How Technology Can Optimize Safety Stock of Spare Parts and MRO Materials
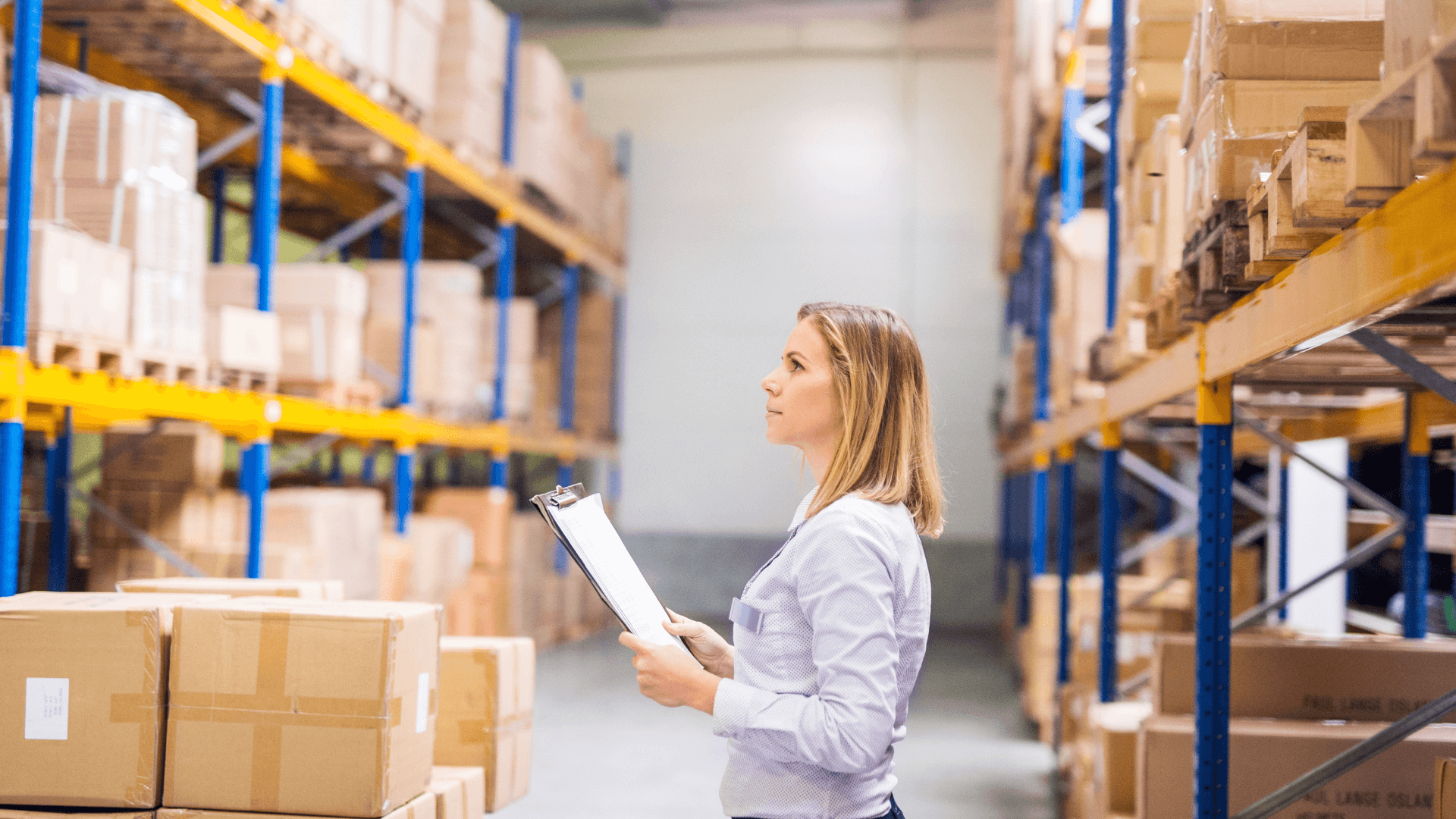
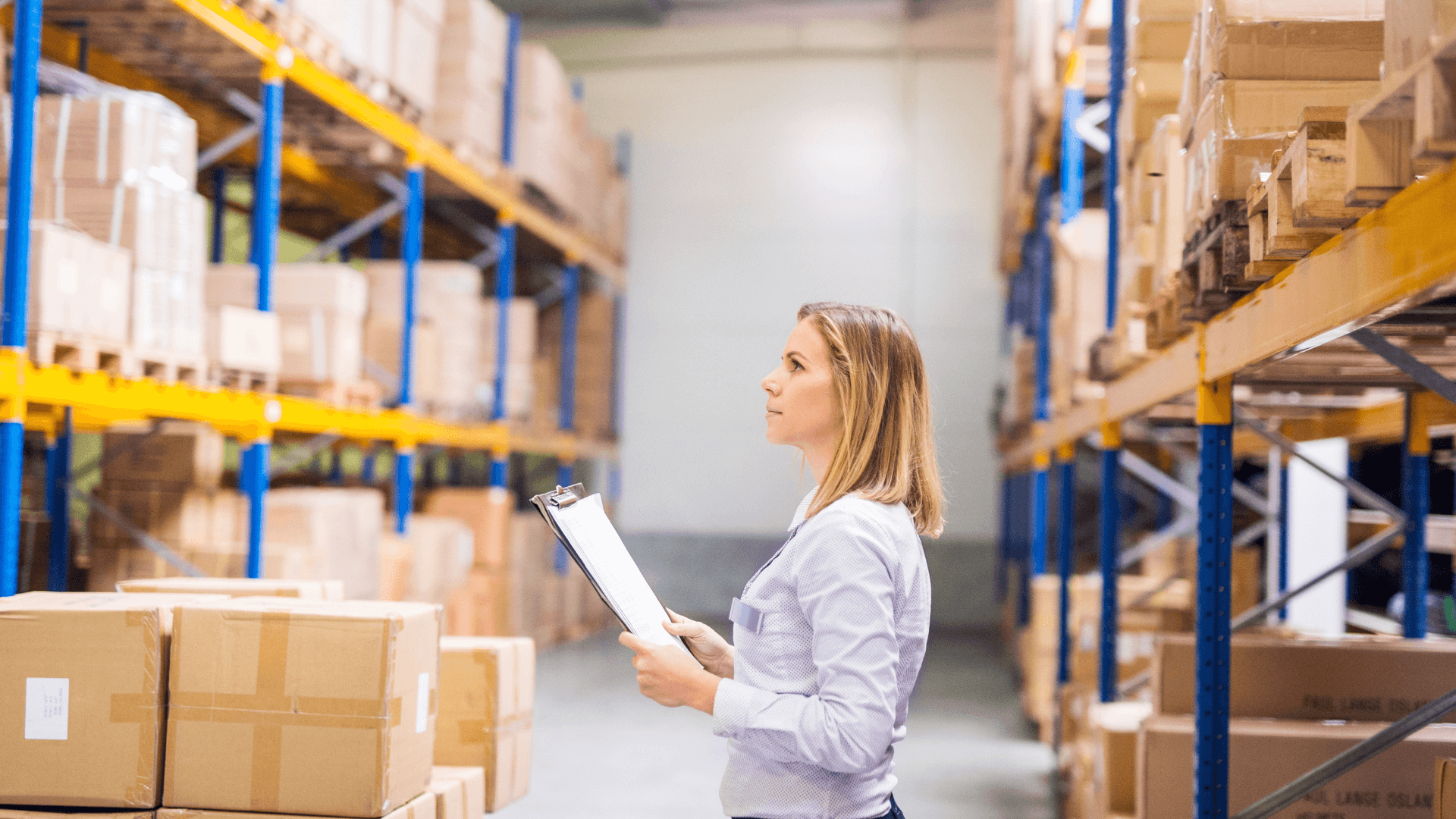
Optimizing safety stock of MRO and spare parts requires understanding different variables that work together to keep your manufacturing operations running. Without a deep understanding of how these moving parts work, and close monitoring of their progress, it can be challenging to identify the necessary steps that need to be taken to start a production line back up in the event of downtime. New digital platforms and data harmonization tools can help you streamline your safety stock more than traditional methods. But before we get into how new solutions are helping, let’s cover the basics.
