MRO Spend Analysis: How Fortune 500 Manufacturers Cut Millions Without Risking Uptime
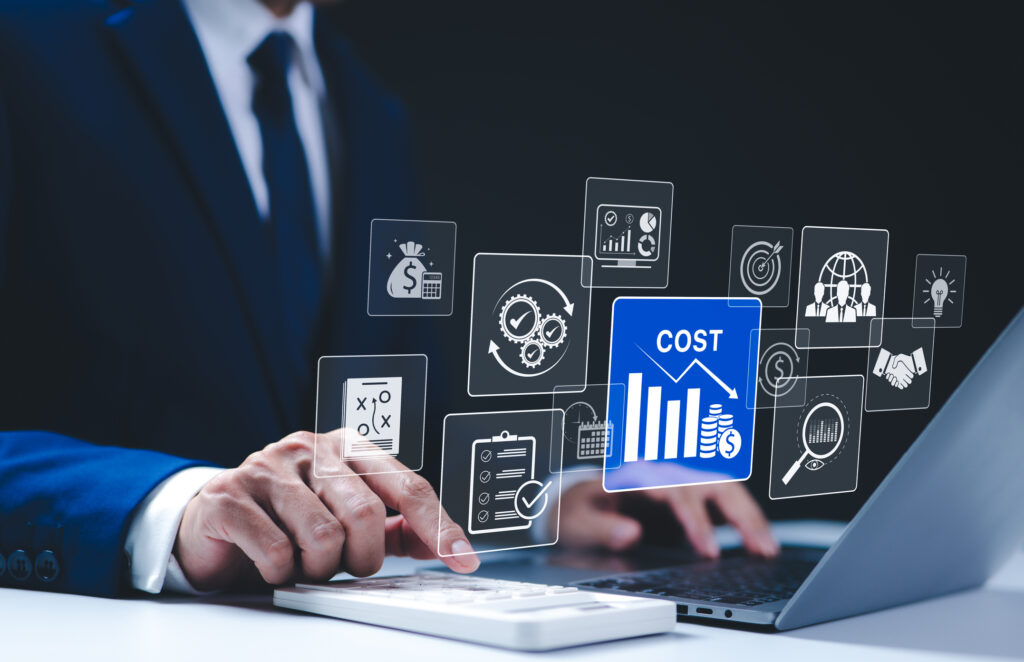
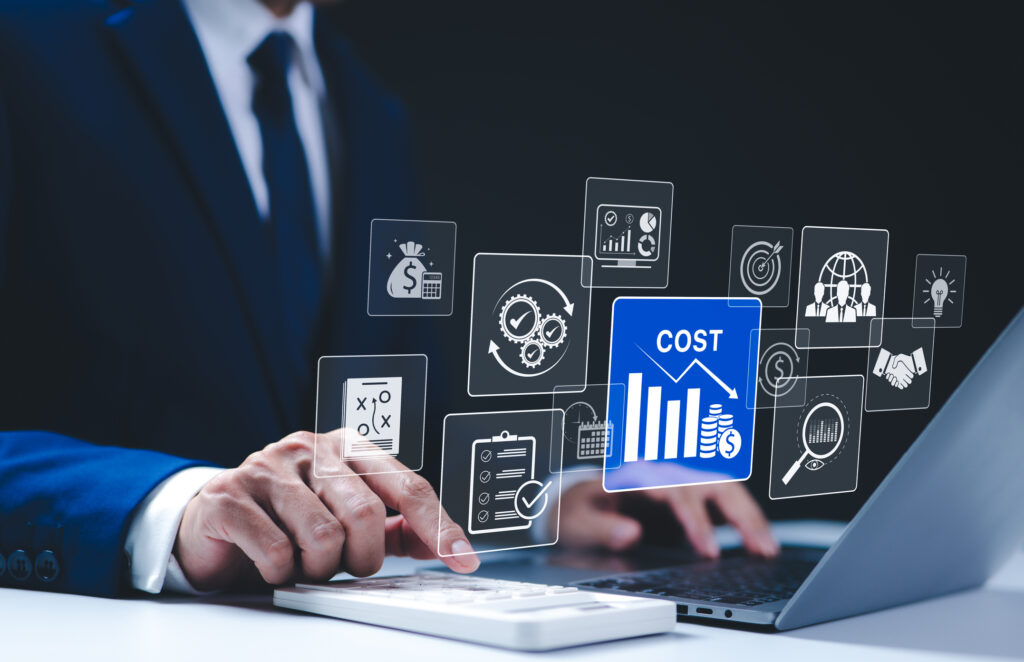
When MRO Spend Turns Into a Silent Profit Drain
Two identical bearings. Two different SKUs. One costs your business $50,000 in wasted working capital.
