How Strategic Category Management for Spare Parts Can Make Your Operation More Resilient
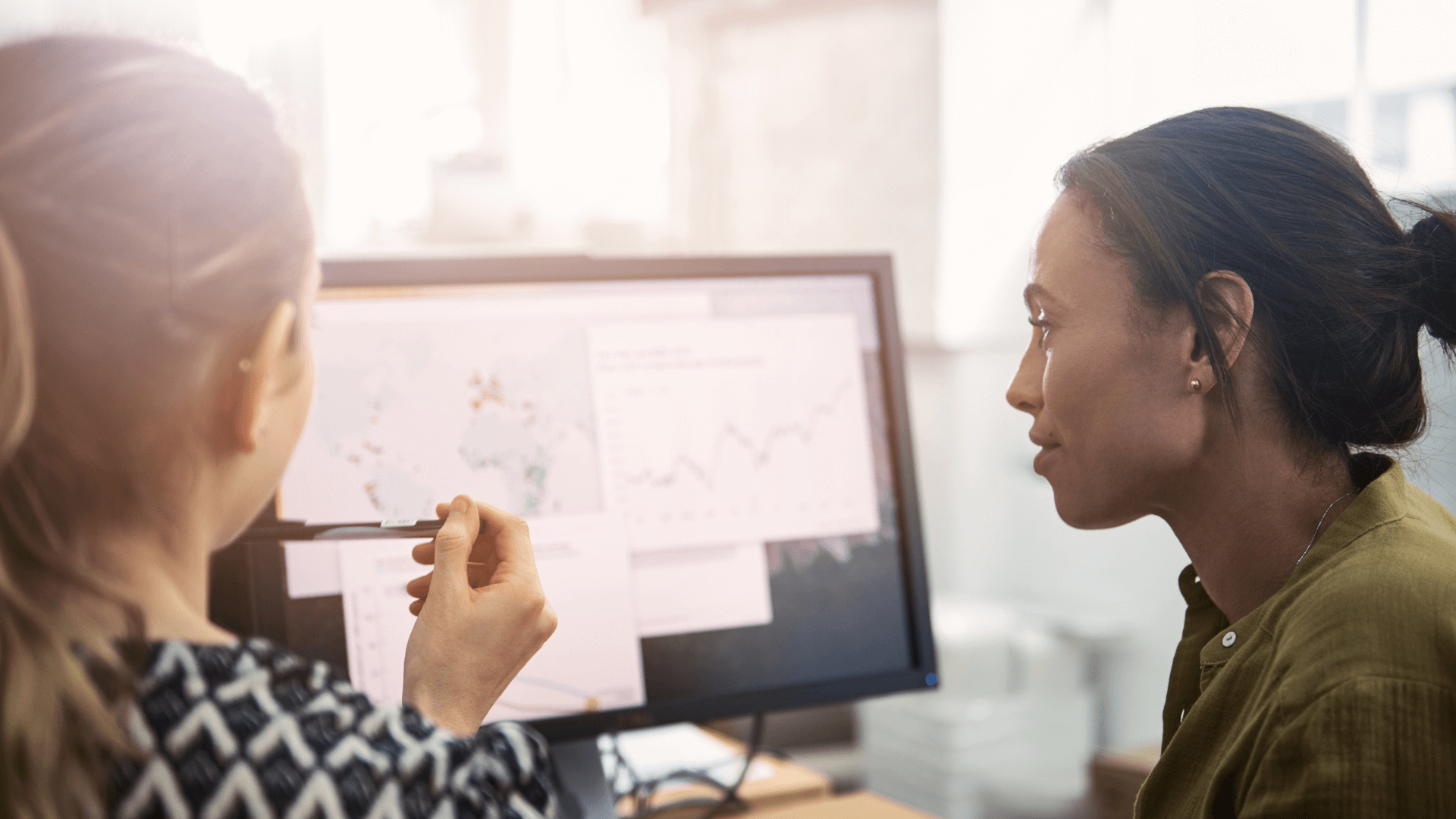
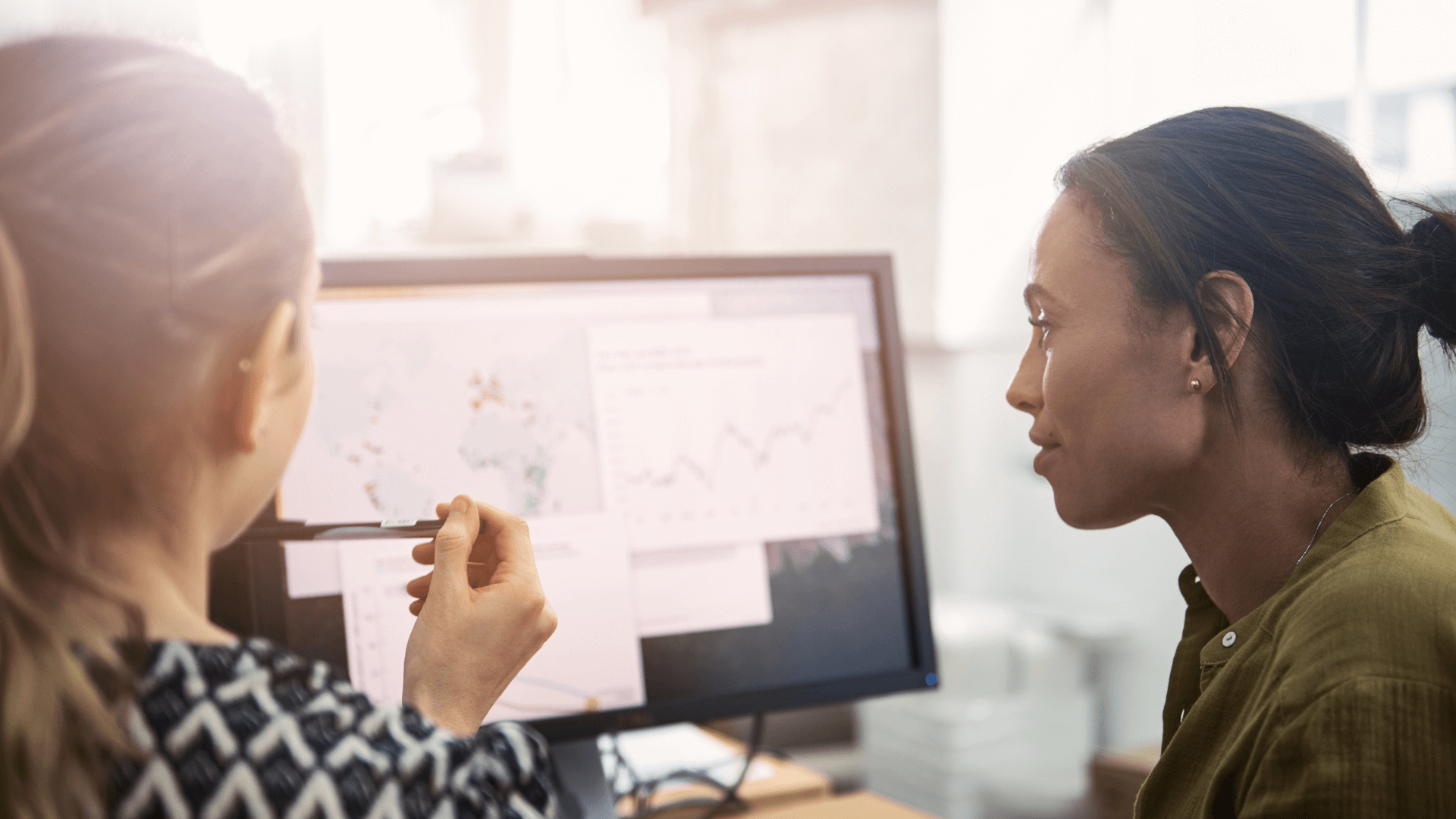
Across industries, experts are turning to strategic category management to keep their spare parts and MRO procurement processes and operations more resilient. A few simple changes can transform the way your operation approaches inventory management, stocking, and more.
