Fostering MRO Inventory Optimization Through Cross-Departmental Communication
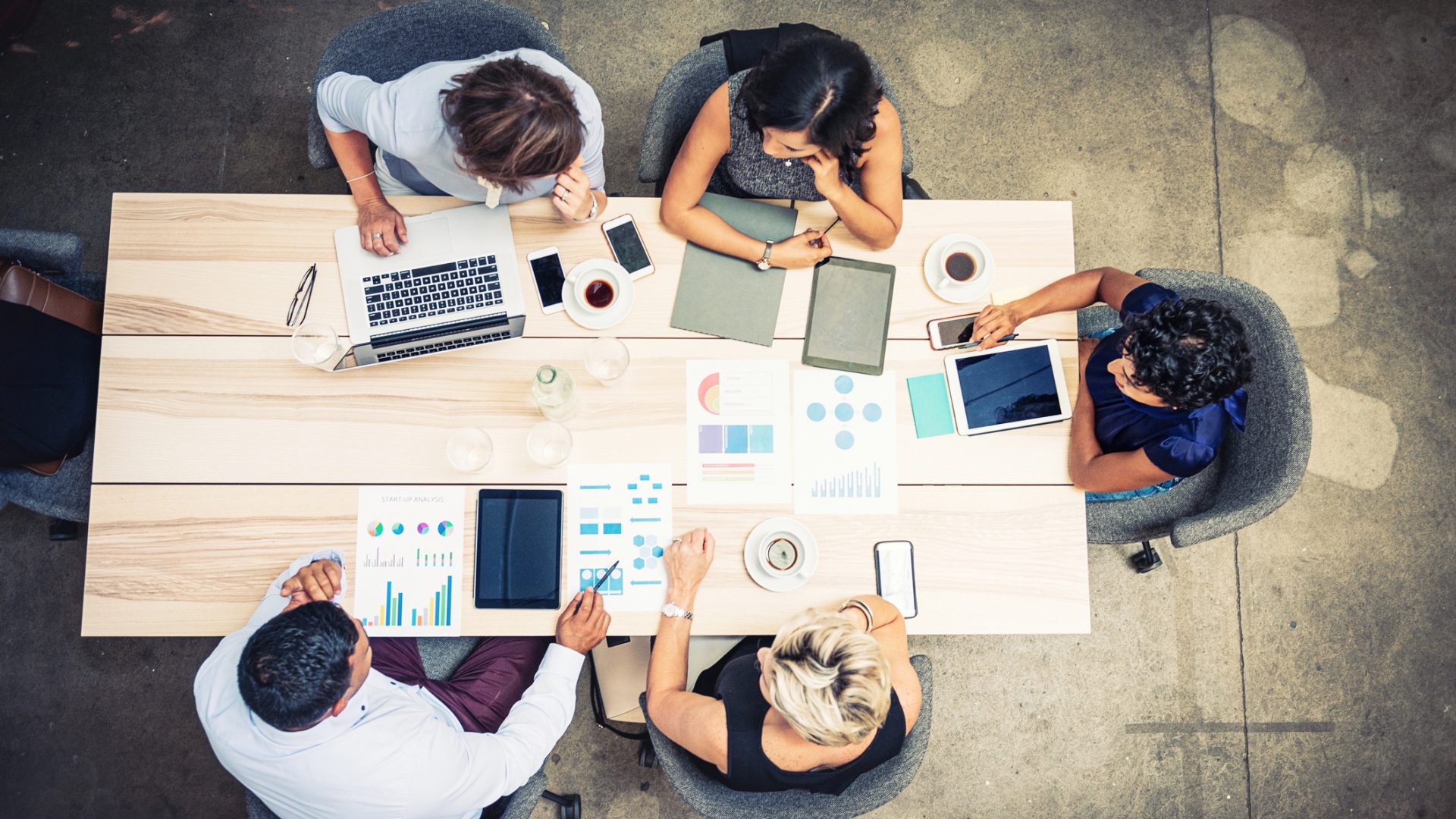
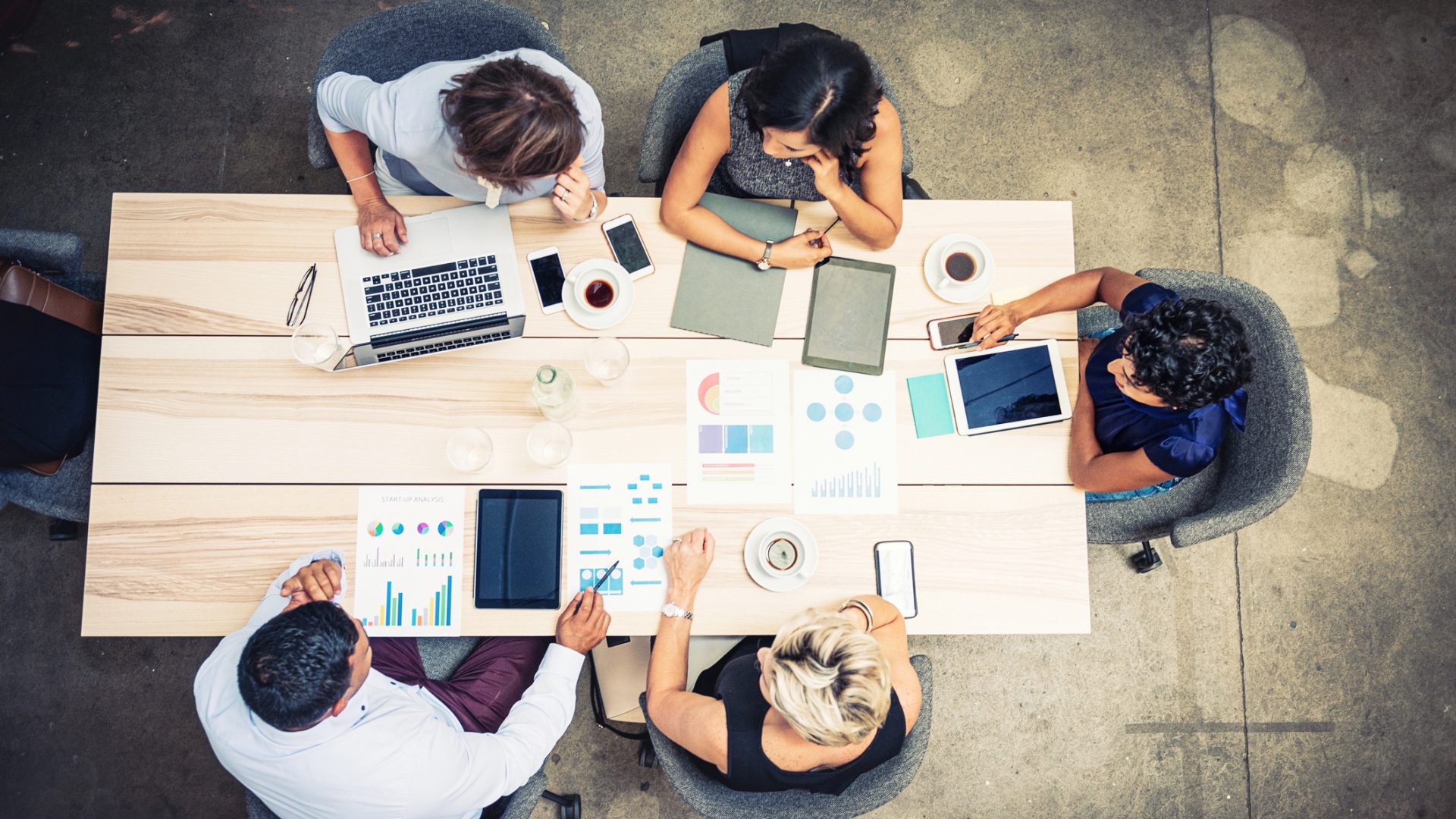
Fostering MRO (Maintenance, Repair, and Operations) inventory optimization hinges on seamless cross-departmental communication and the inherent trust in MRO inventory data. Unfortunately, misaligned incentives between MRO inventory procurement teams and maintenance and operations teams often lead to inefficiencies that can be costly for any organization. This blog explores the challenges posed by these misalignments and offers solutions to foster better communication and improve MRO inventory data for improved MRO optimization.
