7 Ways to Revolutionize Your Inventory Optimization Process
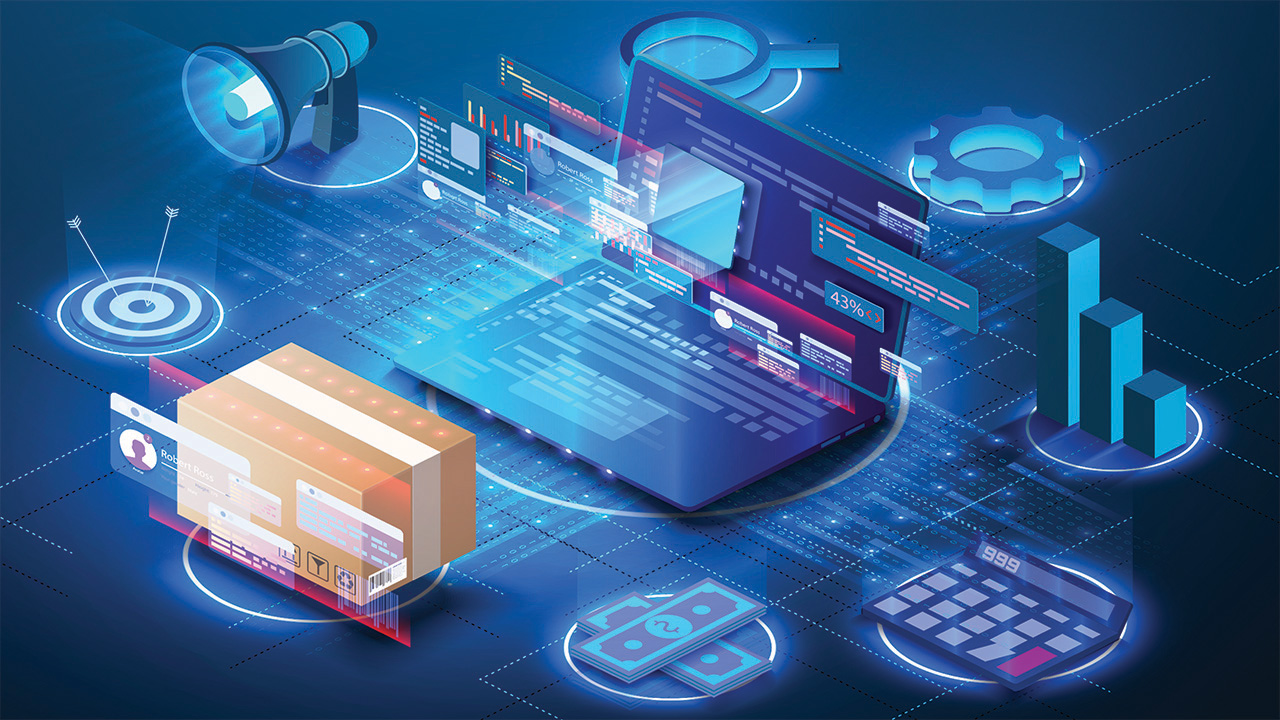
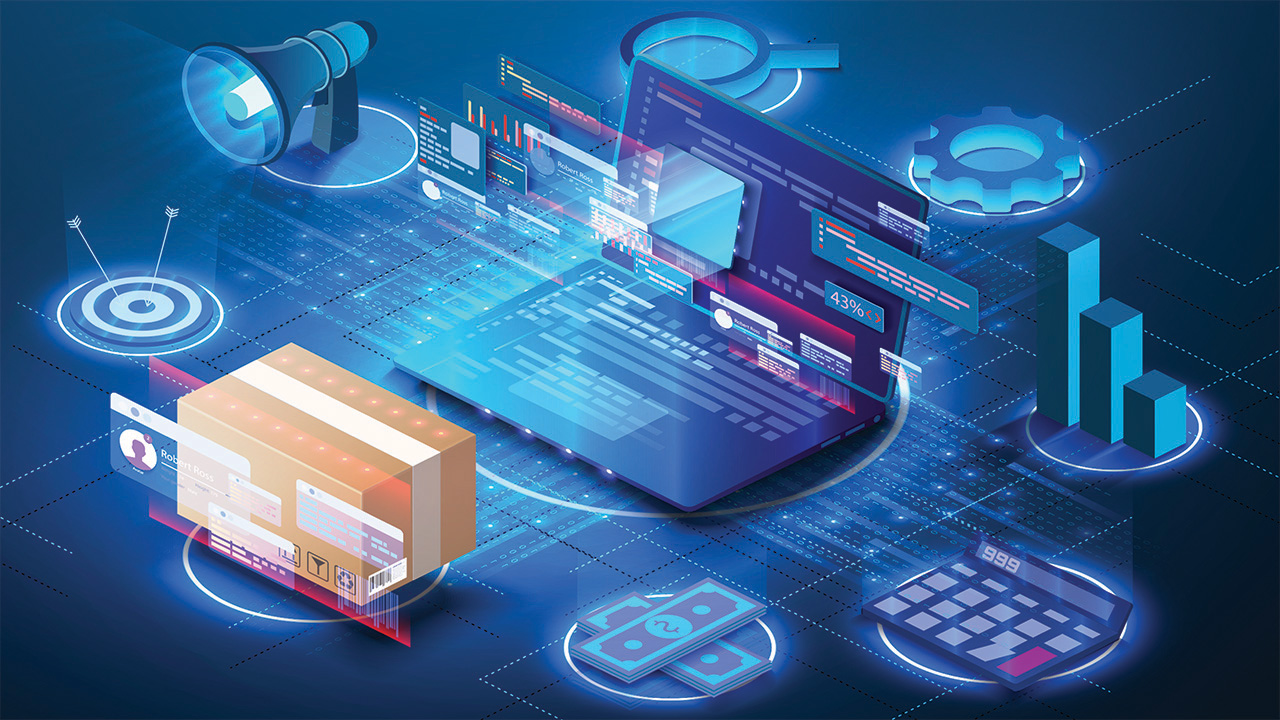
Regardless of the size and shape of your business, a system of inventory management that can view all parts of the flow of products and services is key to smooth operation.
But to keep your inventory management effective, you need to undergo inventory optimization from time to time. This way, you can reduce the amount of working capital tied up in inventory, while making sure you’re meeting supply.
Here are seven ways to make sure your inventory optimization efforts are getting you the results you need for increased inventory flow.
Why is supply chain inventory optimization important?
There are several key reasons why inventory optimization in supply chain is encouraged regardless of industry. After all, a process of creation, manufacturing, and sale is what makes most businesses run smoothly.
Eliminating supply chain variability
With better visibility of the material that needs to be procured, production cost forecasts, and service requirements, inventory optimization could lead to more efficient operations, reduce transportation and production costs, ensure a steady flow of production, and also ensure that the product reaches the market, and customer, well in time.
The costs for storing, carrying, holding, and managing material is ever-present and if not looked into, ever-growing too. Inventory optimization is a great way to save and store effectively.
Additionally, making sure and staying on track of a schedule of delivery and procurement from vendors regularly is far more effective than expediting an emergency material shipment from a vendor.
Inventory planning
Instead of hoarding and potentially storing materials that you don’t even need, it is best to have an automatic calculation of time-based inventory to reduce excess product storage.
These can be done by optimizing by location and having a certain unit of safety stock per material used. This helps accelerate inventory turnover, prevents obsolescence, and saves remarkable amounts of space for extra storage.
