How Can AI and Machine Learning Streamline Your Obsolete Inventory Accounting?
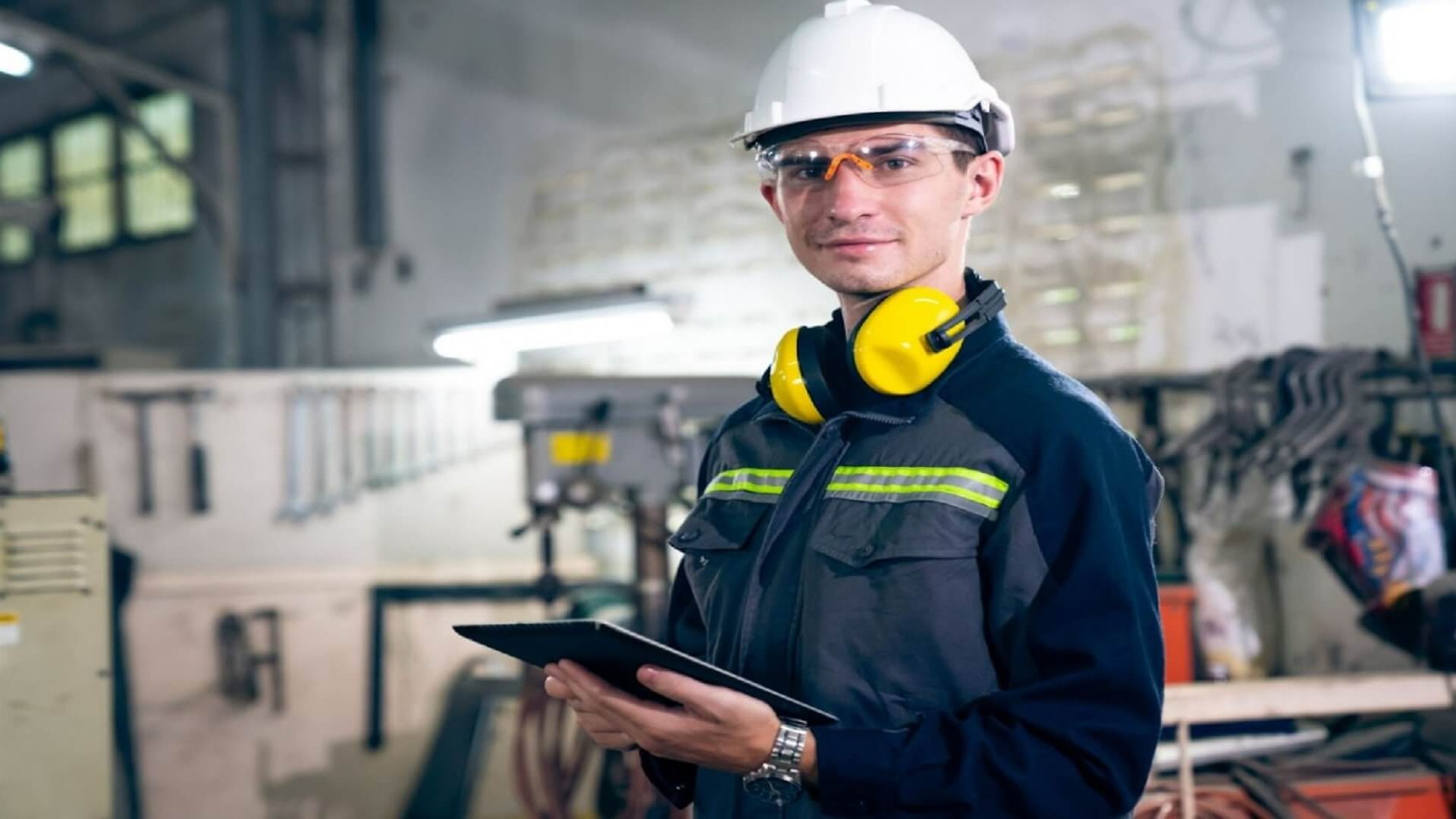
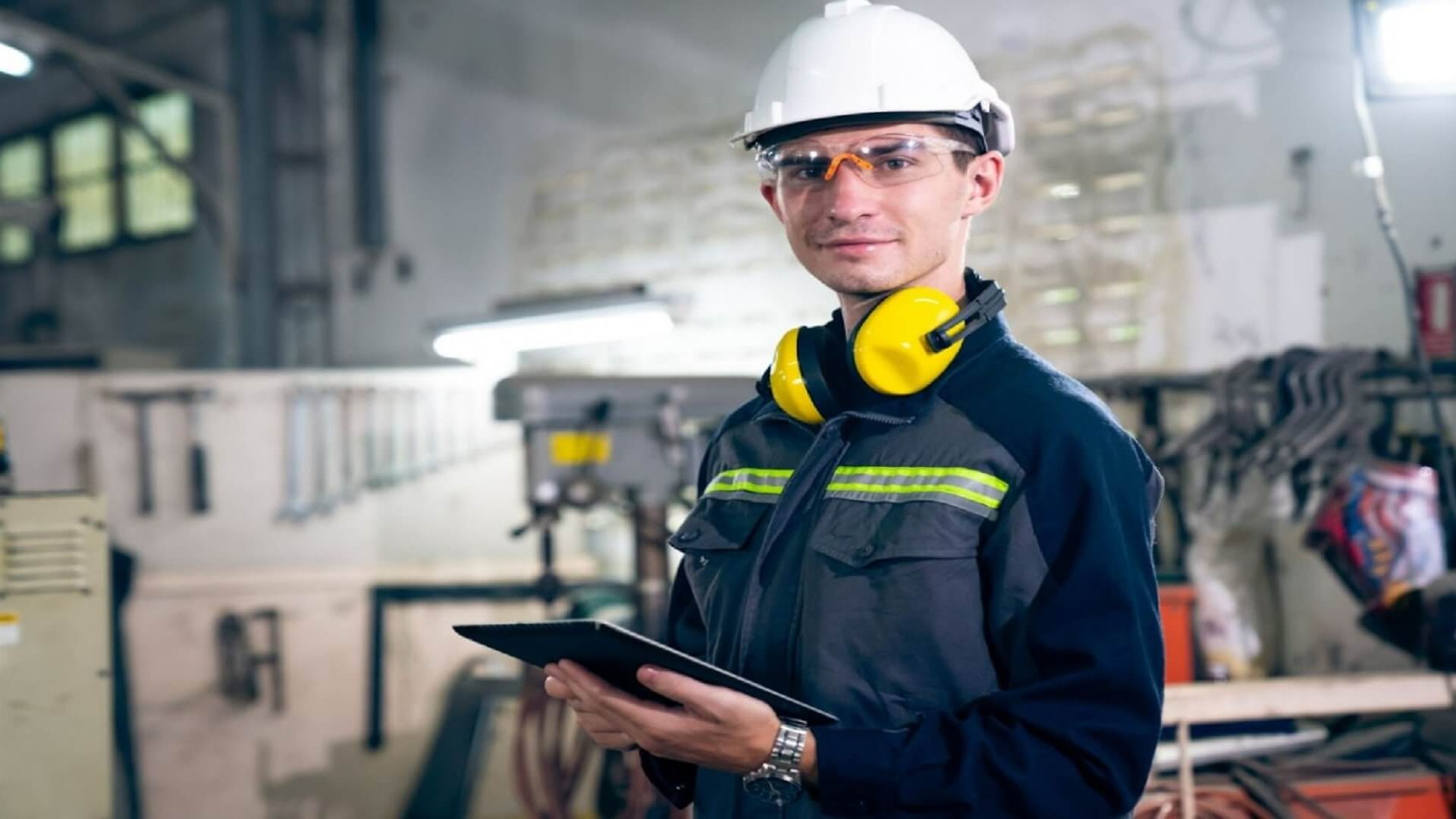
Are you wondering what to do with obsolete inventory? Advancements in modern technology have completely changed the global supply chain landscape and continue to have a massive impact on how businesses operate today. While some business professionals fear that these tools will outperform them and make them obsolete, others are embracing this digital transformation and see it as an opportunity to augment their workforce with new capabilities.
