Inflation and ongoing disruption are a supply chain’s worst nightmare so far in 2022
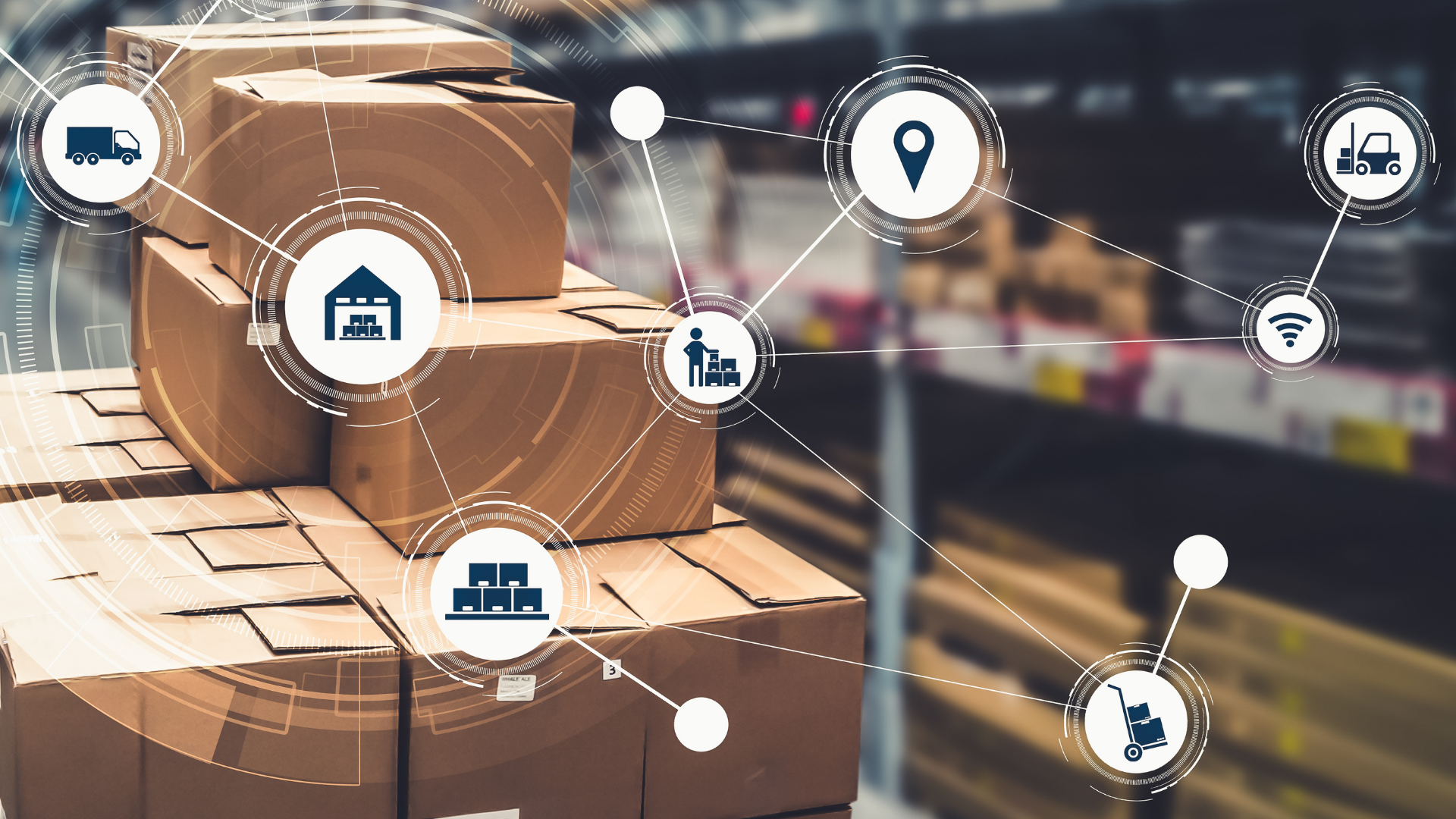
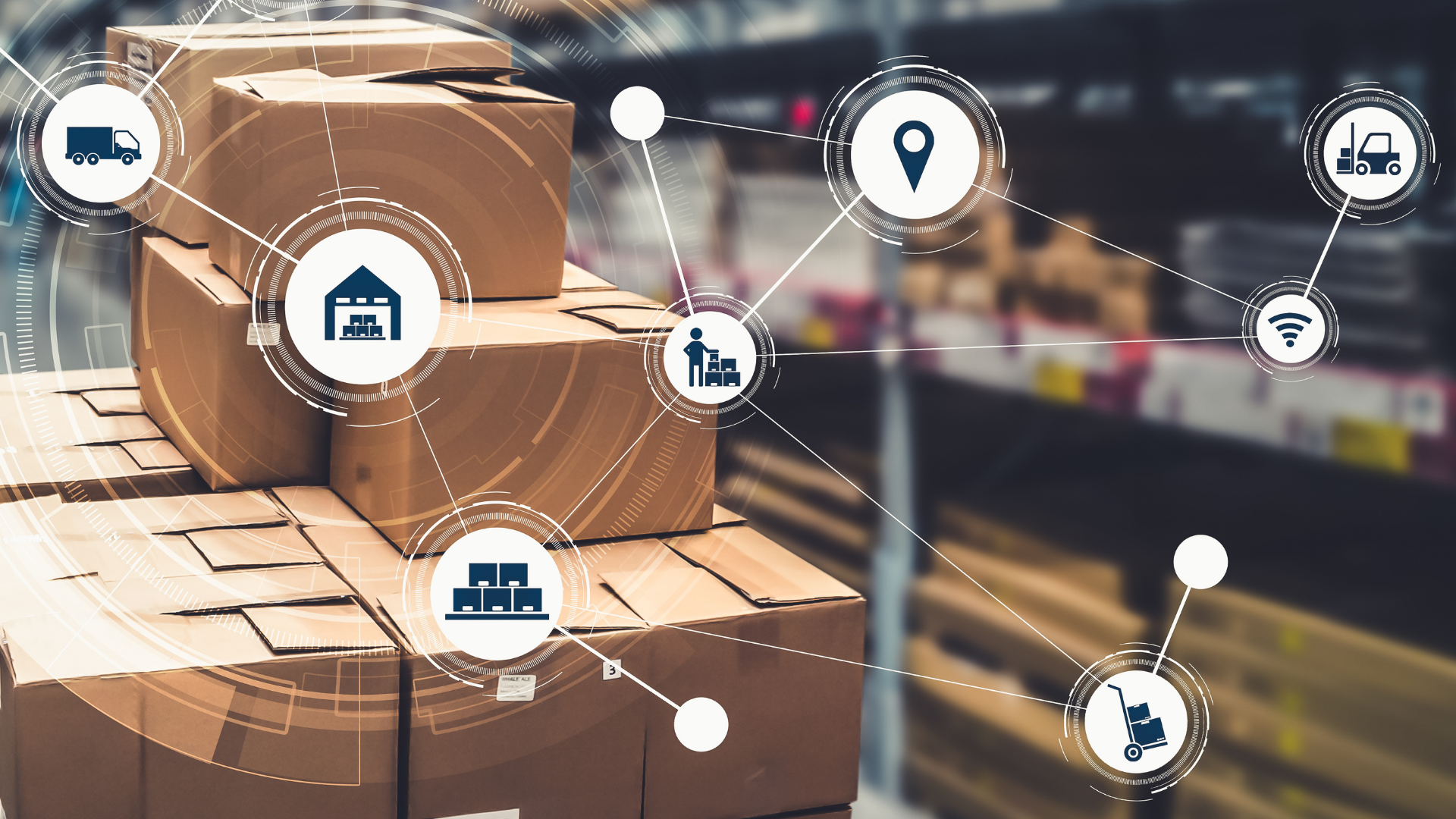
If anything 2022 has brought us so far, it’s more fear, uncertainty and doubt. A year that many believed would return us to some semblance of normality has been anything but as new events and policies bring about yet another headline concerning supply chain shortages and rising costs. While much can still change in the months ahead, the past two years have taught us that we shouldn’t get our hopes up too soon. Let’s take a quick look at the current state of affairs and what that means for businesses and their supply chains moving forward.