Costs and finances
Optimizing inventory processes can enable you to decrease the amount of capital being used for production while improving the service level provided. It allows for time to study and deliver on what consumers want and in the time that they want it in without holding too much material.
This helps reduce inventory fill-ups by 10%-30% and is usually a great financial change and motivator for businesses. Money saved is money earned, and it provides chances to use that money to improve other areas of work.
Customers and employees
With better inventory optimization, your delivery and service times will be improved, satisfying a lot of clients and keeping them happy. This drives customer loyalty through the roof of your warehouse — with no damage to the actual roof — and helps market your business in unexpected ways.
For the employees of the business, it is typically important to believe in what they work for, and knowing decisions that make processes of creation more sustainable, beneficial, and reality-based can provide a sense of comfort and confidence in your employees.
Top tips for improving your inventory management
If not the benefits of inventory optimization that lure you into ensuring you manage and optimize your inventory to watch your work grow in unexpected ways, the ease with which inventory optimization can take place might help you motivate yourself in that direction.
Enable real-time inventory visibility
This isn’t as complicated as it sounds and primarily entails knowing what you own, what you store and where, and how to procure more of it.
While the hoarding and overstocking of some material can render it obsolete, these same materials may be used by another business with another motive to create and fulfill their inventory demand.
A lot of waste can be reduced if inventory systems are studied carefully to know which sister facility needs how much of each material. This requires internal teamwork to ensure all communication is clear and needs are met.