Artificial intelligence and machine learning, in particular, are gaining prominence in the world of inventory accounting and materials management. Organizations have the opportunity to use powerful algorithms to optimize their internal audits, identify areas of risk, and execute many other tasks faster than ever before.
The sustainable benefits that artificial intelligence and machine learning in inventory management have to offer can streamline the auditing process in ways you may not have expected.
Use a modern strategy for obsolete inventory accounting
Keep audits accurate and efficient
By a long shot, the biggest advantage of digitizing your auditing processes is eliminating paper-based, manual systems for good.
These traditional systems are slow, cumbersome, and rife with human error—not to mention that spreadsheet managed data poses security risks, too. Searching for data that is buried or lost in endless rows and columns can be both frustrating and time-consuming.
Though often necessary, it makes reporting and moving inventory inefficient, making it difficult to incentivize departments to consistently stay up-to-date on these processes.
An intelligent system harmonizes data from multiple sites and aggregates them into a single AI and machine learning platform. These super algorithms run through large datasets that traditionally take teams of people hours to sort through. And, what they ultimately return are comprehensive reports that compare harmonized data. It offers access to advanced search criteria at your disposal so that you can find exactly what you’re looking for with a few keystrokes.
AI-proofing your information also means that you avoid the risk of unplanned downtime related to your obsolete inventory, making this a more efficient and reliable alternative to outdated methods.
Increase visibility across sites
One of the biggest reasons why companies experience costly annual write-offs is because they don’t have a realistic look at where their money is flowing. This is yet another reason why gaining visibility into your obsolete inventory is critical. It gives you a holistic view of where your inventory moves and where it doesn’t so you can adjust and optimize where needed.
These data sets return important information about purchasing processes, too. You’ll have information about:
- Which sites are have excess materials or risky shortages
- Average lead times by supplier
- Trends in spending, total quantities ordered, and actual usage metrics
This information catches redundancies and eliminates rogue spending so you can prevent future sunk costs before they happen. In traditional reporting systems, this level of tracking may only be possible on a location-by-location basis, but with digital solutions, all of this is possible on an organizational level.
Digitizing the audit process will automatically create a digital trail of your operations transaction history with less human error. Not only will this significantly bolster the efficiency and accuracy of your materials data, but it also keeps valuable account information secure.
Stop obsolete inventory in its tracks
An easy way to reduce obsolete inventory is by harnessing the power of predictive analysis. It maps purchasing history and performance against market availability to predict future demand, helping you make smart decisions about when to bulk up your inventory.
The powerful algorithms make patterns and yield valuable insight that can help you make informed business decisions to avoid purchasing too much of an item that might become obsolete faster than it can be used.
This especially applies to parts that are frequently used for maintenance. Using forecasts based on predictive analysis, you can determine which parts are needed on hand for frequent repairs, which sites need more repairs than others, and where you can turn in times of emergency.
Leverage the power of AI to streamline obsolete inventory accounting
It isn’t uncommon for businesses to hold excess inventory in the case of emergencies. However, having too much can also backfire—not only do you run the risk of not being able to move excess stock, but auditing the excess spending may reveal a troublesome trend of spare part redundancies across the entirety of your organization.
Together, these factors can significantly impact your bottom line.
Integrating new technologies such as artificial intelligence and machine learning will not only help streamline obsolete inventory accounting but will also facilitate a more responsive and resilient MRO system.
Embracing this digital transformation will revolutionize your company’s approach to inventory auditing.