Disruption continues to pummel supply chains
Prior to the Covid-19 pandemic, supply chains could sufficiently manage occasional black swan events such as major weather disruptions, a blocked canal, or even a trade conflict. However, no supply management strategy was equipped to handle all of these factors simultaneously throughout a pandemic. Unfortunately the hits just keep coming.
The war raging in Ukraine since late February continues to put pressure on already unstable supply chains. Russia is the second largest oil exporter in the world, and with 30% of the world’s wheat supply coming from Ukraine and Russia alone, availability of these and other critical supplies has dropped significantly. As peace talks continue to break down, any alleviation in sight fades farther into the horizon as sanctions on Russia and humanitarian relief efforts for Ukraine remain a focal point for Western leaders.
Shutdowns to manufacturing sites in Shanghai over the past few weeks due to China’s zero-COVID policy have also hit several major corporations’ forecasts, including Apple and Tesla’s Gigafactory. Even now as restrictions ease and reopenings begin, the flood of products into Shanghai’s ports could create bottlenecks similar to ones experienced in 2020.
Here in North America, a trucking blockade reminiscent of Canada’s Freedom Convoy is now occurring at the US – Mexico border. The Pharr-Reynosa International Bridge, a passage responsible for $440B in annual trade between the US and Mexico, is now being held up by truckers on the Mexico side in protest of Texas Governor Greg Abbott’s “enhanced security initiative.” The increased scrutiny and search requirements for illegal contraband has led to significant delays to the 3000 trucks that cross the bridge each day. As of Friday, the blockade has prevented an estimated $30M in fresh produce from entering the U.S. Additional materials impacted also include critical components for electronics.
Rising prices crushing consumer confidence
The release of March’s Consumer Price Index shows inflation has grown by 8.5% over the past 12 months, with the highest increases occurring amongst energy and housing sectors. Furthermore, spending is starting to wane across all income levels, including high income households, which shows universal concerns around rising prices will most likely contribute to an economic slowdown, at least in the near-term. As consumers look to spend less in the coming months, many may consider cheaper alternatives that still meet their needs. With this in mind, organizations must carefully balance keeping shareholders happy versus simply passing inflationary costs on to consumers. Doing so will require examining other areas within their supply chain and manufacturing operations where costs can be optimized so as to alleviate some of the cost burden while also reducing risk.
Still a long road ahead for supply chains
If we’ve learned anything over the past 2+ years, it’s that the old way of managing supply chains simply doesn’t cut it anymore. The “lean” philosophy of “just in time” (JIT) materials management has made supply chain professionals across the globe realize just how little agility their supply chains possess. Additionally, the once enticing cost reduction of globalization and off-shoring simply doesn’t exist anymore as global wage increases, rising transportation costs, and geopolitical uncertainty is now forcing organizations to reconsider continuing their foreign dependence for manufacturing.
Change is never easy, and adopting new management strategies and the technology solutions that support them is not an overnight process, nor can organizations overhaul entire supply chains all at once. It will take time to determine which areas need immediate attention, which areas allow for quick adjustments and improvements, and which areas need to be rebuilt from the ground up.
In short, reimagining how supply chains need to operate in this new era will take time. Survivors and thrivers will adopt the combination of patience and innovation needed to put new structures and systems that ensure longevity while simultaneously setting up team members for success. One thing for sure is that any organization not taking the initiative to reevaluate their supply chain strategy will surely feel more pain in the coming years due to supply chain disruption and inflation.
To learn more about reducing supply chain risk through MRO optimization, download the white paper on MRO optimization today.