7 Best Practices for Managing Critical Spare Parts in MRO
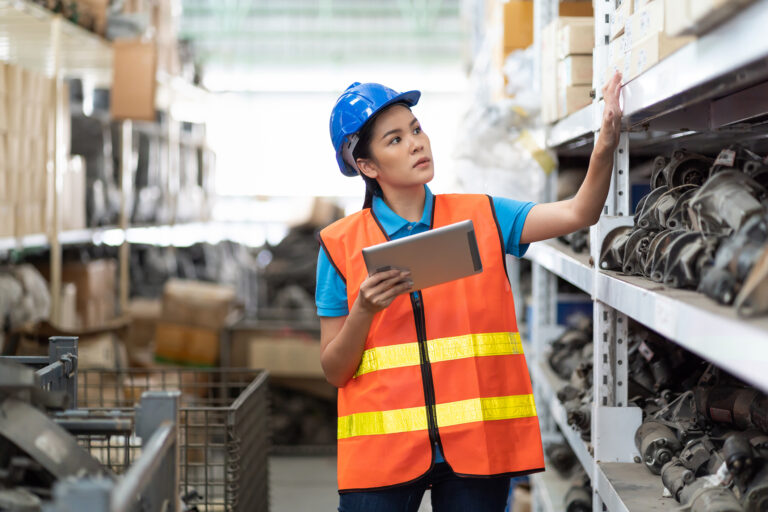
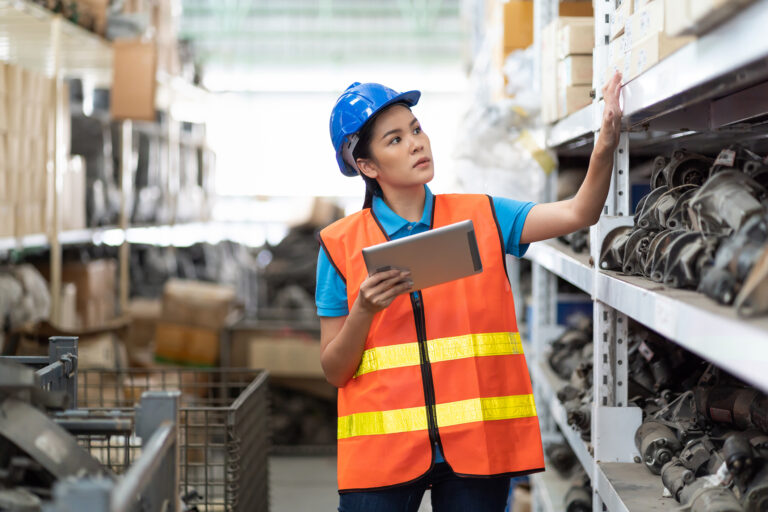
7 Best Practices for Managing Critical Spare Parts in MRO
Managing critical spare parts effectively is essential for ensuring the seamless operation of Maintenance, Repair, and Operations (MRO) inventory. However, the challenges surrounding critical spare parts management can often lead to inefficiencies and increased costs. In this blog, we’ll explore best practices for managing critical spare parts, highlighting common pitfalls and offering innovative solutions, particularly through the integration of AI technologies.
Understanding the Challenge of Critical Spare Parts Management
MRO inventory management has always posed a significant challenge, particularly when it comes to predicting and managing stocking levels for critical spare parts. Many businesses have relied on supply chain software solutions originally designed for finished goods or raw materials, only to find these tools inadequate for MRO inventory. Several key issues contribute to this ineffectiveness:
1. Lack of Understanding of Material Criticality
Critical spare parts often include high-cost insurance spares that tend to move slowly or remain inactive. Traditional procurement algorithms may recommend reducing stock levels for these items, a decision that can be detrimental. The lack of nuanced understanding of what constitutes a critical spare part often results in misguided recommendations that fail to align with operational needs.
2. Ineffective Data Handling
Legacy software systems typically depend on relational databases and BI reports. This reliance forces users to conduct their analyses outside the system, often in Excel, complicating the decision-making process. As a result, organizations miss out on real-time insights that could significantly improve their critical spare parts management.
