Sourcing Industrial MRO Supplies In the Face of a Recession
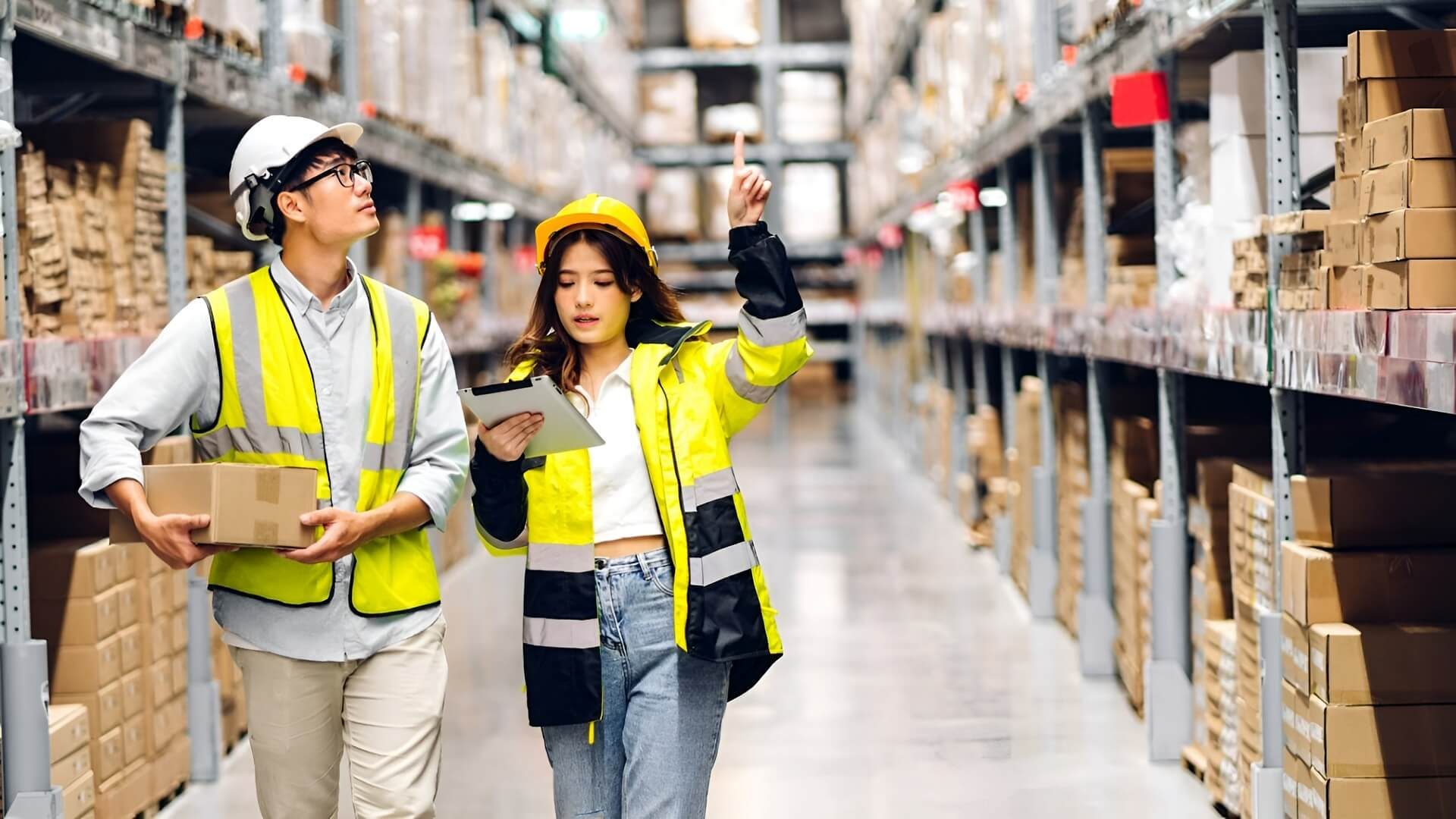
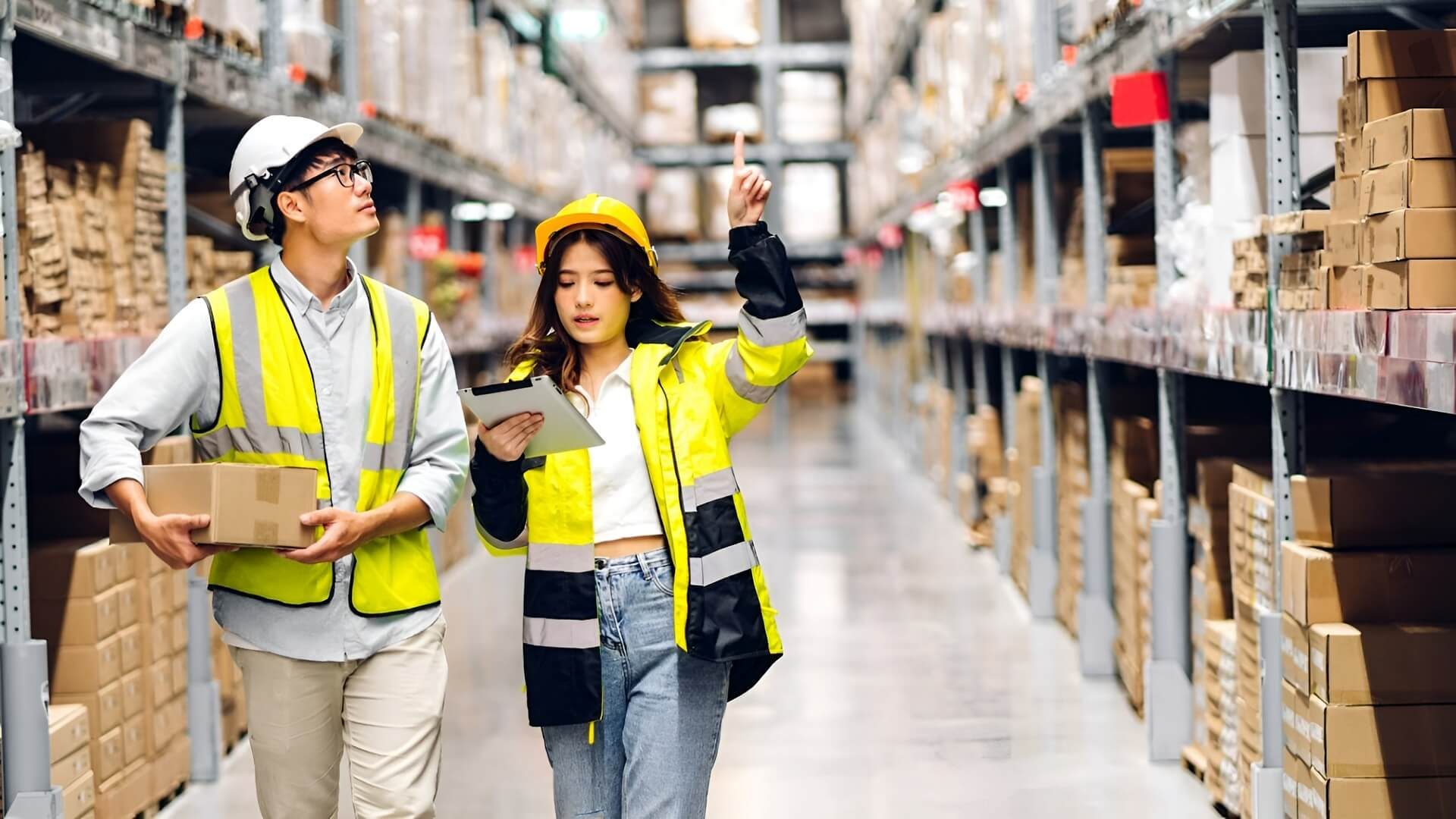
The combination of the Covid-19 pandemic, the Russian-Ukraine war, and the surge in consumer demand has been a perfect recipe for disaster for the global supply chain.
Exacerbating the issue is the record levels of inflation, sparking fears of a global recession, which continues to add strain to an already fragile supply chain, making it difficult to source industrial MRO supplies during a time of crisis.
Fortunately, there is still hope on the horizon with sourcing in supply chains—if you take the right steps, that is. In this guide, let’s take a look at effective strategies for sourcing supplies that you can implement to navigate through an uncertain, inflationary supply chain environment.
Making your purchasing strategy resilient
Update your framework
The economic recession has exposed additional vulnerabilities of the global supply chain and has revealed how fragile balance sheets are in the face of disruptive events. Instead of stagnating with traditional organizational frameworks, MRO leaders should use this as a cue to push long overdue structural change into their system.
An excellent place to start is to improve visibility in your supply chain network so that you have a holistic view of your MRO supplies. This way, you can easily pinpoint and resolve inefficiencies well ahead of time before they snowball into something bigger.