Here are some of the best practices for category management, including some tools that can help your team automate the process.
Category management best practices tried and tested by industry experts
Set performance benchmarks to keep things improving
Setting performance benchmarks is crucial in effective category management because it makes it possible to monitor and measure the performance of different aspects of your operation. This includes:
- Supplier performance
- Product quality
- Pricing and volume discounts
- Inventory management
- Min/max stock levels
Benchmarks make it possible to identify potential growth areas and opportunities for cost reduction. The benchmarks should strategically align with the goals and objectives that are set in place, too. When these two measures of accountability are paired together, it makes spare part procurement optimization that much more straightforward.
Organizing data is a must for strategic category management
Organizing MRO and spare parts data by form, fit, and function can help organizations gain insights into their materials management processes, identify areas of improvement, and make data-driven decisions to optimize their operations.
Organized data not only identifies challenges that need to be addressed but also reveals opportunities for reducing tailspend for cost-saving or improved efficiency. For example, organized spending data may reveal recurring incidents of indirect or rogue spending, making it possible for management teams to take corrective action. This sort of data collection and analysis may also reveal high category spend, or identify a need for renegotiating pricing with suppliers.
Organized data helps improve inventory management, too. Keeping track of stock levels reduces redundant spending and unplanned downtime by helping teams locate excess stock, prevent stockouts, and strategically plan for part replacement as needed. This makes it possible for operations teams to reduce inventory holding costs while ensuring that they have the right spare parts on hand to reduce the likelihood of disruptions.
Create a preemptive approach
Creating a preemptive approach in spare part category management can significantly help in anticipating and preventing potential issues before they even arise. This reduces unplanned downtime due to anticipated maintenance needs and other unforeseen events.
Proactive category management includes planning for part replacements with a structured maintenance schedule. Basing your maintenance strategy on data collected from your operation can keep this true to the needs of your assets, rather than wasting money and time on a maintenance strategy that is too cautionary.
Trusted tools can outperform category management services
Make sense of operation-wide data
Cutting-edge materials management software can help businesses consolidate spare parts inventory data into a single, centralized platform. New tools effortlessly integrate with other systems like ERP software and warehouse management systems to provide a comprehensive view of an entire operation. As a result, supply chain professionals can gain a centralized view of company-wide materials which can help them make accurate, data-driven procurement and maintenance decisions.
Gaining real-time visibility across the supply chain means managers can keep track of the performance of different product categories and identify which areas are underperforming or overperforming. Instead of sifting through mountains of manual paperwork, managers have the luxury of making informed decisions on which categories are good candidates for reduced spending and which ones need critical shortages to be replaced.
Coupled with advanced analytics and reporting features, it becomes even easier to resolve issues before they’re made into something bigger. For instance, if stock levels for replacement parts fall below a certain minimum threshold, managers are given recommendations on the appropriate safety stock level. This makes it possible to order a new batch of replacement parts ahead of time, minimizing the risk of delays and disruptions caused due to production downtime.
Build on top of optimization as you go
Companies can leverage artificial intelligence and machine learning to build on top of systems that already exist rather than starting from scratch. These powerful algorithms can analyze vast arrays of data sets and identify trends. The software can not only learn from past mistakes with each iteration but can also simulate accurate models that allow for sharing parts across your network.
Take, for example, asset maintenance. Relying on manually collected data is prone to error. A cloud-based solution, on the other hand, can crunch vast amounts of historical data regarding previous downtime events to construct recommendations for the right amount of spare parts to keep on hand. By giving more attention to spare parts optimization, businesses can cut down on costs and improve asset lifespan.
This makes it possible for organizations to stay agile in changing markets or as business priorities shift. With materials management software, businesses can quickly adjust their category management strategies to meet new demands and capitalize on emerging opportunities.
Resilient operations rely on robust tools
Embracing strategic category management practices and leveraging the power of a materials management intelligence platform to remain competitive and resilient in a dynamic market can help operations teams stay ahead of the curve.
Learn how you can take your category management strategies to the next level with intelligent materials management solutions.