Increasing Inventory Value with Purpose-Built MRO Technology
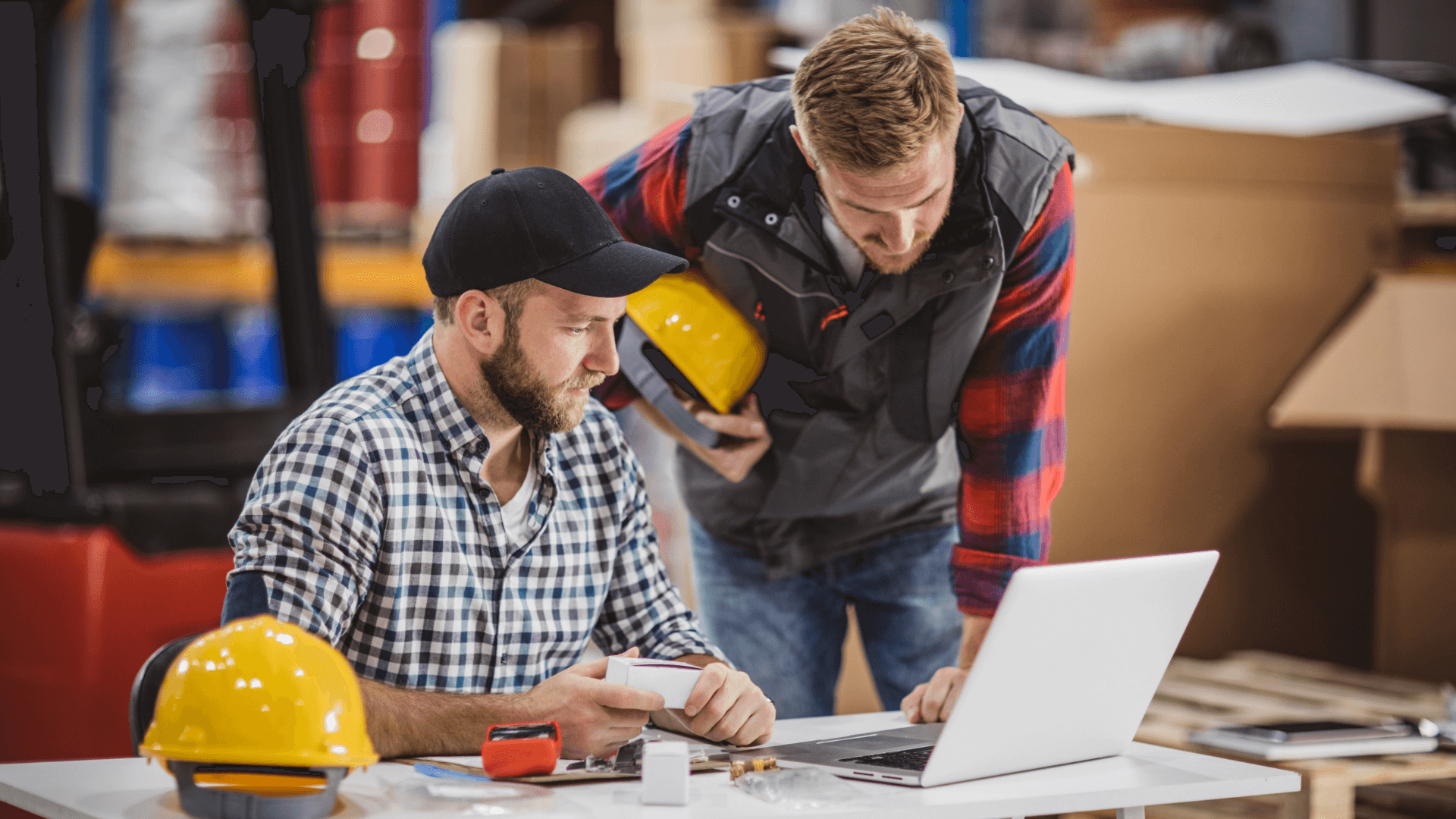
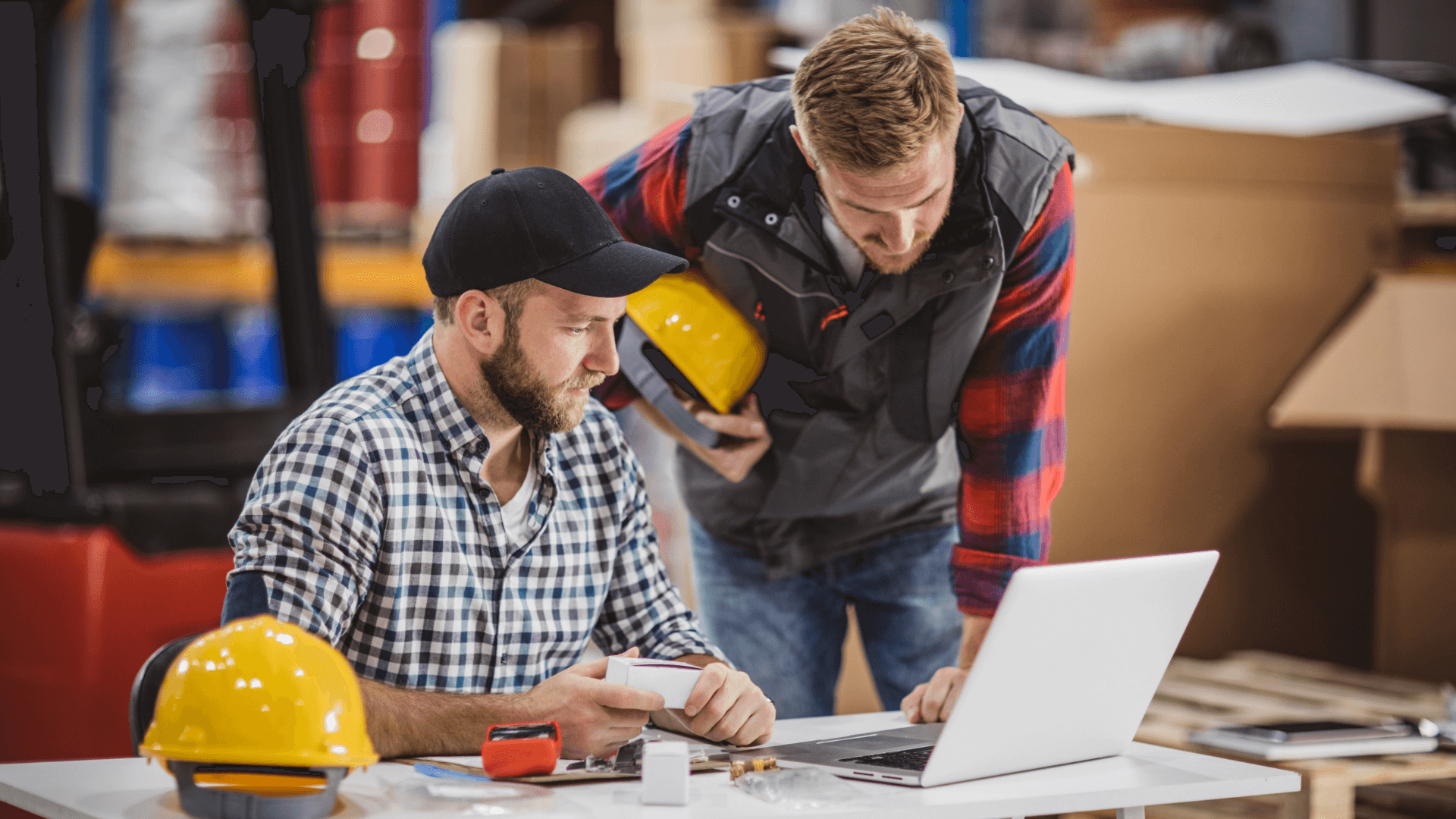
The right MRO inventory management strategy can help operations stretch their dollars and remove overspending. From asset maintenance stock recommendations to strategically using existing inventory across facilities, small changes can offer many opportunities for optimization.
Creating a system that works, however, can prove to be a challenge without the right tools. Data collection and analytics are increasingly becoming the backbone of strategies for procurement and maintenance teams across manufacturing industries. To do this, many are turning to tools built with machine learning and AI-powered data analysis to create lasting, automated process solutions.