Misaligned Incentives and Their Consequences
MRO inventory procurement teams and maintenance and operations teams often have conflicting priorities. For example, maintenance and operations teams prioritize having insurance spares readily available to minimize downtime and quickly address unplanned maintenance needs. On the other hand, procurement teams are incentivized to control costs, limit suppliers, and eliminate wasteful spending. This misalignment can lead to significant operational issues, including unplanned downtime—a problem that affects everyone, regardless of their role.
Unplanned downtime is not the only issue; the duplicates, overstocking, and obsolescence of parts that must be replaced or written off also results in considerable waste. These obsolete parts represent a sunk cost that could have been avoided with better communication and coordination between departments.
The Problem of Siloed Communication
A significant barrier to fostering MRO inventory optimization is the lack of cross-departmental communication. Silos exist across teams, technology systems, and even plants and facilities. Consequently, this fragmentation means neither MRO procurement teams nor maintenance and operations teams have a reliable grasp of their MRO inventory data, which often resides in disconnected technology systems. Each plant may operate under a different model for both maintenance and MRO inventory purchasing, further exacerbating the disjointedness.
Without robust cross-departmental communication, it becomes nearly impossible to trust the data or the insights derived from it. This lack of trust undermines efforts to optimize MRO inventory and leads to inefficiencies like rogue purchasing or mislabeled criticality ratings that could be easily avoided.
The Need for Collaborative Technology Tools
The inability to share needs and information via technology is another critical issue. But many organizations lack collaborative tools that allow internal teams to effectively communicate inventory needs and issues in real time. Manual processes dominate, making it difficult to share up-to-date information and coordinate with external suppliers.
The absence of real-time communication tools not only hampers internal coordination but also complicates interactions with external suppliers. This can lead to delays, miscommunications, and ultimately, a less responsive MRO supply chain.
Shared KPIs for Better Alignment
To overcome these challenges, it’s essential to establish shared KPIs around MRO inventory management and optimization. Aligning procurement and operations teams on common goals is crucial for achieving MRO optimization. Both sides of the organization must recognize that they are two sides of the same coin and work towards a common objective.
By embracing the strengths of each department and acknowledging their own weaknesses, procurement and operations teams can find common ground. Working together, they can develop strategies that minimize downtime, reduce waste, and ensure the availability of critical spare parts.
Moving Forward for MRO Inventory Optimization
To truly overcome these challenges and drive significant improvements, it is essential to adopt a purpose-built AI-powered MRO inventory optimization platform. Such a platform can analyze vast amounts of data in real-time, providing actionable insights and recommendations for optimal inventory levels. This advanced technology enables proactive maintenance strategies, reduces downtime, and ensures the availability of critical spare parts.
An AI-powered solution also enhances cross-departmental communication by providing a unified view of MRO data, facilitating better decision-making, and fostering collaboration between procurement and maintenance teams. By leveraging the strengths of artificial intelligence, organizations can turn a traditionally challenging area into a well-oiled machine, driving both short-term improvements and long-term strategic success.
Incorporating a purpose-built AI-powered MRO inventory optimization platform ensures that MRO inventory optimization efforts are successful, leading to reduced downtime, cost savings, and improved operational efficiency. By prioritizing cross-departmental communication, MRO data sharing, and leveraging AI technology, organizations can achieve a new level of efficiency and reliability in their MRO operations.