How to Reduce Manufacturing Downtime in Production (While Making the Most of It)
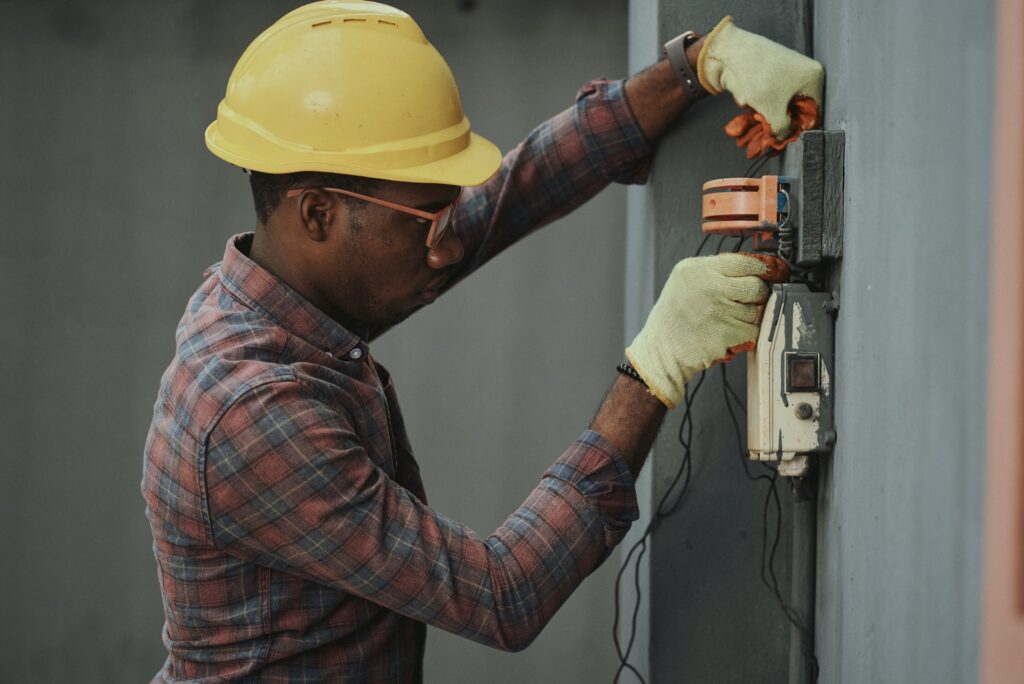
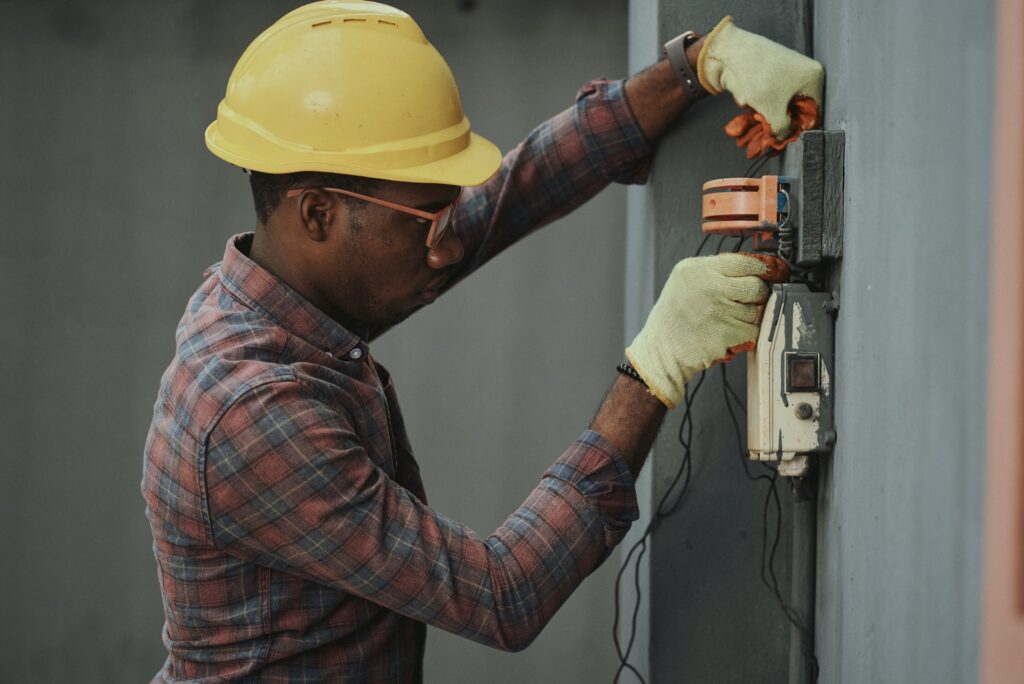
Production downtime is inevitable for any manufacturing company, but minimizing unscheduled outages is especially critical in these delicate times.