Strategic decisions can get more out of existing inventory
Avoid overstocked inventory
When manufacturers carry too much MRO and indirect material inventory, it can lead to increased storage and handling costs, as well as the potential for waste spend. It is an inefficient way to invest capital and doesn’t contribute to the efficiency of daily operations.
Instead, manufacturers need to strategically stock their MRO inventory. This means analyzing inventory purchasing and movement data to determine the optimal amount of inventory to carry. This ensures manufacturers can keep the appropriate MRO and spare parts on hand for when they need it most.
Proactive and ongoing MRO inventory analysis is crucial for ensuring that organizations can see the full potential of their assets and inventory spend. With robust MRO and indirect inventory optimization software, teams can better plan and manage their inventory, aligning procurement strategies with lean maintenance schedules. This can reduce downtime and improve productivity while avoiding the need for overstocking on parts inventory.
Increase access to inventory data
Purpose-built MRO and indirect material management software provides businesses with the tools to overcome data disparities to track inventory levels, monitor procurement data, and analyze maintenance part needs to make informed decisions about inventory management.
Redundant spending can eat away at operational budgets. For teams with data that isn’t harmonized or accessible, however, it is nearly inevitable. MRO and indirect material management software can help maintenance and procurement teams reduce redundant inventory through automated data collection and sharing.
With regularly generated reports on inventory usage and the power of natural language processing (NLP), these tools identify replacement parts that are frequently overstocked or underutilized. It makes it possible for teams with multiple sites to easily share redundant parts across sites, or to avoid further stocking until needed. It kills two birds with one stone, streamlines data and helps teams take the guesswork out of their procurement strategy.
MRO and indirect material management software can also help ensure the operational continuity of assets. Robust MRO software offers real-time information on the status and location of parts, as well as their consumption history. This information can be used to create case-by-case inventory decisions that are based on usage. It reduces the risk of long term unexpected downtime and can help reduce maintenance inventory costs.
Seeing the full potential of your MRO inventory
Improve data collection and sharing
By collecting and sharing data across the entirety of your organization, teams gain greater visibility into their MRO and spare parts inventory levels and use.
Investing in a cutting-edge MRO and indirect materials management solution allows businesses to consolidate all relevant MRO supply data into a single platform. This makes it possible to create processes that are aligned and symbiotic, rather than fragmented.
Standardization offers the piece of mind that information is accurate and up to date and that it can be meaningfully used to make sense of data variances to meet day-to-day needs. Starting from the ground up with these processes is no easy task, and for teams hoping to use manual systems, it can quickly backfire, too.
Tools with more computational power than standard spreadsheets can use AI to eliminate these laborious data analysis practices and even meaningfully translate vast amounts of data into actionable insights using your MRO data as it currently exists.
Strategic MRO inventory management can lead to other savings
Strategic inventory management can lead to significant savings for businesses beyond just reducing inventory costs. By implementing routine maintenance programs for assets, businesses can minimize downtime without increasing maintenance expenses.
An AI-backed solution can analyze previous MRO material or spare part usage, and the make and model of the supply network to accurately meet maintenance needs. Continuous, automated data ingestion makes it possible for organizations to improve MRO inventory levels and reduce the risk of lengthy breakdowns.
Strategic inventory management can also help businesses avoid downtime by revealing where parts are available and accessible regardless of naming convention. By strategically stocking inventory and maintaining accurate records of part location, usage, and replacement schedules, operations teams can ensure that they have the parts they need when they need them.
This can help reduce the likelihood of unplanned downtime due to equipment failure, which can be costly in terms of lost productivity and revenue. By proactively managing inventory, businesses can avoid these costs and keep their operations running smoothly.
Make the most of what’s on hand with a trustworthy MRO solution
In a competitive global market, the biggest mission of an MRO team is to gain the maximum value out of their inventory and assets. Harnessing the power of a purpose-build MRO inventory optimization solution can help companies gain increased visibility, improved resilience, and greater cost savings.
Learn how you can increase inventory value with intelligent MRO and indirect materials management solutions.