For instance, many MRO organizations make the mistake of not having firm purchasing processes. This leads to rogue spending which leads high volumes of unneeded materials that eat at profitability. Instead of allowing departments to make fragmented decisions about supply levels and vendors, establish a system that depends on trusted vendors and suppliers with negotiated contracts and reliable shipping patterns.
It’s also important to set forth policies that require employees to receive real-time procurement insights so that operations can appropriately aggregate spending within the organization.
Keep your supply chain resilient
Throughout the Covid-19 pandemic, many major cities in China—the world’s biggest manufacturing superpower—have been locked down to prevent the spread of the virus as China continues to enforce its “zero Covid” policy.. These revolving disruptions send supply shocks across the supply chain because companies can’t guarantee the ability to source their MRO supplies from their usual vendors anymore.
For many, this has been reason enough to diversify their vendors in an effort to make their procurement strategies more resilient.
Diversification allows operations to lean on different vendors in times of crisis or delay. This way, even if your usual vendor is unable to fulfill your needs, you can immediately switch to your alternative supplier(s) for materials. Your production processes will continue to run with little to no downtime.
Since suppliers play an integral role in the success of your business, it’s vital that you assess how reliable they are. You can use performance-based scorecards that clearly outline the results you expect and utilize Key Performance Indicators (KPIs) to evaluate vendor performance and mitigate risk.
Some KPIs all procurement teams should work into their contract include:
- Quality of MRO supplies
- Average lead time
- Shipment and delivery windows
- Inventory availability
- Monitoring the financial status of vendors
Create air-tight processes now
Another way to unlock value in your MRO ecosystem is to optimize existing inventory levels and procurement processes before you’re hit with a recession. This leaves you better prepared to insulate yourself from the coming calamity. Operations teams and MRO managers should invest in a solution that sits on top of your existing tech stack so that you can prioritize continued improvements for your materials management strategy.
Studies show that interruptions to production operations ranked number one on the list of global risks to supply chains. If essential components aren’t readily available or can’t be sourced from alternative vendors, this can create significant roadblocks for production and logistics. It can lead to increased costs, cancellation of orders, and process delays which can eventually result in reduced market earnings, market share, and damaged reputations.
MRO leaders need to ensure their digital transformation incorporates a solution that can create cost-effective materials management processes. Systematically optimizing MRO materials can help identify areas that need more safety stock so that they can be available in the right place should downtime occur.
Furthermore, having a system that facilitates the timely exchange of information between key stakeholders not only improves communication but also allows teams to proactively implement corrective actions at the initial stage of the problem.
Invest in resiliency
Use the right tools to support a “right-sized” system
Old, legacy systems are simply not equipped with the features needed to make your supply chain resilient. Investing in the right material management software can help you uncover opportunities that otherwise couldn’t be done by using traditional approaches.
For starters, your operations should be able to promote consistent data collection practices across your entire supply ecosystem. The data that is collected should be harmonized into a single spot that can be viewed with just a tap of your fingers. Since you’ve employed healthy data collection methodologies, your MRO data will be accurate, up-to-date, and reliable.
Using this data, you can open your organization up to actionable insight rather than vulnerabilities. For instance, you’ll have a comprehensive breakdown of where money is flowing out of your operation so that you can cut back on maverick spending and rogue purchases. It allows you to make informed business decisions such as educating employees about malpractice and establishing policies to curb the issue.
Take on a proactive approach
As important as it is to make your supply chain resilient, it’s equally important to make an agile supply chain as well. The global market is evolving rapidly and if businesses don’t keep up they’ll soon become obsolete in the long run.
An AI-based solution helps leaders make informed decisions with tools that offer actionable insight from the get-go.
For instance, you can leverage powerful machine-learning algorithms to analyze historical data regarding inventory levels, duplicate materials, critical shortages, and usage statistics from previous downtime events. The smart system will incorporate data points regarding your historical purchasing habits
Using this information, the software returns actionable insight regarding when to exercise spend avoidance, materials that can be shared across facilities, how many new parts need to be ordered, and where disposition opportunities lie..
This not only helps managers increase the lifespan of assets, but you can also minimize bottlenecks in your supply chain, such as shipping delays and unplanned production downtime events.
Prepare for what lies ahead
The road ahead is uncertain as the threat of recession looms large over the manufacturing industry. Now more than ever, companies should take some time to evaluate their current materials management strategies and put forth new, effective strategies to sustain their business in times of high uncertainty.
A cloud-based purpose-built solution for materials management can help you build long-term resilience by providing the flexibility to navigate through disruptions and the resilience to rebound from their impacts.
Learn more about how to mitigate your organization’s expensive data problem today.