Assessing Your Current Tech Stack’s Impact on MRO Inventory Procurement
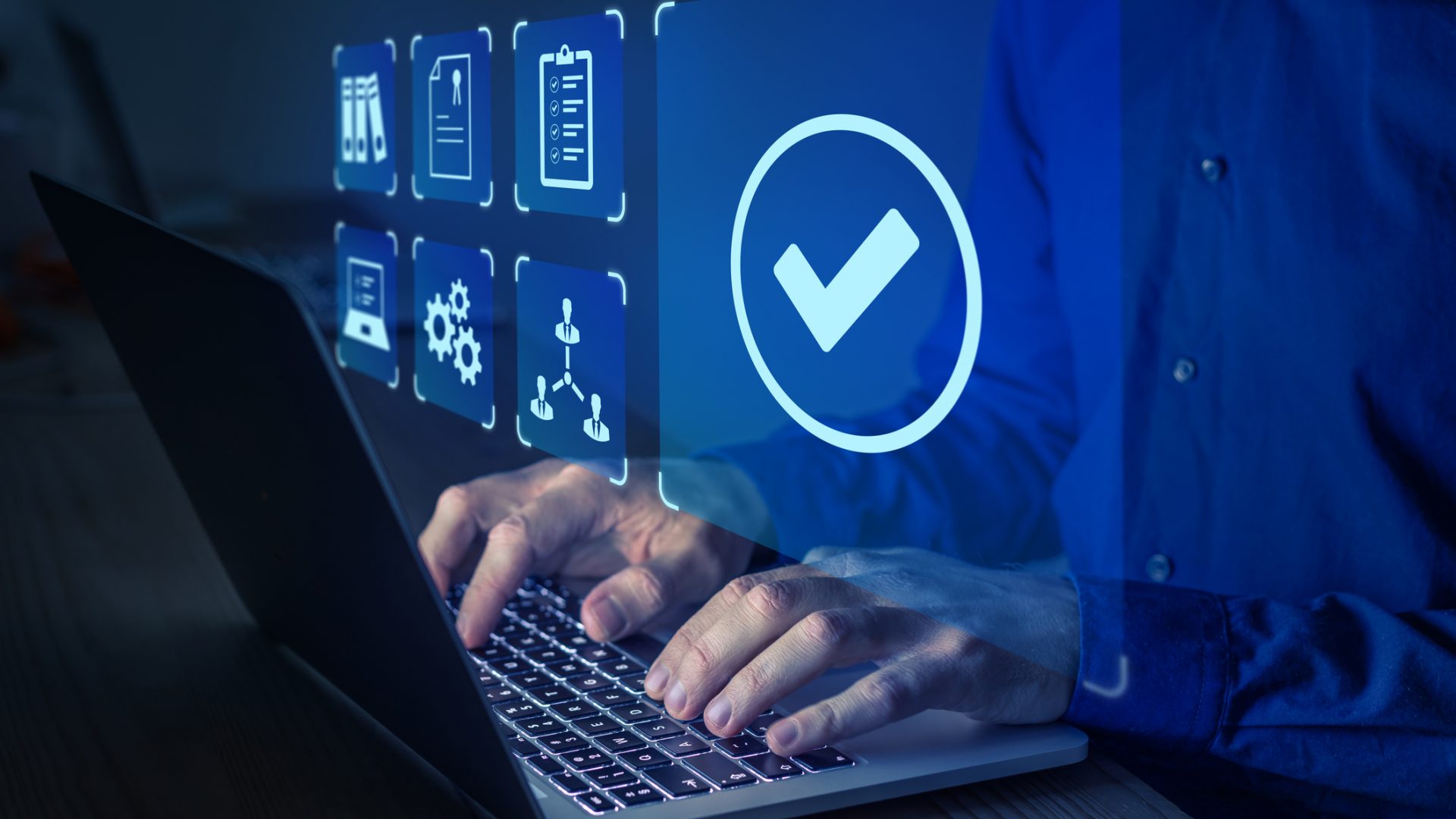
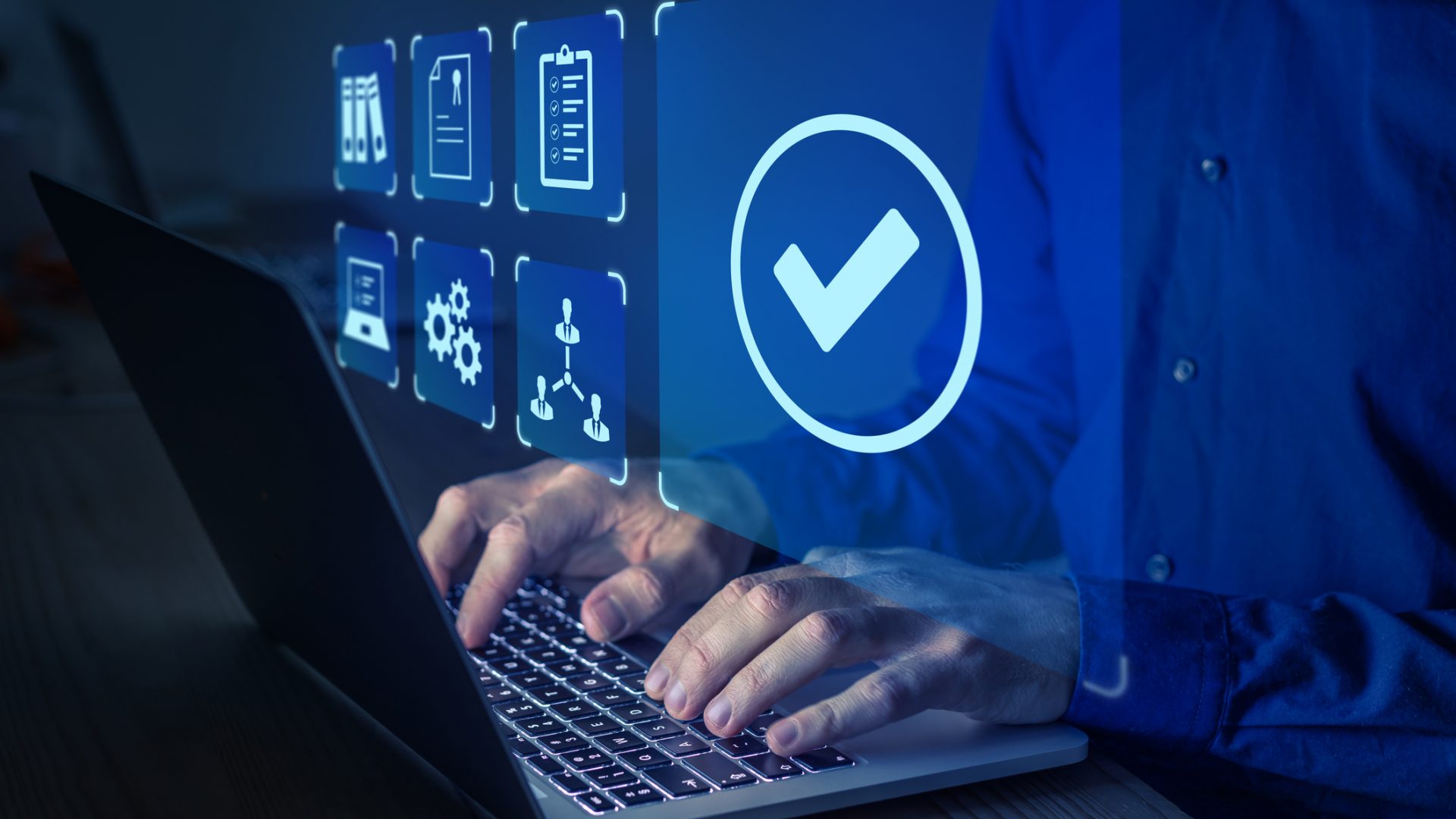
In the complex world of MRO inventory procurement, especially in asset intensive industries like manufacturing, energy production, and oil and gas that are heavily reliant on Maintenance, Repair, and Operations (MRO) inventory, the effectiveness of your tech stack can make or break your MRO procurement and inventory management efficiency.
