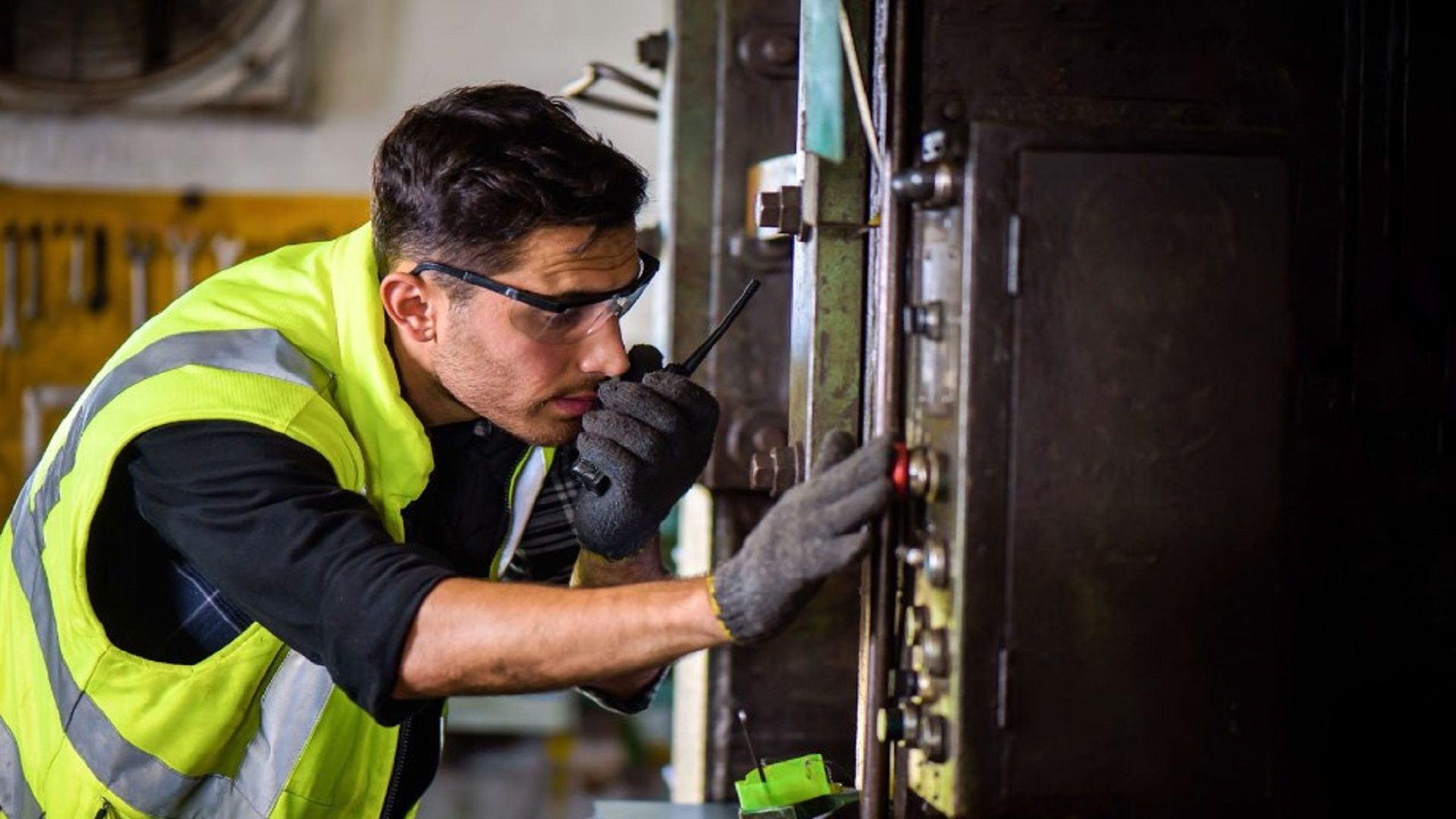
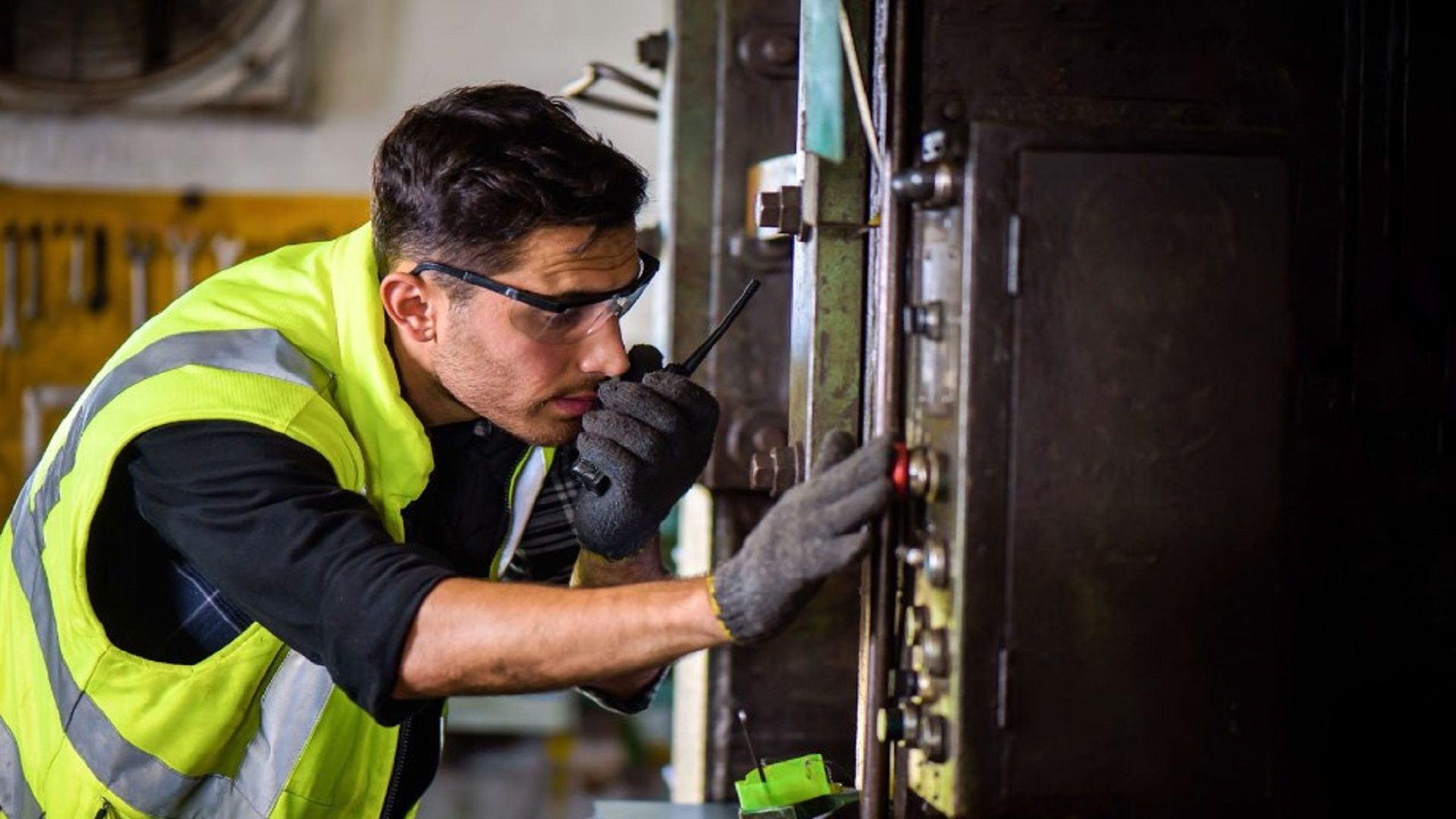
The global marketplace is a fast-moving and competitive landscape. And for manufacturers, maintenance, repairs, and operations (MRO) can make-or-break operations, especially if mismanagement occurs and leads to unplanned downtime.
Traditional MRO strategies simply don’t cut it in today’s markets, and manufacturers who are still employing these practices that don’t prioritize MRO inventory optimization are quickly being outpaced.
Choosing the right MRO strategy keeps operations up and running on minimal resources without wasting production time or introducing unnecessary risk.
However, there is no one-size-fits-all maintenance strategy. Here’s how you can use four highly regarded best practices and strategies for manufacturing maintenance, with some much-needed updates from contemporary tools.
