How to Determine Safety Stock in Inventory Management: Updating Outdated Methods with New Tools
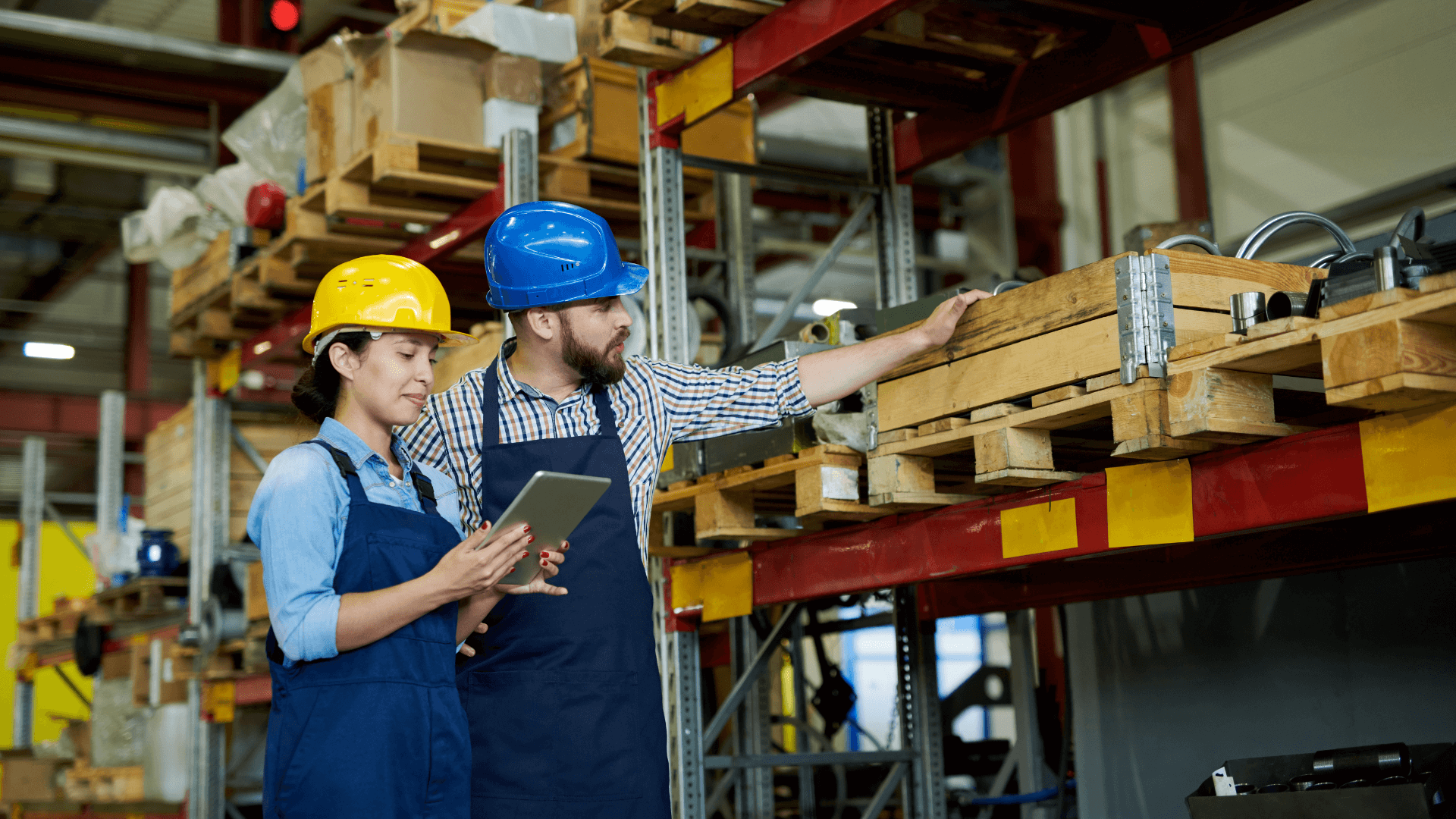
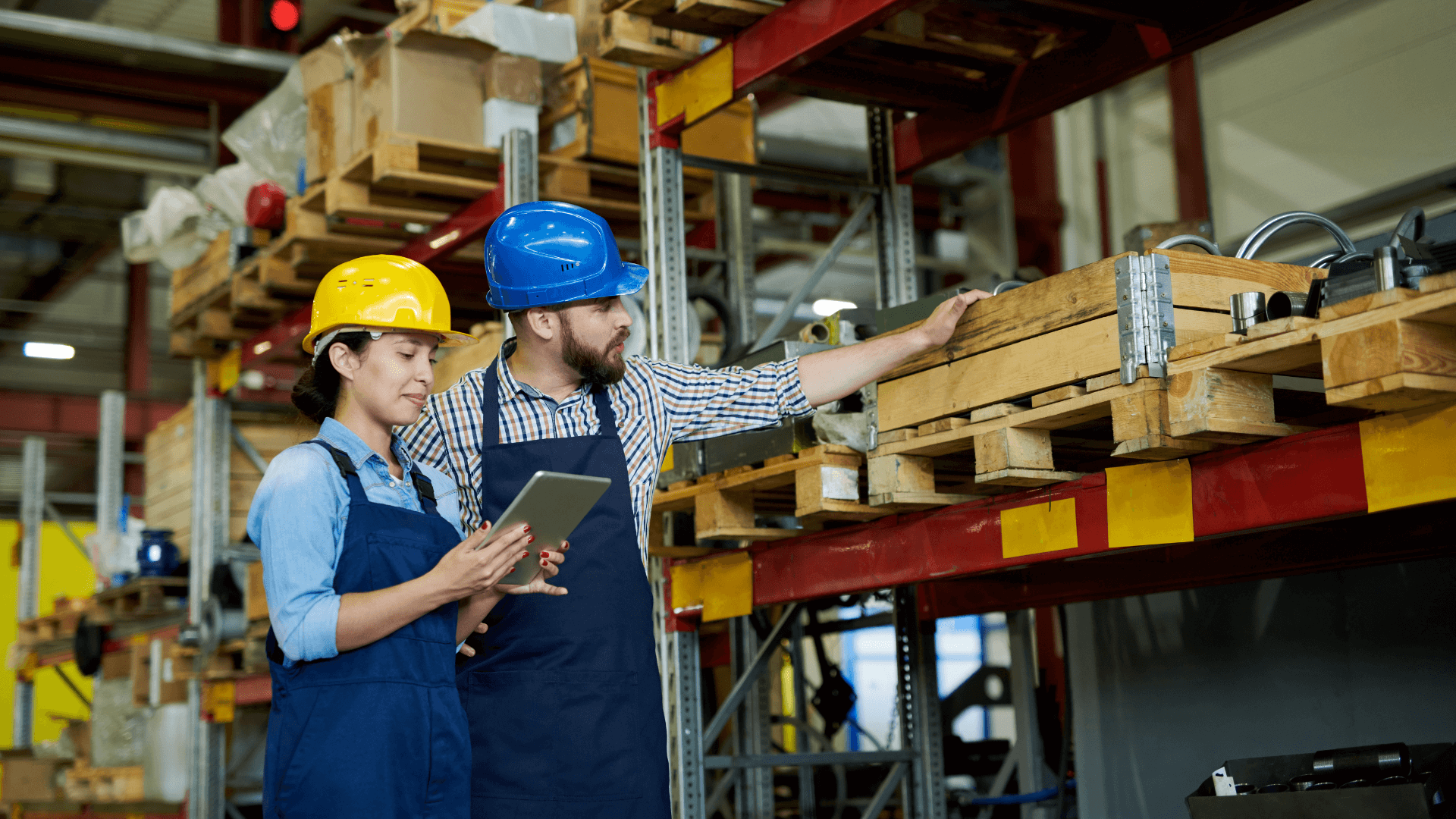
A strong MRO and spare parts strategy is the backbone of any operations efficiency. With so many moving parts and variables that are integral to success, having an effective and efficient safety stock strategy is crucial for being prepared during fluctuations in production.