No matter how technologically capable the supply chain process becomes, there will always be a time when a manufacturer must stop production lines to conduct routine and emergency maintenance or upgrades to existing systems.
When manufacturing downtime is unplanned, the costs can be detrimental to your company’s bottom line. One report of the cost of unplanned downtime noted that in IT and manufacturing organizations, they could lose up to $108,000 every hour during downtime depending on their scale of operation.
The manufacturing downtime costs are even higher in other industries. For example, downtime in the auto industry has been calculated to cost $22,000 per minute. Moreover, almost every factory experiences at least a 5% loss in production capacity due to unscheduled downtime, some may lose as much as 20%.
Several factors can contribute to a halt in production. Some include operational error, equipment maintenance, MRO supply shortages, or outdated hardware or software. Production downtime facilitated by breakdowns in operations is common but very costly to not only company profits, but company risk as well.
In this article, we will examine how to reduce downtime in production and increase productivity with solutions to prepare for and prevent these expensive events. Even small supply chain management organizations with limited capital can reduce the possibility of unforeseen manufacturing downtime in production with the reduction strategies and measures listed below.
A Short List of Steps You can take to Reduce Downtime in Manufacturing Production
Increase your end-to-end enterprise visibility
Data capture technology in conjunction with AI-powered inventory management software allows leaders to see manufacturing and service status in real-time.
Effective software utilizes KPIs to track inventory and presents that data in a digestible format to end-users and decision-makers. Moreover, many solutions can track downtime events, the first step in reducing the resources lost should this occur.
In a modern supply chain and manufacturing environment, visibility over operations and the MRO materials needed to keep them running is vital to company success; it grants your business the ability to make ongoing data-driven decisions that reduce time lost and predict future interruption. Critical company processes like addressing production halts immediately or optimizing MRO stock levels can eliminate hours of lost time and resources.
Despite recent technological advancements leading to end-to-end (E2E) production visibility, supply chain leaders recognize the limitations these services have when stacked up against disruptive world events. Businesses adopt technologies that allow them to thrive in rough conditions and bolster through disruptions to survive in a modern supply chain ecosystem.
Fortunately, increased visibility helps businesses predict and manage the day-to-day disruptions that are often encountered. Maintenance or system upgrades are common disturbances that can be optimized via intuitive visibility tools to remove the hassle and wasted time.
Upgrade your out-of-date systems
Preventative maintenance is already a process mature companies employ to reduce manufacturing downtime., but it is the unplanned failures that lead to devastating outcomes. When this occurs, an operations team must be able to quickly respond and know what materials are needed to get production back up and running. Since every second lost is wasted capital, the speed of this response is essential to your business’s bottom line.
Upgrading your systems is a crucial step in keeping this response rate swift. Newer systems are, by default, less likely to fail, preventing unexpected downtime from occurring in the first place. However, investing in other cost-saving measures can save you money in the long term.
For example, utilizing IoT solutions with sensors monitoring your equipment gives your supply chain manager a warning in the case of mechanical overload or failure. Or installing novel software systems for increased functionality and security. But equipment monitoring is only one area that requires your attention. You must also know what MRO materials are available at all times to ensure you have the right parts on hand.
Sometimes upgrading your system requires an internal change. Companies must form a habit of recording system maintenance requirements, establishing standard operating procedures, training maintenance crews, developing downtime records, and tracking MRO items to reduce the risk of unscheduled downtime and optimize preventative maintenance.
Even the most transparent companies use a variety of software and hardware that make handling multiple systems difficult for supply chain managers. When this inevitably occurs, machine-learning-powered software can be your saving grace in untangling the web of contrasting systems and complex data.
Take the time to perform preventative maintenance
We have explored the reasons for supply chain downtime, but what do businesses forfeit when this occurs? Often these downtime occurrences result in lost employee productivity, no item production, rescheduled work hours, repair costs, customer complaints, tarnished brand and reputation, and overall reduced service capabilities.
