Bad MRO Procurement Practices That Cost Millions – And How to Fix Them Fast
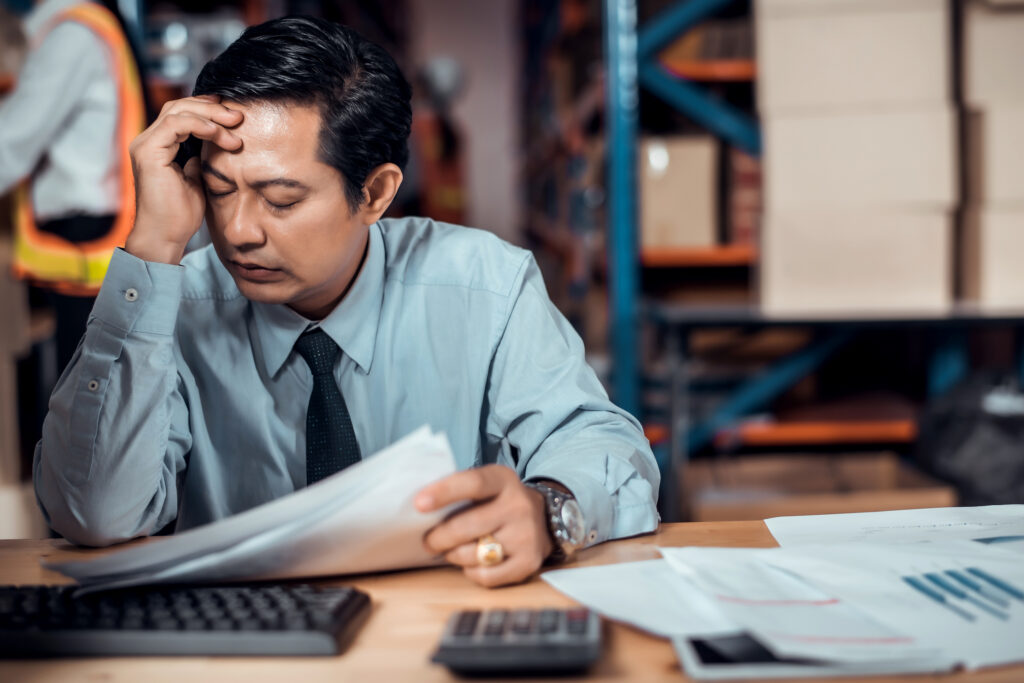
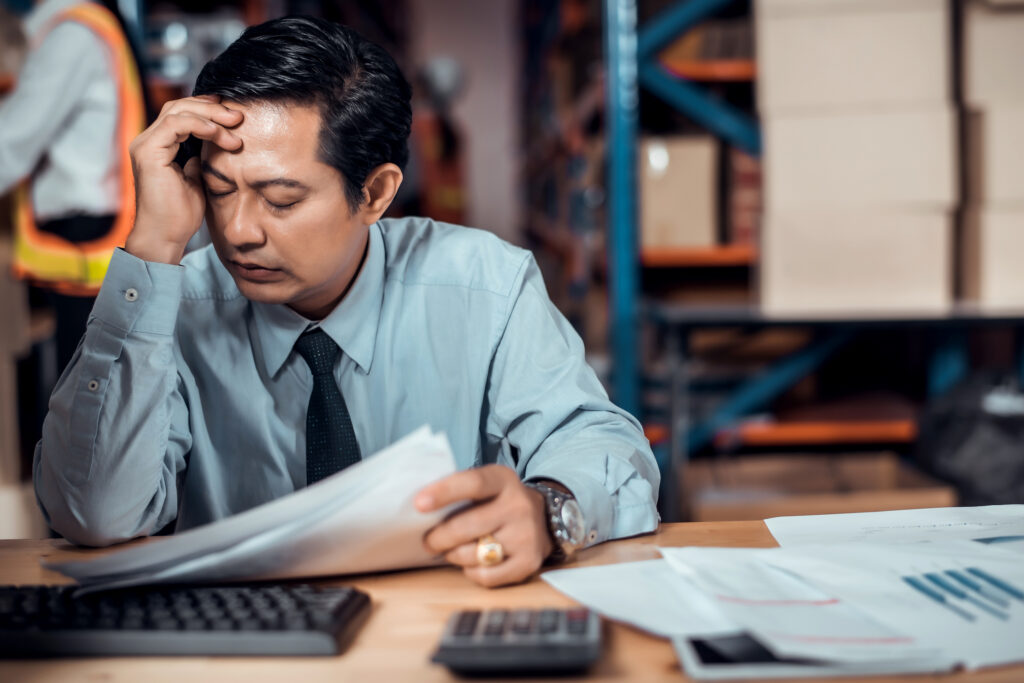
Still treating MRO like a rounding error? That mindset is burning your budget.
