What Are the Biggest Aerospace Supply Chain Issues Facing Us In 2023?
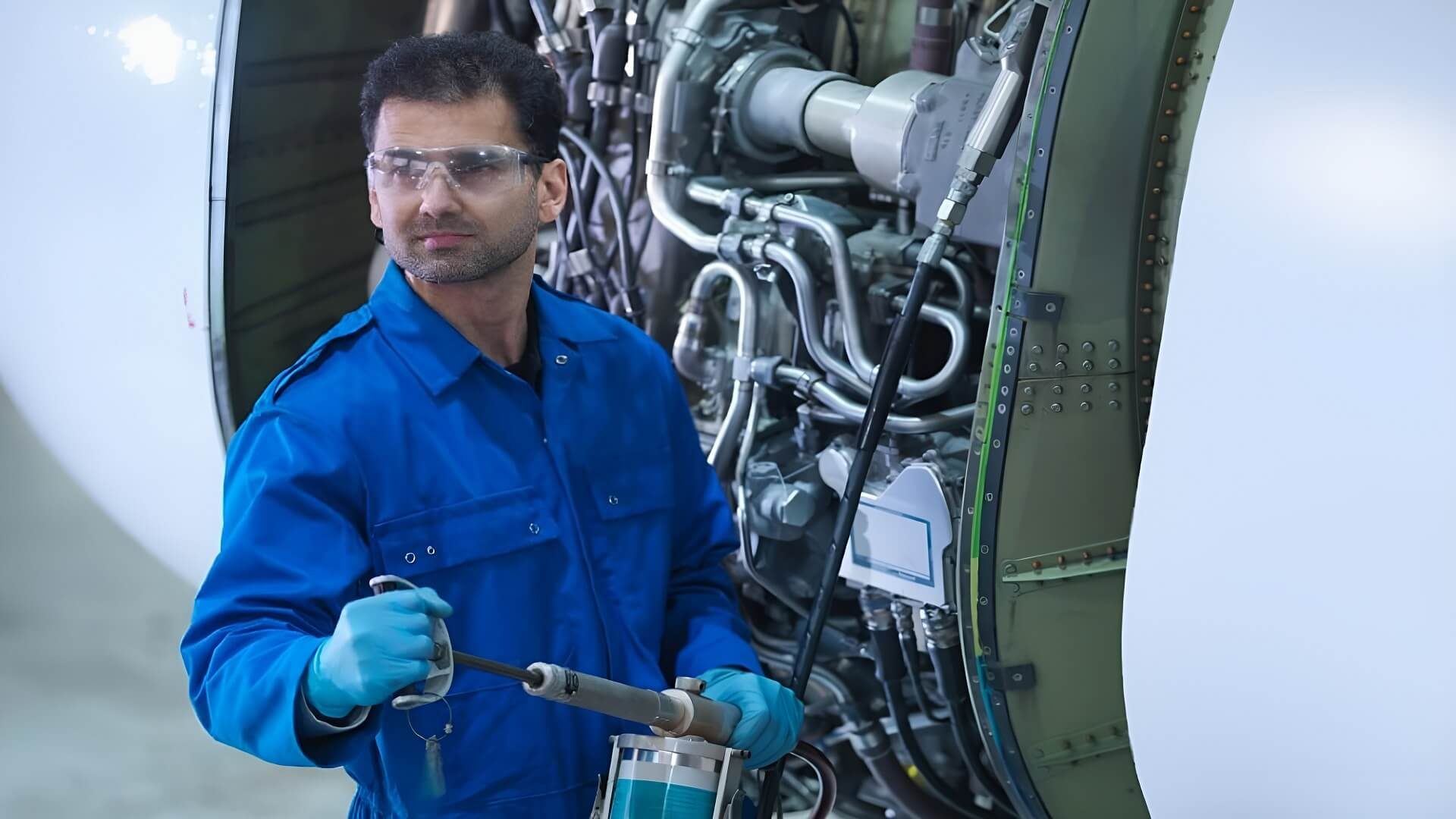
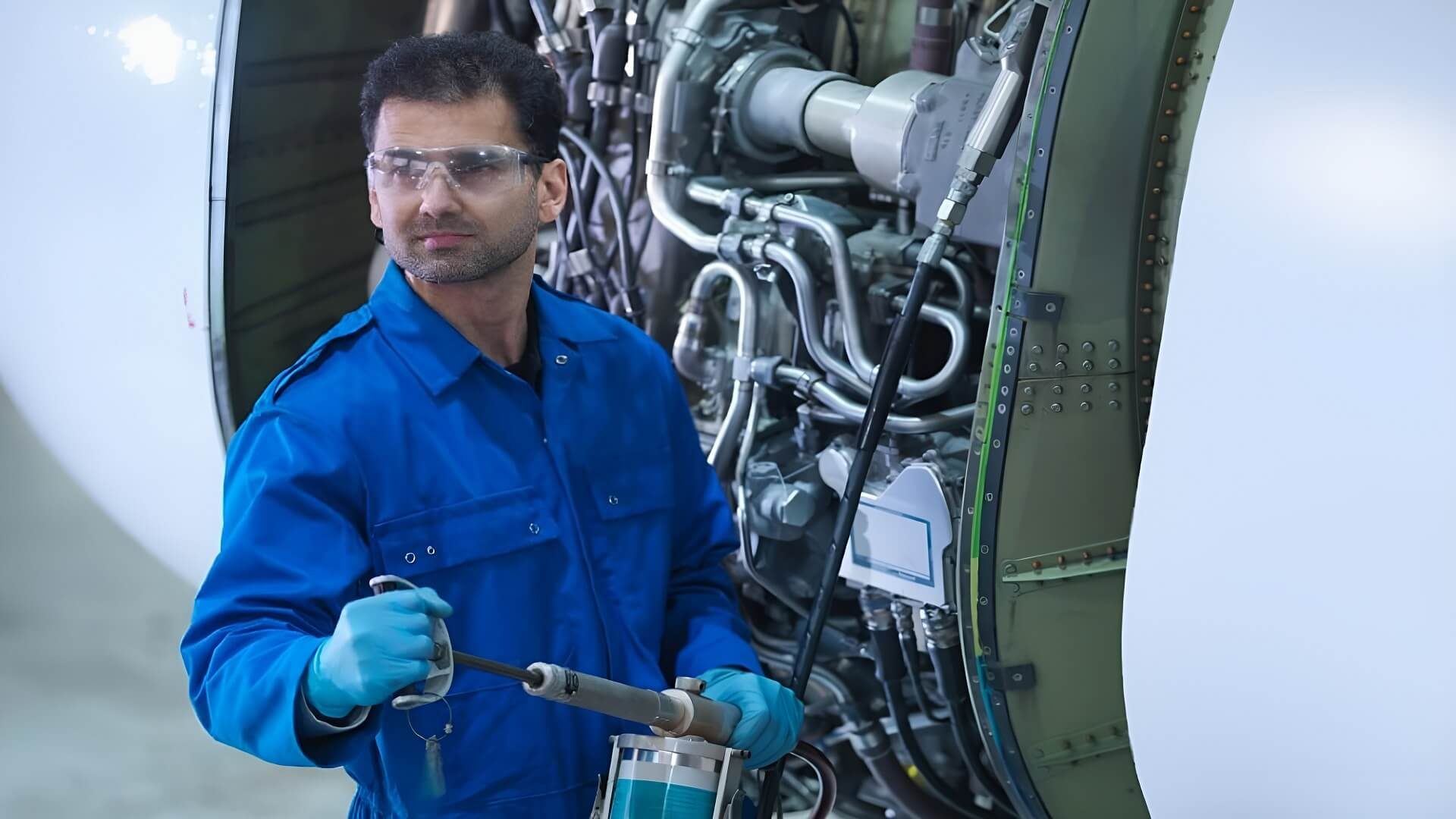
The lingering impact of the Covid-19 pandemic ripples across the aerospace industry even today. Although production has ramped up again, aviation operations are still struggling to rebound from the issues plaguing their supply chains, making it difficult to find their footing in a post-pandemic world.
