MRO Purchasing: 3 Cost Improvement Strategies You May Be Missing
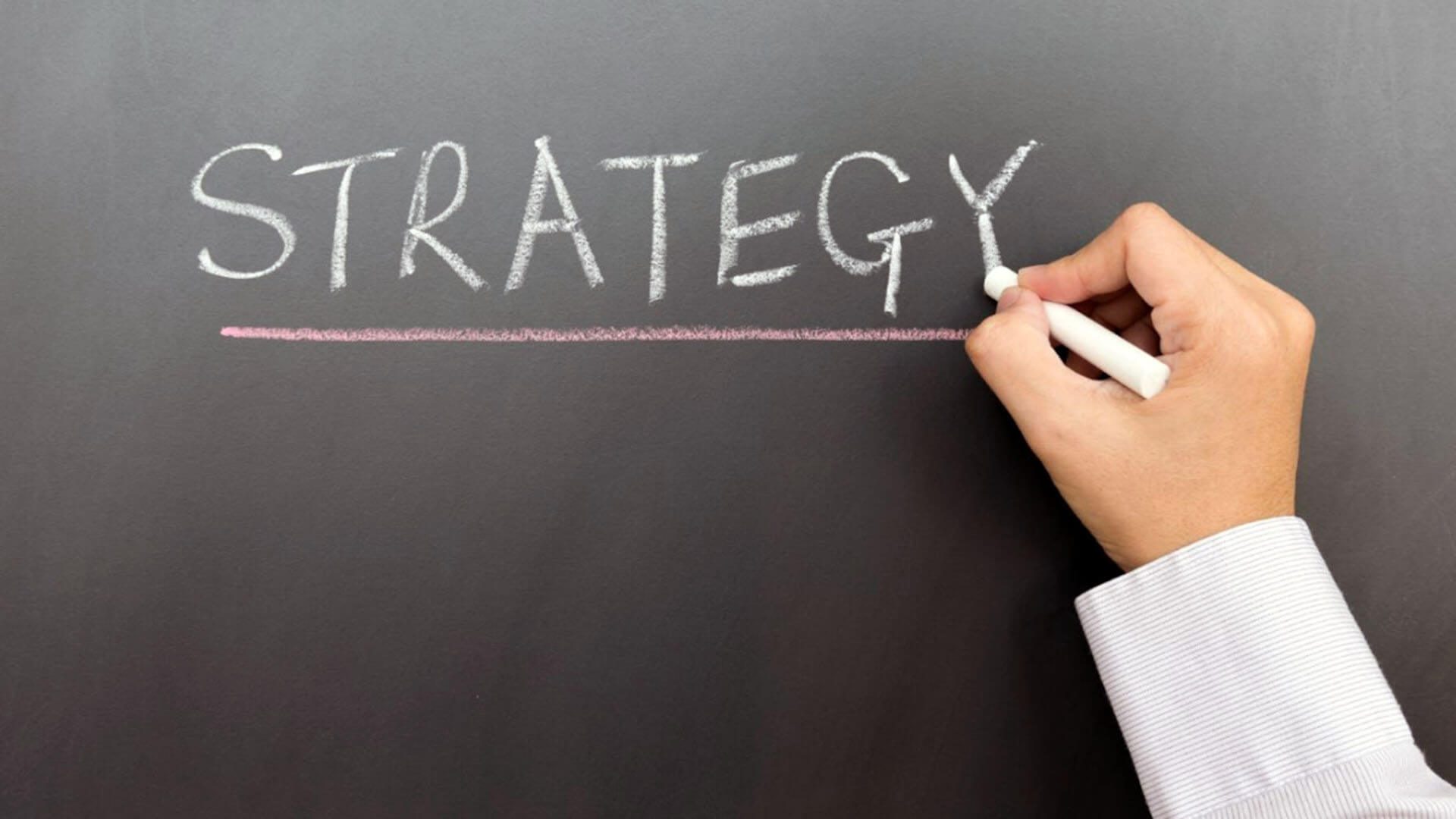
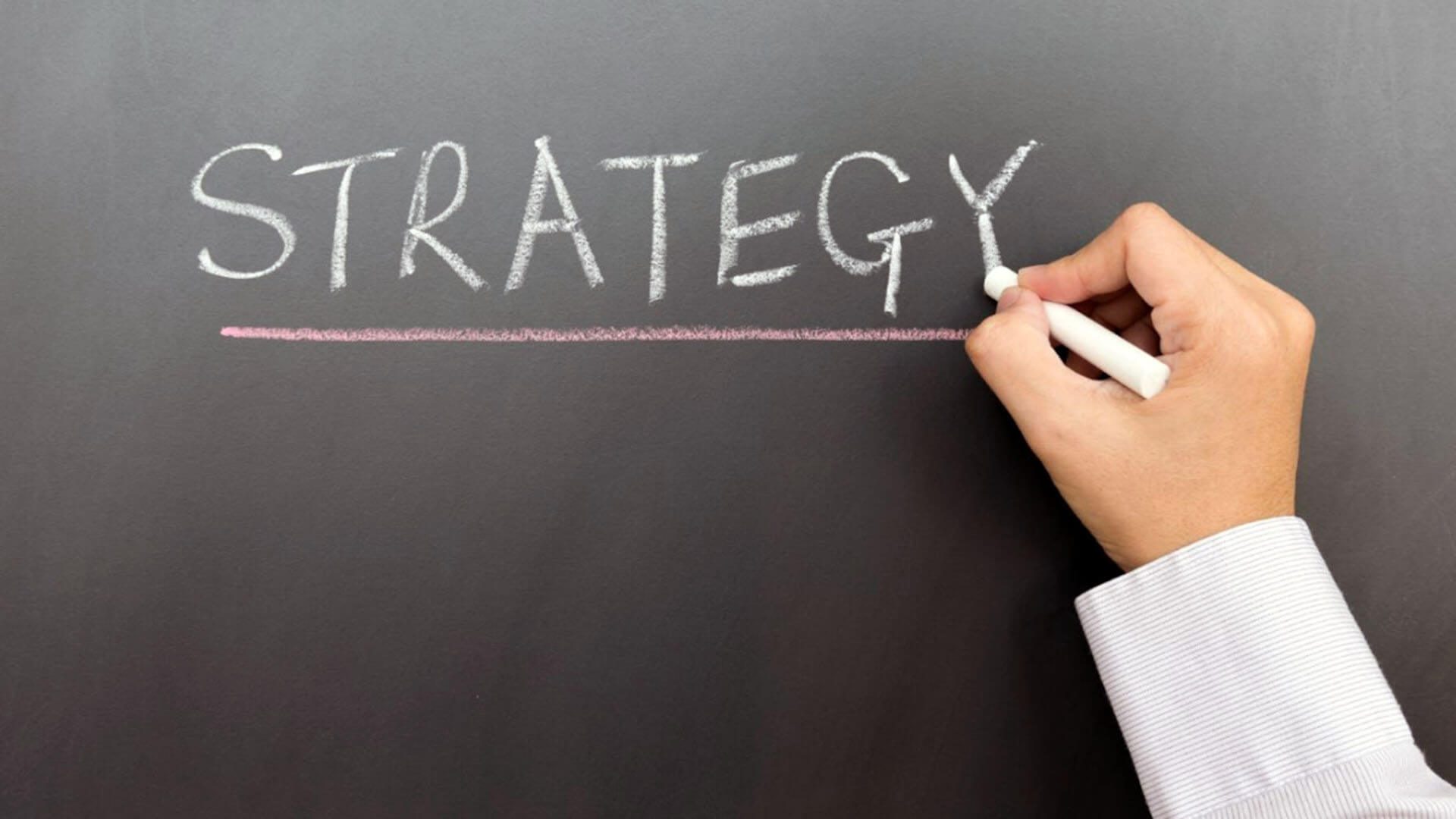
The cost of production typically exceeds the cost of the materials and components directly utilized to produce the product. Why? Due to indirect material expenses associated with production — those that don’t appear in the finished product but do enable its creation.
