Digital Twins: Technology for the Supply Chain
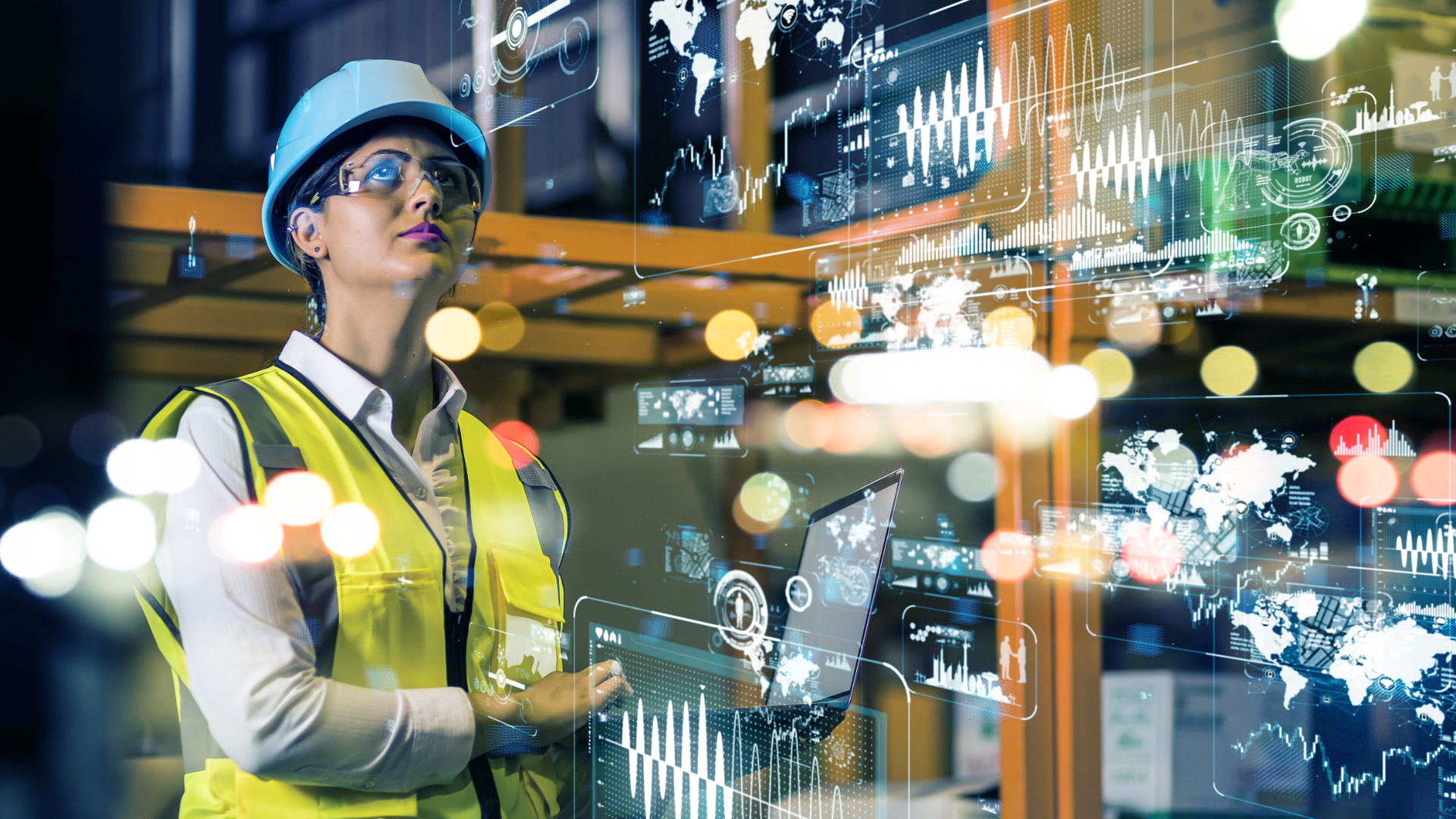
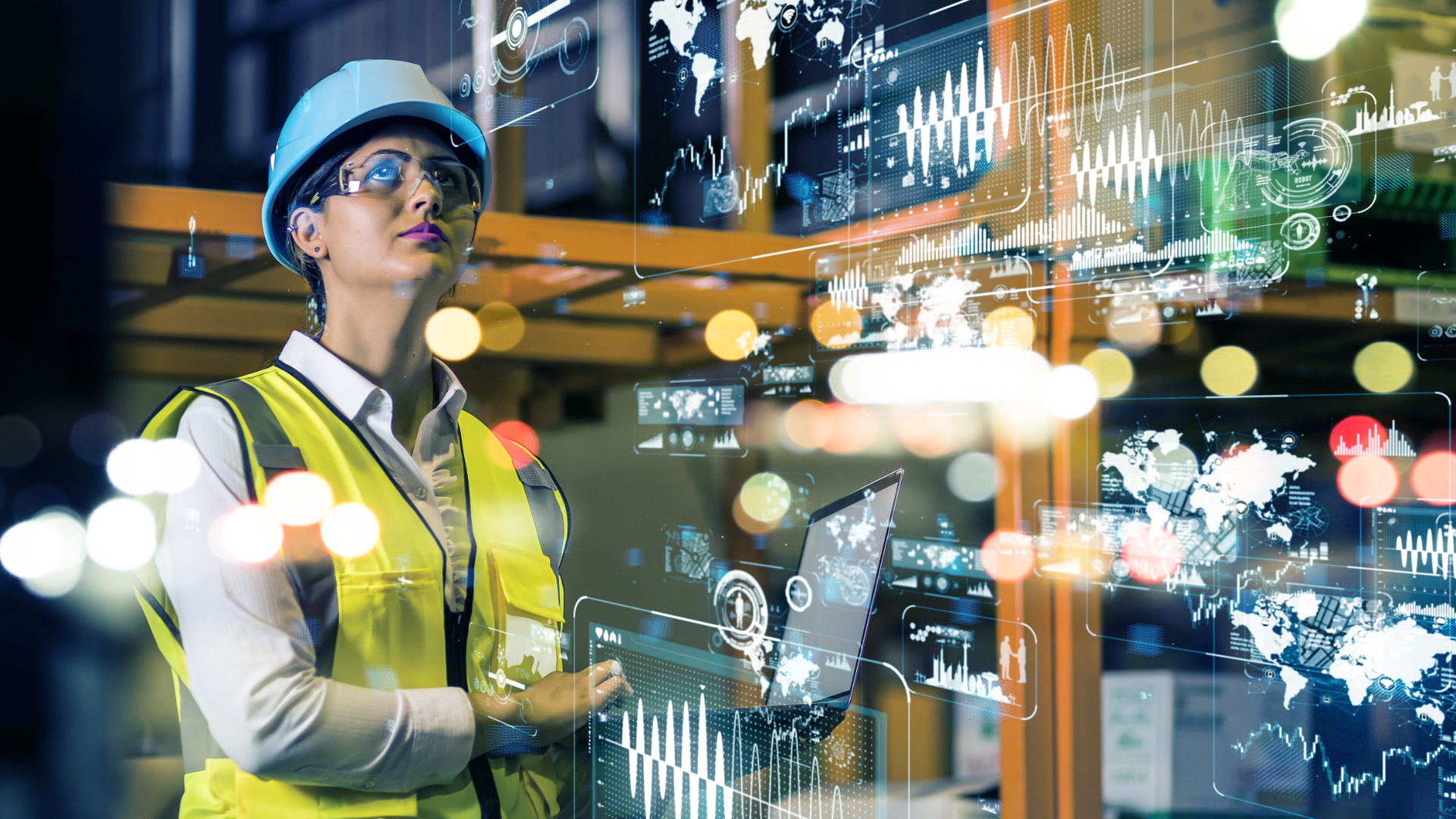
Companies are looking into frontier technologies like AI, ML and IoT technology solutions to re-energize their supply chain efforts. Industry insiders are hoping that ‘digital twins’ might play a part in this balancing act.