The traditional safety stock formula
A manufacturer’s spare part safety stock is vital for preventing unplanned and costly downtime. Complex systems of production constantly find their machinery needing maintenance or repair-from worn-out fan belts, lubrication issues, or parts misalignment, the list goes on- it’s the nature of running a well-used asset in production. The inevitability of these repairs makes stocking MRO materials and spare parts that much more important.
Strategically maintaining MRO inventory ensures that parts are on-hand to keep both planned and emergency maintenance swift. Safety stock can reduce downtime by keeping stock on hand to avoid excessive delays that arise from shortages or long supplier lead times. Traditional strategies for building a strategic safety stock are built on a few key pieces of information.
First and foremost, some analysis of your maintenance and operational data is necessary to start with. Finding the average time between failures is necessary for creating routine maintenance schedules and strategically stocking necessary parts. Likewise, having access to the consumption data to replacement parts will also help schedule maintenance and avoid outages during production peaks. This will ensure that your maintenance schedule extends the lifespan of your assets without being costly or inefficient. Both of these values can usually be found in your materials data.
Procurement data will also serve well here. Easy access to average lead time and demand variability will make it easier for your procurement team to work with inventory vendors to keep stock reliably filled without tying up costs in unused excess inventory.
Many use these variables to conduct calculations and help identify the quantity and frequency needed for reordering stock items. However, it’s important to note that this traditional strategy is contingent on a few factors. First, the data that is being used must be harmonized and meaningful, a task that becomes next to impossible when using multiple ERP instances and manual spreadsheet analysis.
Unharmonized data produces unreliable results, which can result in unplanned downtime or stock shortages in a time of crisis. Likewise, it’s also important to note that there are unforeseen circumstances that can arise. Teams may try to prepare for the unexpected by overstocking, but this strategy is often costly and inefficient.
It’s recommended that teams use purpose-built MRO inventory optimization tools to aid in data collection and analytics. MRO tools that help manage data collection and sharing can also aid in other parts of the process, too. Advanced features like machine learning and natural language processing can help maintenance and procurement teams manage these processes across their entire enterprise network.
Upgrading your approach to spare part safety stock inventory management
Traditional formulas can tell operations teams some things, but they certainly cannot offer robust approaches that are resilient and dynamic. Avoiding a one-size-fits-all technique can save teams time and money by ensuring you don’t take a blanket approach to how you manage your spare parts. Here’s how new technology can help operation leaders avoid piecemeal consultations and start optimizing with a strategy that is tailored to their unique operational needs.
Data harmonization keeps things thorough
Keeping your safety stock for spare parts strategically maintained requires frequently updating and maintaining information about your maintenance history and records. This information should always be shared with your procurement and maintenance teams to keep material inventory levels consistent and company strategies aligned.
Data collection in itself can be an overwhelming task. When it comes to collecting information consistently across a number of sites for a range of assets, this is especially true. The process of data collection, too, can feel useless if it’s manual or if it makes it hard for teams to make sense of the information that is being shared. Manual methods can make both of these things that much more difficult.
New tools can automate data collection processes, harmonizing them across the whole organization by using machine learning and AI-powered algorithms to analyze inventory and maintenance data. Trained on the trends of your assets and maintenance needs, these tools instantly make sense of historic and new data as it is collected, helping you make better informed decisions around procurement and operational needs.
Be proactive and cost-efficient
Traditional consultancies and safety stock strategies rely on processes that need to be implemented in staggered phases. This can incur significant costs in the lengthy project times required during implementation, and in the changes that unintentionally arise as solutions are set in motion.
The only truly preemptive solution lies in the hands of artificial intelligence, which learns throughout usage and accounts for system-wide changes in the moment. The results can be seen in most operations in a much shorter timeline than traditional data cleanse initiatives.
With the right tools, your inventory management strategy will be adaptive and keep just the right amount of stock at the right time, saving you money and keeping the process as efficient as possible.
New tools can help you transform traditional strategies
While you can’t always anticipate the unexpected, spare part safety stock can help your operation stay afloat even when unexpected problems arise. Preparing for the worst, however, shouldn’t use up all of your team’s resources. Enhancing your workflow to keep your systems up and running is made easier with an MRO software solution you can trust.
With Verusen, your decision-making is supported by cutting-edge AI and comprehensive data harmonization tools, helping you make the calls to keep your operations and procurement strategies efficient and low-cost. With the best tools in your pocket, there’s no setback you can’t be prepared for.