Let’s delve into the critical importance of assessing your current tech stack’s impact on MRO inventory management and how it can revolutionize your procurement strategies for smarter purchasing, inventory management, cost reduction, and risk management.
Do You Have Expensive Systems yet Still Rely on Manual Processes
Many MRO procurement professionals find themselves trapped in a paradox: investing in expensive, state-of-the-art software systems only to continue relying on manual processes like pivot table analysis, email, and data cleansing projects. Despite the promise of automation and streamlining, manual data entry, fragmented workflows, and siloed information persist.
The result? Inefficiency, wasted resources, and missed opportunities for optimization. In fact, many organizations find themselves dealing with millions of dollars in excess inventory or SLOB materials. Relying on manual processes to find these insights proves next to impossible, meaning companies have to regularly navigate costly write-offs.
Do Your Systems Give You Confidence in Your MRO Data?
Confidence in your data is paramount for effective MRO procurement and inventory management. Can you trust the availability, location, lead times, and cost optimization insights provided by your current tech stack? Without this confidence, procurement decisions become risky guesswork, leading to stockouts, overstocking, and increased operational risk.
These challenges become compounded when your organization is maintaining:
- Multiple systems of record – it’s common for companies to have many instances of ERP or EAM systems. This leads to siloed business units or departments who have no trust in the data regarding inventory availability, lead times, and purchasing needs.
- A constantly expanding supplier base – many organizations rely on dozens if not hundreds of suppliers for MRO inventory, which often results in challenges around consistent naming of parts, tail spend, poor category management, and more.
- Mergers and acquisitions – as companies grow and expand through M&A activity, they inherit all the spare parts data, purchasing processes, and suppliers that come with the new division being absorbed. This only adds to the MRO data challenges most organizations are already dealing with.
It’s time to assess whether your tech stack provides the actionable insights your MRO data possesses to make informed decisions for upcoming MRO purchases.
Does Your System Capture Context to Previous Decision-Making?
Understanding the context behind previous inventory management decisions is key to avoiding costly mistakes and identifying opportunities for improvement around duplicate materials, SLOB inventory, lead times, and maintenance challenges. Yet, without access to historical data and insights, procurement professionals risk repeating past errors.
Evaluate whether your tech stack empowers you to lean on your reliability engineers, maintenance teams, and operations managers to provide you with the institutional knowledge to update your existing data. As older workers retire from the workforce and already growing talent gaps continue, being armed with the contextual information needed to refine your procurement strategies and drive continuous improvement will be key to creating additional waste or risk in your company.
Does Your System Efficiently Align Procurement with Operational Needs?
Efficient alignment between procurement processes and operational needs is essential for successful MRO management. But it requires the ability to trust MRO data. However, traditional systems like ERP, EAM, and P2P solutions have very constricting data dependencies that make it difficult to pull real insights.
As a result, organizations lack the agility and flexibility to adapt to dynamic operational requirements. Assess whether your tech stack enables seamless integration between procurement and operations, including the ability to collaborate on demand signals, inventory replenishment, part sharing, and supplier management.
Does Your System Let You Share Parts with Ease?
MRO Inventory sharing presents a cost-effective strategy for optimizing MRO inventory levels and reducing procurement costs. Especially if you have duplicate materials and high levels of overmax. However, many procurement professionals struggle to facilitate seamless inventory sharing due to visibility limitations in their tech stack. Evaluate whether your current system supports inventory sharing initiatives, including recommendations for sharing parts, network creation amongst BUs, and optimizing hub and spoke opportunities.
Research Purpose-Built MRO Solutions
Ultimately, assessing your current tech stack’s impact on MRO procurement and inventory management is the first critical for maximizing efficiency, minimizing downtime, and reducing potentially millions of dollars worth of excess inventory. Having a purpose-built solution that specifically addresses MRO challenges such as manual processes, data dependencies, and alignment with operational needs, procurement professionals can unlock the full potential of their MRO management efforts and drive organizational success.
To see what opportunities AI-powered MRO inventory optimization may present your organization, check out the MRO Cost Savings Calculator.