This is the reality for many Fortune 1000, asset-intensive manufacturers. Even in stable market conditions, a single unplanned plant shutdown can cost millions in lost production and expedited shipping. And yet, MRO spend management – the inventory of spare parts, consumables, and maintenance materials needed to keep operations running – is often overlooked as a strategic lever for cost savings and risk reduction.
If your organization runs SAP, Oracle, Maximo, or Infor/Hexagon ERP/EAM systems across multiple sites, chances are you’re sitting on hidden savings opportunities. Without visibility across plants, your team could be over-purchasing materials that already exist elsewhere, holding excess stock for years, or missing chances to consolidate suppliers.
See how your MRO spend stacks up – book a supply chain optimization call.
Five Common MRO Spend Challenges That Erode Profitability
1. Disconnected Data Across Multiple ERP/EAM Systems
For global manufacturers, it’s common to run multiple ERP or EAM instances due to mergers, acquisitions, or regional independence. But when plant A’s system can’t “see” plant B’s inventory, the result is duplicate purchases, inconsistent part naming, and a lack of enterprise-wide insight.
Without consolidated visibility, you’re unable to identify slow-moving stock, transfer critical spares between sites, or adjust stocking policies to actual demand. This directly impacts both MRO spend reduction opportunities and uptime reliability.
2. Excess Stock – or Dangerous Shortages
Too much inventory means millions tied up in carrying costs. Too little means production risks, emergency buys, and expedited freight fees. Most companies lack accurate, network-wide insight into how much MRO material they truly have on hand.
Consider this: If your organization holds $100M in MRO stock across 15 plants, and the annual carrying cost (storage, insurance, obsolescence, and capital cost) averages a conservative 20% – that’s $20 million per year just to hold that inventory. Even a modest 10% reduction in excess stock through network optimization frees $10 million in working capital annually without increasing downtime risk.
Balancing inventory requires not just plant-level awareness but a network-wide optimization strategy. The right AI-driven MRO spend analysis tools can reveal overstock positions and reallocate underused parts to where they’re needed most – without a costly, months-long data cleansing project.
3. Hidden Duplicate Materials
Duplicate SKUs silently inflate your MRO spend by increasing procurement volume and fragmenting supplier contracts. Over time, this not only wastes working capital but also hides opportunities for volume discounts and sourcing efficiency.
AI-enabled inventory management platforms can identify and reconcile these duplicates – even when part descriptions differ due to supplier changes or inconsistent naming conventions. The result? Clearer supplier performance metrics and a more predictable MRO spend baseline.
4. Inconsistent Supplier Performance Tracking
Without standardized, enterprise-wide metrics, supplier evaluation becomes subjective. Poor performance might go unnoticed until a critical outage exposes the risk.
A centralized MRO platform allows you to monitor on-time delivery, quality, and fill rates across all vendors. This visibility helps sourcing teams shift spend to more reliable suppliers – reducing downtime risk and strengthening supply chain resilience.
5. Manual, Spreadsheet-Based Processes
Manual MRO management consumes your team’s expertise without capturing it for strategic use. Spreadsheets get outdated fast, and tribal knowledge remains locked in individuals’ heads.
By contrast, AI-based decision support systems combine machine learning with human insights, automating data analysis while preserving institutional knowledge. This allows your experts to focus on strategic improvements rather than data wrangling.
Case Study: Fortune 500 Packaging Manufacturer Saves Millions & Avoids Weeks of Downtime
Facing excess working capital from duplicate inventory, siloed decision-making, and fragmented ERP systems, a Fortune 500 packaging manufacturer turned to Verusen’s AI-driven MRO spend analysis platform.
- $59 million in savings opportunities identified, with $14 million verified savings to date – without increasing operational risk.
- >$1 million saved by preventing downtime: When a critical part failed, Verusen’s AI Global Material Search located an identical spare at a sister plant. The asset was operational again in 3 days instead of 4+ weeks, avoiding millions in lost production.
Downtime impact example: For this manufacturer, each hour of unplanned downtime costs approximately $40,000 in lost production, labor disruption, and delayed orders. Avoiding an additional 25 days of downtime (600 hours) prevented roughly $24 million in potential losses.
- 672 at-risk materials identified for proactive management.
- Material review time dropped from 20+ minutes to 4 minutes on average.
- All MRO inventory data harmonized into a single platform, enabling cross-site visibility and faster decision-making.
“The Verusen solution found the critical assets we needed to get our assets up and running in 3 days instead of 4+ weeks, saving us millions.” – Reliability Manager, North America
FAQs
Do we need to run a data cleanse before starting?
No – Verusen’s AI cleans, classifies, and unifies your MRO data in-platform. No separate data project is required.
Will this work with multiple ERP/EAM systems?
Yes – Verusen overlays your existing systems (SAP, Oracle, Maximo, Infor/Hexagon, and others) and integrates updates regularly.
How soon will we see verified savings?
Most enterprises identify measurable savings opportunities within 30-45 days, with verified savings following shortly after implementation.