Types of manufacturing maintenance strategies that work
Corrective maintenance
Corrective maintenance can be categorized into two parent classes:
- Planned corrective maintenance
- Unplanned corrective maintenance
Planned corrective maintenance refers to asset repairs that can be deferred to a later, scheduled date. This strategy may be helpful if you’re running a tight budget, have limited time, or if you are short on staff. Planned corrective maintenance can be further broken down into run-to-failure maintenance and preventative maintenance.
Run-to-failure maintenance keeps assets running until they break down and require repair. This strategy is useful for assets that are non-critical and/or redundant and those that can be easily repaired or replaced.
For instance, let’s say a system comprises several fans. Assuming that the system can run properly even if one fan breaks down and that you have an adequate number of replaceable fans in your storeroom, you can let the system run until one of the fans breaks down. In this situation, replacing the fan will be both quick and inexpensive. However, lacking visibility into how many fans you have, whether it be too many or not enough, can end up costing you some serious money.
Unplanned maintenance refers to repair actions taken immediately after an asset fails or shows signs of potential failure like when a part breaks and clogs the whole production line, both literally and metaphorically. These episodes of production downtime can be catastrophic, result in massive losses, and require immediate attention.
This type of maintenance has a high level of unpredictability which can lead to a backlog of work orders. A lack of planning and insight can lead to serious downtime, missed deadlines, and massive hits to your budget, especially if the assets that failed are expensive or hard to replace. In general, these problems snowball into complicated issues that aren’t easy to resolve.
That’s why harmonizing your MRO inventory to make sure you have the right part in the right place at the right time can be the difference between meeting OTIF or missed SLAs and falling profits.
Preventative maintenance
“Small oversights can lead to big problems” is the philosophy of those who practice preventative maintenance.
Preventative maintenance leverages planned maintenance cycles to reduce the risk of failure and prevent equipment from degrading.
This is done at set intervals such as every 30, 60, or 90 days according to a set of predetermined criteria. Because maintenance is systematic and performed routinely, manufacturers can arrange backup equipment to be up and running during scheduled downtime to avoid emergencies or unforeseeable circumstances.
This can maximize the longevity of an asset whilst minimizing the risk of unplanned downtime. Using assets to the point of failure usually ends up costing 10 times more than periodic maintenance, so there is also a cost-benefit for running on a preventative schedule. On the other hand, over-scheduled maintenance can result in wasted time or overspending on parts so a healthy balance must be struck for maximum ROI.
Risk-based maintenance
Risk-based maintenance gives priority to the most risk-sensitive systems and machinery, such as:
- Production lines in machinery
- Infrastructural equipment
- Building ecosystem (lighting, electrical, plumbing)
- Modes of transport (trucks, containers)
Risk-based maintenance approaches resource distribution from an economic standpoint. It generally happens in two phases, risk assessment and finally the creation of a plan of action based on risk assessment.
Risk assessment largely seeks out high-risk assets and the potential cost of their failure. Historical data, such as environmental and operational data, is used to create an inspection plan. This strategy requires close monitoring of MRO inventory to ensure all necessary parts are available while minimizing rogue spending on excess parts
Condition-based maintenance
As the name suggests, condition-based maintenance only happens when certain indicators reveal that an asset is showing signs of decreasing performance or near equipment failure.
Visual inspections, scheduled tests, and sensor devices can be used to gain insight for making an informed decision.
Using sensors to get pressure readings on piping systems is one example of where condition-based maintenance might make sense. Food and beverage producers who rely on pipe and liquid systems can identify when possible leaks may occur and rectify the issue when and if needed.
This strategy requires investing in the right monitoring tools, though these expenses may be offset by savings in minimized downtime and machine longevity. Condition-based monitoring is most effective when it is used for strategic repairs and replacements, so monitoring this technology closely is critical to seeing a return on investment.
Regardless of which strategy you choose to employ, it all starts with harmonizing your MRO inventory to ensure part availability without overspending.
Establish a maintenance strategy of your own
Collect relevant information and data
The first step in developing a robust maintenance strategy is to collect relevant information and data. Pinpointing problems is the only way to find the most cost and time-effective solutions.
The amount of information you collect may be surprising, or you may be surprised to learn that you have far more to look for than you initially expected.
