Materials Management: Avoiding a Supply Chain Data Cleanse Means Huge Savings
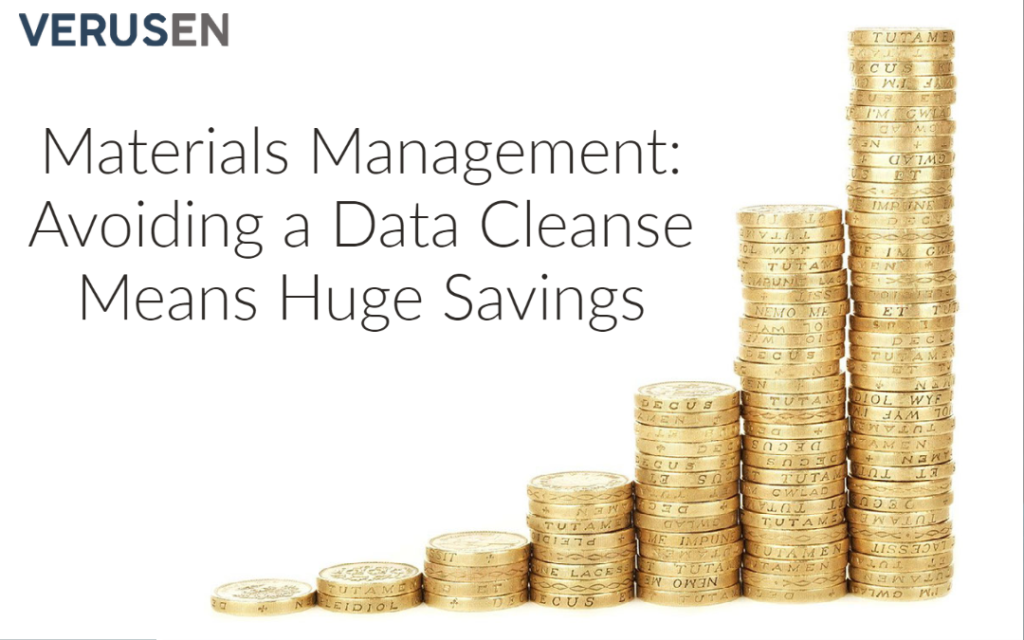
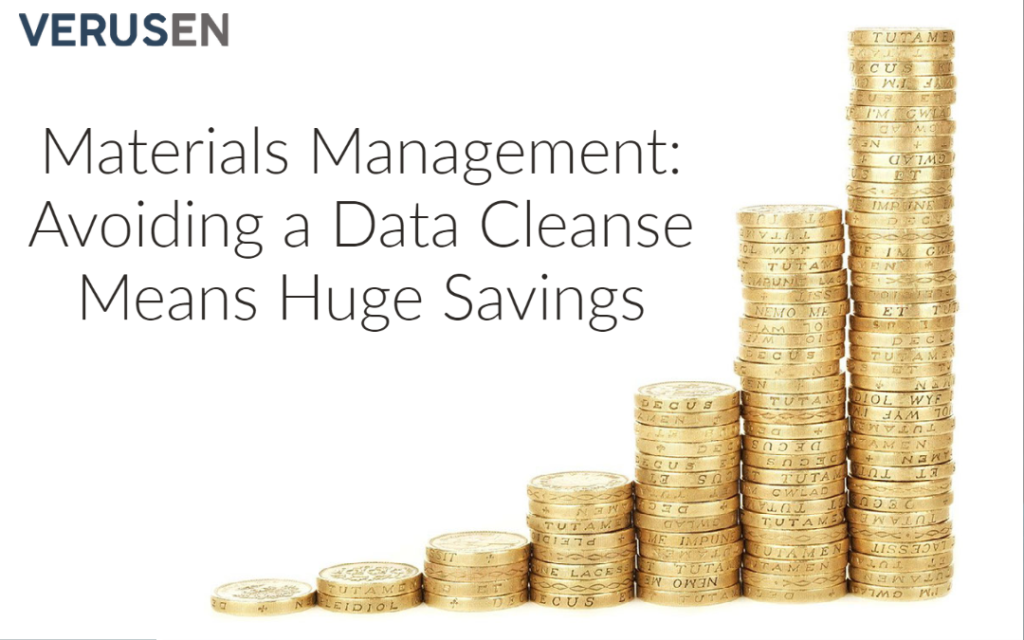
Stop Leaving Money on the Table
Last week I broke down the three usual suspects for dirty data and why a supply chain executive doesn’t need to address that pain before launching their digital transformation project. What I didn’t talk about was just how expensive the legacy data cleanse was and the savings involved by bypassing an old school process with a supply chain digital transformation.
Supply Chain Data Cleanse: Implicit vs. Explicit Cost
Fortune 500 manufacturers are wasting, on average, $50 million in excess working capital. In some instances, that number can be upwards of $100 million for just four weeks of inventory. Having inaccurate materials management inventory data means you’re taking a gamble on unplanned downtime – and given the variety of ‘once-in-a-lifetime’ supply chain bottlenecks from the last 12 months alone – this is a risky play. A recent survey of automotive industry executives placed the average cost of downtime at $22,000 per minute.
What if there isn’t a global catastrophe? That doesn’t mean you’re out of the woods. A technician can’t find a part. Maybe the naming convention is wrong or maybe it’s not actually in stock or even categorized incorrectly due to someone fat-fingering the input. Unplanned downtime costs can come from a variety of bad data issues and they are difficult to pinpoint as more than simply inefficiency in the supply network. These hidden costs mean organizations are leaving revenue on the table by not fully optimizing their supply chain inventory and running with additional risk as well.
The Traditional Data Cleanse Process
Breaking down a traditional supply chain data cleanse really comes down to one of two solutions: An internal process or an external process. The internal resides within the Master Data Management (MDM) or Information Systems (IS) teams. These two teams are typically tasked with providing guidance for strategic opportunities, managing/correcting bad data and an increasingly difficult task of tackling a mountain of spreadsheets.
Externally, companies will hire consulting firms that often rely on offshore resources to brute force data into a clean state. These teams manually check data and clean up inaccuracies before exporting it back into the company’s ERP (or other inventory management system) – a process that can easily take months, and in some cases, years. The real issue here is that clean data has a half life and without major internal process change it will quickly revert to being dirty again.
Artificial Intelligence Emerges as a New Path Forward with Industry 4.0
Industry 4.0 – The new buzzword for what essentially is our fourth industrial revolution – has been pushed by the emergence of our understanding of artificial intelligence and how it can solve problems like a data cleanse in the background while doing so much more. Imagine a system that interprets years of data, identifies patterns, areas of concern and waste and all the while fixes inconsistencies as it finds them. Then taking all that information and packaging it up to be easily digestible by employees where they can either ‘agree’ or ‘disagree’ with the AI recommendations, further training the system. That’s the power behind a modern supply chain digital transformation. Modern supply chain intelligence platforms empowering companies to tackle industry 4.0 initiatives without waiting on legacy issues to be resolved. The result is the death to a traditional data cleanse while reducing risk and saving significant working capital all at the same time.