Downtime must be considered a capital loss if companies are to instill the sense of urgency that is required to prevent future outages. Historically, to reduce wasted capital companies have engaged in regularly scheduled maintenance, but they often overlook the MRO inventory levels existing throughout the enterprise.
A good start to preventative maintenance is risk auditing. Risk auditing is one of the quickest and most cost-effective ways to analyze and plan for future maintenance. Risk auditing can find weaknesses in your supply chain, like obsolete equipment, so you can address them with data-enabled solutions.
Utilizing shorter periods of planned downtime to service equipment or upgrade systems can limit manufacturing downtime. It can also reduce labor costs and effort for team members tasked with solving the issue; especially when a part is out of stock or not easily accessible, making on-demand service more difficult.
The advantages of planned maintenance aren’t theoretical, research has shown that this tactic improves equipment availability by 5-15% and reduces costs by up to 25%.
Set your business up for success
Reducing and planning downtime within your supply chain can protect you from pesky bottlenecks and unforeseen logistical anomalies. Similarly, if you don’t take any method to prevent downtime, it could cause far-reaching damage to your manufacturing enterprise. These strategies are proven methods for removing downtime-related mishaps and saving your company money.
Increasing visibility, upgrading systems, strategically managing MRO inventory levels, and scheduling preventative maintenance all work in conjunction to protect you from unplanned disruptions. Managing your downtime doesn’t have to be a hassle if you use AI-driven software; much of it is already done for you and easily accessible so that your team always has the information they need. Ensure the safety and success of your business by implementing these modern solutions, like Verusen’s AI and machine learning platform. By considering the factors listed above, businesses can do just that, and minimize supply-chain disruption while adding value through smart management practices. To learn more about reducing supply chain risk through MRO optimization, download the white paper on MRO optimization today.
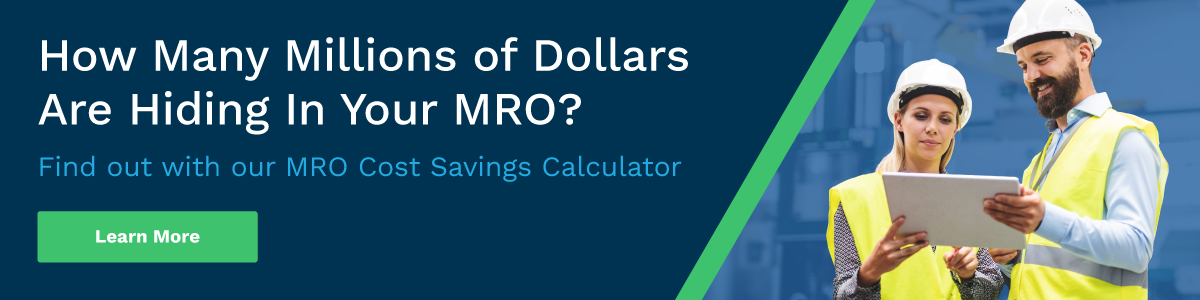
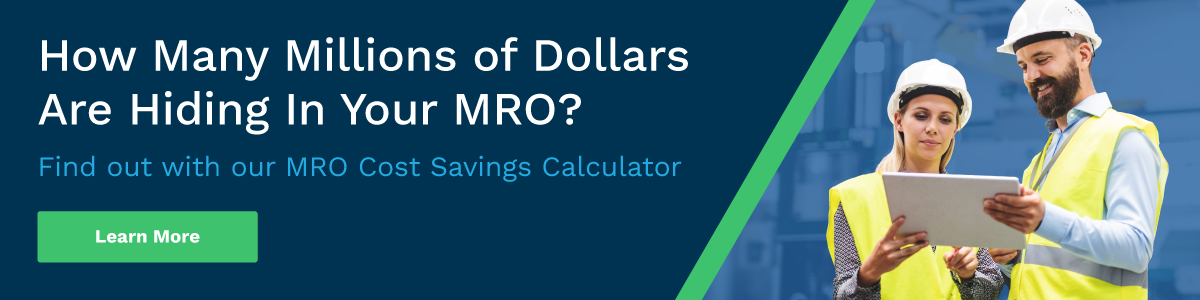
[…] instance, unplanned production downtime is not only one of the biggest disruptors of manufacturing operations, but it’s also one that can […]
[…] intervals. Run-to-failure maintenance only proves to be counterproductive since it leads to more unplanned production downtimes and reduces the lifespan of company […]