Examples include consumables like adhesives, lubricants, and essential repairs which are vital to the smooth running of the production lines.
These expenses fall into the category of Maintenance, Repair, and Operations (MRO) and are a key part of indirect spending.
Since these expenses can account for about 15% to 30% of an organization’s total procurement budget, businesses need to implement effective strategies to minimize costs and maximize profit margins.
This guide will explore three cost improvement strategies that you can implement today.
1. Implement a purpose-built solution to track MRO material data
A common problem among many businesses today is that they still rely on disparate and outdated legacy systems.
These systems were not designed to accommodate shared work that spans multiple enterprises and they frequently create data silos that severely affect the visibility of the entire supply network.
A decentralized system results in fragmented data that is isolated across multiple departments, therefore subjecting it to redundancy, inaccuracy, and obsolescence. This makes it challenging for businesses to gauge information about indirect spending and take corrective actions to control it.
Moving all your MRO items to a single, centralized platform can bolster improvement opportunities across a manufacturer’s entire enterprise. Stakeholders will be able to aggregate real-time data that is up-to-data from various facilities in an easily consumable format making it easy to see where the money is being spent, on what parts, and the percentage of the total budget, individual stock levels, among many things.
With improved spending visibility, businesses can optimize indirect spend by cutting or appropriate costs where necessary to fine-tune their budgets.
2. Harness the power of AI to drive MRO optimization
Production downtime can be detrimental to quarter goals if a piece of equipment remains inoperable. While ideal situations are planned for scheduled maintenance, unplanned outages due to hardware failure can set an organization back weeks if the appropriate part isn’t on hand. The financial costs associated with production downtime can be significant and it has the potential of being the biggest contributor to MRO purchasing.
According to The Wall Street Journal, the unplanned downtime cost for industrial manufacturers may be more than $50 billion per year. Therefore, businesses not only need a preventative maintenance strategy to maximize the lifespan of equipment, they need a solution that allows them to easily locate all materials in the event of an unplanned outage.
This is much more effective than reactive maintenance, which involves waiting for disruption to occur before responding to it and simply hoping you have the right materials on hand to manage the issue.
Businesses can leverage Industry 4.0 tools such as artificial intelligence and machine learning to make accurate predictions about potential equipment needs. But manufacturers now have the option to take this a step further with advanced data science to analyze historical data regarding average use of MRO parts, value on hand, safety stock levels, supplier lead times, and overall supplier performance.
As a result, businesses can be proactive and take the necessary measures to optimize MRO inventory levels, eliminate wasted working capital, and reduce procurement efforts. This can help drive down excess MRO purchasing costs substantially.
3. Invest in a materials management solution to improveme procurement
Material management software is equipped with features that make it easy for businesses to track, manage, and control their indirect spend.
Since data across multiple systems is consolidated into a single, centralized platform, businesses can enjoy the luxury of improved decision making. Manufacturers can access real-time, up-to-date, accurate data about MRO purchasing which makes it easy to analyze transaction costs for items, evaluate potential vendors, use Key Performance Indicators (KPIs) to track performance for existing preferred suppliers, and fine-tune the procurement budget while still building value.
The integration a purpose-built solution allows you to incorporate large datasets across multiple departments that can be analyzed to yield valuable insights. Businesses can leverage the power of predictive analysis to find patterns in data, especially when it comes to production operations so that any future occurrences of equipment failures can be detected with a high degree of accuracy. Businesses will have enough time to mitigate these risks well ahead of time.
Don’t delay
If your business’s MRO purchasing is managed effectively, it can not only help you drive costs down but can also be of tremendous value to your organization.
Investing in a cloud-based solution can help you unlock the potential of your MRO supply chain through improved visibility, integration of Industry 4.0 tools, and a centralized system, among many other features.
To learn more about balancing efficiency and responsiveness through material management software, download the ebook on overcoming MRO challenges today.