In large manufacturing operations, indirect materials are often overlooked. But buried in that 5-10% of spend is a mountain of waste, risk, and untapped capital. Outdated procurement habits – the ones nobody questions because “it’s how we’ve always done it”- are quietly costing Fortune 1000 manufacturers tens of millions.
Here’s what those bad habits look like, how to break them, and how one pulp and paper manufacturer turned theirs into $26 million in verified savings.
1. You’re Not Measuring the Efficiency of Your MRO Procurement Process
If you can’t measure it, you can’t manage it – and you definitely can’t improve it.
Most manufacturers don’t track the efficiency of their MRO procurement workflows because MRO spend seems small on paper. But small percentages at enterprise scale become big liabilities.
Without performance metrics, you’re likely over-ordering, duplicating SKUs, or missing preventive maintenance windows.
Better Way:
- Establish MRO-specific KPIs like inventory turnover, cost per PO, and supplier delivery lead time
- Benchmark performance across plants
- Monitor variance by category to find hidden inefficiencies
This turns MRO from a blind spot into a controllable, optimizable function.
2. Your MRO Data Lives in Silos
Still bouncing between spreadsheets, SAP instances, and tribal knowledge?
One of the most expensive habits in MRO is relying on fragmented, outdated data spread across ERP silos. It kills visibility, slows down sourcing, and leads to costly reorders of materials that already exist somewhere in the network.
Better Way:
- Use AI to harmonize MRO data without a manual cleanse
- Centralize part visibility across plants
- Enable real-time inventory discovery through a single platform
When data becomes visible and trustworthy, you unlock a new level of agility and control.
3. You’re Still Managing MRO Procurement Manually
Emailing POs, chasing approvals, manually checking stock? That’s not procurement-that’s firefighting.
Manual MRO processes are error-prone, slow, and completely unscalable across complex, multi-site operations. And when parts go missing, the cost isn’t just clerical – it’s production downtime, missed shipments, and frustrated customers.
Better Way:
- Automate low-value, high-volume tasks like order requests and part searches
- Leverage predictive analytics to spot demand patterns and reduce stockouts
- Integrate with ERP and EAM systems to streamline approvals and fulfillment
Case Study: Fortune 500 Pulp & Paper Manufacturer
This global manufacturer had $1B in MRO inventory spread across 110 U.S. sites and four different ERP systems. Years of site-level autonomy led to siloed processes, misaligned incentives between procurement and operations, and repeated eight-figure inventory write-offs.
What Changed with Verusen:
- Unified visibility into MRO materials across all business units and ERP systems
- Centralized decision-making from hundreds of stakeholders down to a team of seven
- Replaced fragmented, reactive procurement with network-level optimization
Outcomes:
- $55M in identified inventory reduction opportunities
- $26M in verified savings to date
- 2,900 at-risk materials identified
- 6,600 hours saved by centralizing execution
Verusen didn’t just save them money – it reshaped how they manage MRO procurement across the enterprise.
FAQs: What Execs Ask Before Making the Shift
Can we use Verusen if we run multiple ERP or EAM systems?
Yes. Verusen integrates with SAP, Oracle, Maximo, Infor, and others – even across multiple instances.
Do we need to cleanse our data before using Verusen?
No. Verusen’s AI works with your existing data structure, no upfront cleanse required.
How fast can we see results?
Most customers start seeing measurable results in under 90 days.
Will this disrupt plant operations?
Not at all. Verusen operates in parallel with your existing systems and workflows.
What Happens If You Do Nothing?
You keep overpaying for duplicate parts. You keep writing off obsolete inventory. You keep getting blindsided by stockouts and downtime.
Ready to break bad MRO procurement habits for good?
Book a call with Verusen to see how our AI platform transforms MRO visibility and savings.