‘Digital Twins’ comes from the software world to describe a replica of the real device or system that exists electronically in a virtual space. The goal is to create a ‘twin’ to mirror a real-world working system along with the processes to which they belong.
Fast Company notes more succinctly that digital twins are “the process of using data streams to create a digital representation of a real-world asset to improve collaboration, information access, and decision-making.”
This isn’t futurama stuff, either. By 2025, the market size for digital twins is expected to rise by some 40%, while more than 90% of IoT Platforms will likely utilize some aspects of digital twinning capability by 2026.
Manufacturers in the supply chain can use digital twins as the basis for alignment and local decision-making in the supply chain. In addition, by using data and predictability outcomes in digital twins and cutting the requirement for physical prototyping, teams and organizations will find more flexible testing scenarios, which will help save time and costs.
More than a Concept
Digital twins are more than a concept. Organizations can create a working twin to help teams evolve their products. The virtual product, created with AI and machine learning, helps to inform the physical product. Likewise, digital twin technology works in reverse. It’s a two-way information flow that helps refine products and processes.
For example, digital twin technology can show engineers precisely how a house or office building might hold up over time due to weather, extreme sunlight, natural causes, or more. Then, the engineers can build the structures with sensors to help monitor the buildings. The sensors capture and relay data about the nature of the physical structures. This could include critical data about temperature, wind, energy use, and more.
Once this data has been captured, it can be sent back and processed into the virtual twin. At this point, engineers use the virtual model for various explorative practices. For example, they can study the buildings to see how they withstand environmental pressures. In addition, they can undergo simulations to check for potential improvements. All of these checkups are to gain valuable insights, which can then be transferred into future iterations of the physical twin. All of this helps to feed a two-way flow of data and information.
Digital Twins in Materials Management
Organizations have been dabbling with digital twins in materials management and data points for a while. What’s exciting is that this technology can positively impact the supply chain by simulating large, complex processes, using real-time data and massive computing power.
But to get there, organizations must have clear visibility across their enterprise supply network. A disorganized inventory of material parts has slowed any transition to digital twin technology. In many organizations, the physical pieces are stored in a chaotic fashion. As a result, there may be duplicate materials, and a company may not know which parts have shortages or which materials are being shared across the enterprise.
In some warehouses, the indirect materials may be in storage bins across network store rooms. Therefore, companies need organization before moving ahead to create digital twins.
Organization for indirect materials
Digital twin technology can help with organizing indirect materials. Understanding indirect materials like MRO and putting the pieces together can be a game changer.
The solution exists and doesn’t demand data or system overhauls of business processes. Instead, achieving Material Truth throughout an organization lays the foundation for digital twin technology scalability and functionality.
Improve Operational Ability with AI Technology
More than 90% of global procurement leaders said in a Globality survey they are moving rapidly to transform existing operating processes and models to seek a more competitive advantage. In addition, they are focused on new AI and ML technologies to help gain more value from their data.
These leaders said they are building digital and data teams to integrate these new technologies into their enterprises. With these moves, they expect to learn valuable insights and be better prepared to adjust flexibly to any economic or structural disruptions in their businesses.
It’s time for enterprises to move ahead. An MRO supply ecosystem enables companies to streamline sourcing processes on schedule and via the organization’s guidance. It’s about connecting supplier data to internal networks and between operating facilities. This helps the enterprise move closer to autonomous procurement.
By moving materials data into an MRO intelligence platform and out of spreadsheets and ERP tables, optimizing digital networks, and laying the foundation for digital twin processes, an organization can achieve consistency and management of its materials data.
Have a closer look. Upgrade your enterprise MRO management by investing in the efficiency and accuracy of new MRO technology.
Paul Noble,
Founder & CEO of Verusen