If managing MRO and indirect materials sounds like one more complex system to manage, it’s likely that your operation is still using manual methods that are outdated and inefficient. Procurement and maintenance leaders across industries are turning to new safety stock methods that leverage cutting-edge technology to make MRO and spare part procurement and management significantly easier, allowing them to focus on higher-priority production concerns like cost reduction and operational efficiency. Here’s what you should know about safety stock in supply chain management and about making the switch.
Ordering enough inventory to keep operations running
From stockouts and shortages to supply chain delays, procurement and maintenance teams learned the importance of MRO safety stock the hard way over the last four years. What started as pandemic-related delays are now inventory overages that many are still working to resolve.
With so much on the line, right sizing safety stock has become crucial for teams to reduce waste without introducing new risk. Calculating a balanced strategy that prioritizes being prepared and cost-effective, however, is no easy task.
Operations teams may turn to traditional safety stock formulas to gain insight into ways to stay prepared. This usually involves performing averages on maintenance data to identify the frequency of part failure and the duration of maintenance downtime. Having these averages on hand makes it possible for teams to determine when replacement stock is needed, and in how much quantity.
Unfortunately, the data needed to run these analyses is typically filled with gaps or poor governance, making it impossible to determine what the right amount of MRO materials is needed. Adopting technology that is purpose-built for MRO, spare parts, and indirect material management is key to streamlining your inventory needs.
The drawbacks of traditional safety stock methods
Many of the traditional methods for establishing your safety stock have their drawbacks, in fact, there are specific issues that may crop up depending on the chosen method, but the broad strokes are similar.
Traditional methods of safety stocking often fail to adapt to changing demand and asset maintenance needs. This includes increased maintenance that is the result of frequent wear and tear, required parts replacement for safety compliance purposes, or new procurement negotiations.
A failure to account for these multiple variables means that traditional formulas often fall flat, failing to be responsive and instead forcing operations to become reactive instead of proactive. The result is unplanned downtime and a scramble to find the right parts due to complicated maintenance solutions.
On the other end of the spectrum is overstocking safety supply for MRO. This strategy grew in popularity during the pandemic, when stock shortages were common. While this may leave your operation with plenty of spare part inventory to work with, it also unnecessarily ties up capital and storage space where it is not being used.
MRO software that can accurately determine safety stock
Leveraging a purpose-built MRO solution to help make the right inventory management decisions can put your operations team ahead of the curve. Unlike traditional formulas, these tools are can use data that comes directly from your maintenance and procurement systems to generate tailored recommendations and actionable insights for your existing materials, all without needing to clean your data beforehand.
Automatic data collection and processing powered by machine learning
A purpose-built MRO solution is integrated with the newest Industry 4.0 features, including an advanced deep-learning AI system that supports your decision-making. Equipped with the capability to analyze past MRO data, maintenance records, or vendor information, the easy to use solution can help predict inventory needs as they change and adapt.
Keeping track of your current inventory is easy, too, as the AI provides real-time monitoring of your stock and helps simplify the ordering process for MRO items when stock levels are low or need to be adjusted.
Actionable insights backed by cutting-edge technology
Part of creating an effective safety stock strategy is having a reliable and consistent maintenance approach. This means that maintenance and procurement teams need to come together to align strategies and stay ahead. Advanced MRO software can help mitigate the challenges that arise in doing this.
Purpose-built MRO software solutions use existing MRO data to accurate determine inventory needs based on purchase history and consumption data. It not only recommends where overages can be reduced and shortages exist, the artificial intelligence eliminates the need for a traditional data cleanse prior to running the models.
All of this information is easily collected and stored in a cloud-based system to keep processes standardized and reduce data silos. It makes reporting across departments effortless and reduces the risk of miscommunication, all while ensuring that your safety stock strategy is effective from a cost and performance standpoint.
Elevate your inventory management strategies with MRO intelligence
Investing in the right tools for your operation will play a vital role in reducing the costly risk of unplanned production downtime and wasted working capital. A purpose-built MRO solution can guide your operation toward a smarter, more resilient strategy for your MRO inventory needs. With increased operational visibility, meaningful insights, and optimization strategies based on your operation’s maintenance and downtime history, there’s no need for manual-based, one size fits all approaches that are ineffective. Learn more about optimizing your MRO strategy today.