Implement global materials search capability
Access materials across your enterprise for a full, real-time view of on-hand inventory; think Google but for your inventory. This enables you to find parts even if two plants use different names for the same asset, and ensure a smooth handover as well as optimum use of already procured materials, minimizing waste, time spent on procurement, as well as capital.
Understand material demand signals
A concrete understanding of how the various teams across all departments and divisions communicate and make decisions about shared or exclusive inventory is key to ensure all demands for material are met.
However, this can prove difficult, especially when departments utilize varying systems or tracking elements, or struggle in general to pass data between them, or to unite this within a central environment.
While creating this level of communication may initially require an exhausting overview of existing systems – as well as daily tracking of movement and procurement of all materials – it can prove immensely fundamental in the smooth running of inventory.
Getting started with this process can be made easier through the use of material optimization software, as this can utilize technological solutions, such as artificial intelligence, to carry out some of the data-heavy lifting for you.
Understanding material demand – as and when it arises – can simplify the procurement process, keep you on-schedule, and ultimately avoid timely delays.
Implement AI-driven predictive demand
Once the strategic overview of pre-existing inventory and practices of procurement are in place, the management of company-wide intra-department materials – and the goal of storing clean data – can be initiated.
At a basic level, this means knowing how and what to do with all the information you have gathered – that is, how to effectively manage your inventory.
This is exactly where Verusen’s materials optimization platform, powered by AI-driven insights, can take over and help you achieve all the goals you have set for your inventory.
With the ability to compile and analyze material-based data across multiple systems in order to make real-time information accessible, Verusen’s platform has the capability to improve communications, making essential information accessible to managers across departments and plants, ensuring smooth operations.
An effective platform can stop the over-ordering and overspending of materials within a matter of days and is a highly sophisticated outlook on inventory management and optimization which considers real-time delays and possibilities of risks based on materials through all production plants.
Partner with your most strategic suppliers
To reduce risks and costs when it comes to primary supply bases, identifying and partnering with strategic suppliers can be a fundamental step to success.
As a primary function of purchasing and storing, these partnerships can then be used to proactively tackle supply disruptions, or other complications and hurdles in the supply chain for inventory.
Having suppliers as partners who are within strategic convenience of distance and cost for the production plant is key, and this may differ for each warehouse. While communication with suppliers can prove difficult – especially if mediating across multiple data systems – this can be another way in which material optimization software can bridge the gap.
One of the biggest and more rewarding results of this is the creation of a long-lasting production-based partnership that thrives on communication and collaboration in critical service timespans.
By better understanding your demand, and better relaying this accurately and in a timely manner to your suppliers, increased understanding all round can occur and play a key role in optimizing your inventory.
Optimize across your entire supply network
The supply network is, at a basic level, all of your connected supply chains.
From optimizing maintenance, repair and operations, to direct inventory checks, optimizing across the entire length of your supply chain can help to ensure there are no weak links.
Network-wide supply optimization is far more easily achievable when data is clearly visible and systems are synchronized. The power of AI can take this one step further by supporting the process of network-based decision.
Ultimately, clear communication from start to finish helps build collaborative relationships and reduces the chances of waste material.
Reduce operational risk across all functions
One of the basic and most effective ways of ensuring smooth operation and function with minimal risk is through the 6 R’s of Material Management that governs the main principles of purchasing. These include:
Right quality
Quality is typically defined as the capability and power to satisfy a particular production need. The best way to determine quality is to study the intention or final product that is meant to be produced.
Right quantity
Suppliers should supply and buyers must procure only the amount of materials needed to ensure that there is no wastage but also to ensure that production never ceases due to a lack of materials. The Economic Order Quantity is key here and must be clarified at each stage.
Right price
Using effective cost and value analyses should be the first step in determining the actual procurement cost for materials from different suppliers. The nature of competition and demand for the material also greatly influences the price.
Right source
The right source is usually reliable in terms of delivery, quality, and after-sales services; often key to most procured materials in case of any issues that may arise.
Right time
Procuring material when there is no need or production has ceased due to no materials being available are both extremes that must be avoided for smooth operations. While the former gives way to obsolescence, waste, and overstocking, the latter can stop all production due to an issue that shouldn’t have existed.
Right place
The procurement of materials is not over after cost negotiations, but only after the materials have been delivered, securely and in quantities and qualities demanded, to the right location. Directions and instructions have to be clear to avoid mismanagement and confusion of delivery.
Revolutionize your inventory optimization
Verusen offers materials optimization for the modern age, starting with AI-powered processes supported by human expertise to get the perfect blend of flexibility and performance. Start reducing your risks today.