The more thorough you are in collecting parts, condition, and pricing information, the more targeted your maintenance plan will be. Collecting and harmonizing data across sites is a huge plus here because it will allow you to develop an organization-wide maintenance strategy.You should have information regarding your pieces of equipments’:
- Part description and identification number
- Meantime between part usage
- Cost of onhand inventory
- Safety stock recommendations
- Supplier performance metrics
This is an essential first step, but it shouldn’t have to be repeated. Manually collecting and storing this information in generic systems of record can lead to the same bottlenecks as working pen and paper.
There’s no sense in wasting time and opting for something that stores information you’re required to regularly seek out. Instead, look for maintenance solutions that make this part of maintenance scheduling painless and simple. New technology leverages advanced features that synchronize parts data so that you can capitalize on the information you have across sites within your enterprise network.
With the high number of parts that you have to manage at any given time, having a purpose-built solution that can analyze thousands to hundreds of thousands of SKUs at a given time is crucial to your success.
Put together an inspection checklist and reporting system
Having a materials management platform streamlines your maintenance checks by harmonizing MRO inventory data, standardizing procurement efforts, and maintaining compliance information.
This should standardize maintenance strategies across sites, regardless of who is conducting service or ordering parts. Be sure to detail useable vendors as well to streamline spending and ordering.
Modern solutions capitalize on connecting your team through network visibility of inventory and optimization opportunities through easy-to-use software. Ultimately, these tools can ensure that your team is operating using a standardized process, which is the only way to see results from your maintenance strategy.
Take inventory, for example. A manual system may track inventory at different sites, but if you’re looking to cut costs and keep operations smooth, you can stretch your dollar by creating channels for stocked parts across sites. This helps you avoid running out of stock for necessary parts, allows you to quickly pinpoint where available stock is, and avoids duplicate spend on overstocked parts.
Create a schedule based on your MRO strategy
Now that you’ve collected relevant data and built an inspection checklist, you can create a MRO strategy that works for your operation.
An effective schedule is more than just when to perform certain tasks, but it should also take into consideration how long each inspection is going to take. Inspections may result in downtime, so it’s wise to prepare.
This can be a long process, so leverage as many resources as you can, including asking your vendors and technicians to weigh in. Artificial intelligence and machine learning systems have helped operations across industries keep downtime for these purposes to a minimum.
These solutions elevate scheduling strategies by coupling machinery and parts data with environmental factors, production time, and other circumstance-based specifications that may throw off man-made estimates. If you want to optimize time and cut back on labor costs, these smart solutions are worthwhile investments.
Keep your operations specialists in mind
There are a lot of behind-the-scenes players who keep your operation moving smoothly, so this plan should be just as useful for them as it is for you.
Keep your maintenance staff in the loop at all times in a way that is comprehensive and digestible. They should have easy access to vendor information, maintenance history, and environmental data. This cuts back on downtime because it streamlines diagnosis and keeps engineers one step ahead of the problem at hand.
Similarly, your plant team likely has the most extensive knowledge of your assets. They play a pivotal role when it comes to ordering the right parts, staying in compliance, and troubleshooting with engineers. Developing a strategic relationship between plant managers and vendors is not only beneficial for the purpose of relationship building but can also keep maintenance costs down by bulking orders and consolidating purchases.
Work closely with both stakeholders to make decisions about effective scheduling strategies and input that information into a trusted MRO optimization solution to keep all parties informed and accountable.
Stay prepared for all of your maintenance needs
It’s possible to implement a manufacturing maintenance program using traditional, old-fashioned methods—but it won’t keep you ahead of problems for long.
Investing in the right material management software consolidates data into a single platform so that you always have access to real-time, inventory information at all times, enabling you to optimize system performance regardless of the situation.
End-to-end visibility makes it that much easier to keep parts stocked and maintenance strategies operating at an optimized level.
These intelligent solutions leverage predictive analysis capabilities to generate recommended action items that are in line with not only your maintenance goals but also your cost optimization strategies. Embracing these purpose-built solutions can streamline your operation and keep you ahead of the curve in today’s fast-paced market.
To learn more about balancing working capital and risk with a materials management intelligence platform, download the ebook on overcoming MRO challenges with manufacturing strategy examples today.
[…] it’s also one that can hit you when you least expect it. Leaders can avoid these problems with a working maintenance schedule that is both systematic and executed […]
[…] managers are scheduling maintenance only when needed as opposed to doing it at scheduled intervals. Run-to-failure maintenance only proves to be counterproductive since it leads to more unplanned production downtimes and […]