3. Complexity and Implementation Challenges
Over the past three decades, various MRO optimization tools have emerged. Initially useful, these systems have become overly complex, requiring significant time and expertise to implement. Current implementations often take six to twelve months and necessitate ongoing adjustments as organizational needs change, creating a scenario where knowledge gets lost with employee turnover and system configurations become outdated.
Examples of Challenges:
- Oil & Gas Producer Offshore
This company initially focused on uptime but later needed to prioritize cost reductions. However, their software’s conservative recommendations no longer aligned with their evolving priorities, leading to abandonment of the tool.
- Open Pit Mining Organization
Faced with fluctuating commodity prices, the client found their optimization solution ineffective due to outdated recommendations. Instead of updating configurations, they chose not to renew their contract.
- Utility Company
This organization aimed to save $200M in MRO costs but struggled with the complexities of their system during the COVID-19 pandemic. As a result, the solution failed to provide value, leading to its discontinuation.
Best Practices for Managing Critical Spare Parts
1. Establish a Clear Definition of Criticality
Defining what constitutes a critical spare part is foundational. Establish criteria based on the part’s role in operations, replacement cost, lead times, and the impact of downtime. A clear understanding of criticality ensures that procurement strategies align with operational priorities.
2. Utilize AI and Advanced Analytics
The advent of AI, particularly through Large Language Models (LLMs), has revolutionized critical spare parts management. Unlike traditional systems that rely on rigid configurations, AI-driven solutions can analyze vast amounts of data to identify duplicates, recommend optimal stocking levels, and dynamically adjust to changing conditions.
Benefits of AI in Critical Spare Parts Management:
- Identifying Price Variance
AI can detect discrepancies in prices for the same parts across different locations, helping organizations optimize procurement strategies.
- Network Optimization
AI can recommend opportunities for sharing parts across locations, reducing excess inventory and associated carrying costs.
- Enhancing Repair Strategies
By assessing the condition and suitability of parts for repair, AI can streamline maintenance processes, contributing to cost savings.
3. Implement a Risk-Based Approach
A risk-based approach to critical spare parts management allows organizations to prioritize stocking levels based on potential impacts on operations. This method not only optimizes inventory levels but also enhances collaboration between procurement and operations teams, ensuring everyone is aligned on material criticality.
4. Continuous Data Evaluation
Leverage an “always-on” data evaluation approach to ensure that criticality assignments are kept up-to-date. By continuously assessing and updating material criticality, organizations can avoid reliance on outdated information that may lead to stockouts or excess inventory.
5. Engage Users in the Process
Involve frontline users in the training and ongoing adjustments of AI systems. Users often possess valuable insights about parts that are not reflected in existing data. By implementing user-in-the-loop technology, organizations can quickly adapt to new information and adjust criticality ratings and stocking recommendations in real time.
6. Train and Retain Knowledge
Ensure that training programs are in place to educate new users about the systems and processes related to critical spare parts management. Retaining knowledge through documentation and ongoing training helps mitigate the risks associated with employee turnover.
7. Regularly Review and Update Processes
Regular reviews of critical spare parts management practices help ensure that they remain relevant and effective. Consider implementing scheduled assessments of inventory levels, data accuracy, and software performance to maintain optimal operations.
Navigating MRO Inventory Challenges
Effective management of critical spare parts is crucial for maintaining operational efficiency and minimizing downtime in MRO inventory. By adopting best practices such as defining material criticality, leveraging AI technologies, and engaging users in the decision-making process, organizations can significantly improve their critical spare parts management.
In an increasingly complex business environment, the ability to adapt quickly and make data-driven decisions is essential. By integrating advanced technologies and strategies, your company can ensure it’s well-equipped to navigate the challenges of MRO inventory management while optimizing critical spare parts processes. As you consider your critical spare parts management strategies, remember that continuous improvement and adaptation are key to thriving in today’s dynamic business landscape.
Ready to learn more? Download our webinar to explore how AI can help define spare parts criticality methodology.