In this article, we’ll take a look at the biggest supply chain issues that aerospace MRO leaders have to watch out for in 2023 and the solutions available to mitigate them.
Returning to pre-pandemic demand with post-pandemic bottlenecks
Meeting increasing demand
Although the travel demand has reached normalcy, the same can’t be said about the supply available. This disparity in high demand and low supply puts a strain on an already fragile supply chain. This issue is further exacerbated by a severe labor shortage, a result of a growing interest in more flexible working conditions with higher pay.
The aviation industry has specifically identified the scarcity of engine castings and wiring connectors to be the biggest contributors to the bottlenecks in their supply chain.
Manufacturers are struggling to cope with these hiccups and are seeing increased delays, with supply back-ups of up to two months, and lowered profit margins.
Misallocated resources
A common mistake that MRO leaders make is failing to anticipate the needs of the future, leading to the misallocation of valuable resources. These mistakes are not only costly in terms of capital, but also in terms of the time it takes to recover from these losses.
A great example is when 138 737-MAX planes that were supposed to leave for China ended up remaining on the tarmacs in Washington. This is because China still has strict Covid-19 travel restrictions and exercises extreme caution when it comes to international travel.
If Boeing were able to foresee this, they would’ve prioritized customers who needed their planes more urgently instead of spending their inventory on this prospect.
Not only are manufacturers left sitting on products that won’t be accepted, but the capital tied to them could’ve been reinvested elsewhere in the business with the potential for a higher ROI.
Inflation and energy costs
Inflation is wreaking havoc in the aerospace supply chain landscape and long-established ways of business prove to be obsolete in a high-cost business environment.
Inflation has affected operation costs significantly, putting managers in the challenging position of needing to negotiate costs or tighten up procurement processes.
Largely, these price hikes have been seen in price tags on raw materials, energy, labor, and transportation. It’s forced the industry to get lean in purchasing and ordering, and also to get creative with keeping production time to a minimum in an effort to save on energy expenses.
The challenge of it all is keeping productions running smoothly with minimal unwanted downtime, all while being as efficient as possible in resource expenditure and use.
How you can stay ahead of these supply chain issues
Move resources where they need to go
The best thing leaders in the industry can do is prepare for the unexpected by keeping a close eye on what they can control in anticipation of the unexpected.
Small operational hiccups and inefficiencies can snowball from one part of the operation into another, leading to unforeseen downtime and lost resources.
The right material management software should help managers increase operational visibility and lend them a holistic view of their operation in a single, intuitive platform. This can help identify any vulnerabilities or potential roadblocks in the system well ahead of time so that corrective actions can be implemented before those issues amplify into something bigger.
Keep production streamlined
A growing customer base can put a lot of pressure on production, especially if manufacturing timeframes and resource availability aren’t commensurate with the demand surge. It makes optimization necessary rather than exceptional.
Failure to optimize supply chain processes can lead to increased energy consumption, more frequent unplanned production downtime, and inefficiency all of which leads to one thing: increased costs.
Leveraging digital tools can not only streamline production but can also yield increased productivity. For instance, artificial intelligence and machine learning can crunch historical data regarding past downtime events at unimaginable speeds to predict future occurrences of mechanical failure or the need for part replacement. This way, you can schedule maintenance at times that make disruptions minimal and are energy efficient.
Smart analytics offer actionable insights on stock replacement and procurement strategies so that operations can stay ahead of the curve when it comes to delays and downtime.
Stay resilient through this year’s challenges
The road ahead in the aerospace supply chain landscape is an uncertain one and it can be challenging to navigate through it. It’s high time to say goodbye to old processes and embrace digital tools that optimize operations.
A cloud-based solution should allow operations to see results in a matter of weeks.
Improved visibility, predictive analysis capabilities, and actionable recommendations are just a few of the features that a good material management solution can offer. Equip yourself with the right tools so that you can face the challenges of 2023 head-on.
Learn more about how to mitigate your organization’s expensive data problem today.