4 Common MRO Inventory Challenges and How to Solve Them
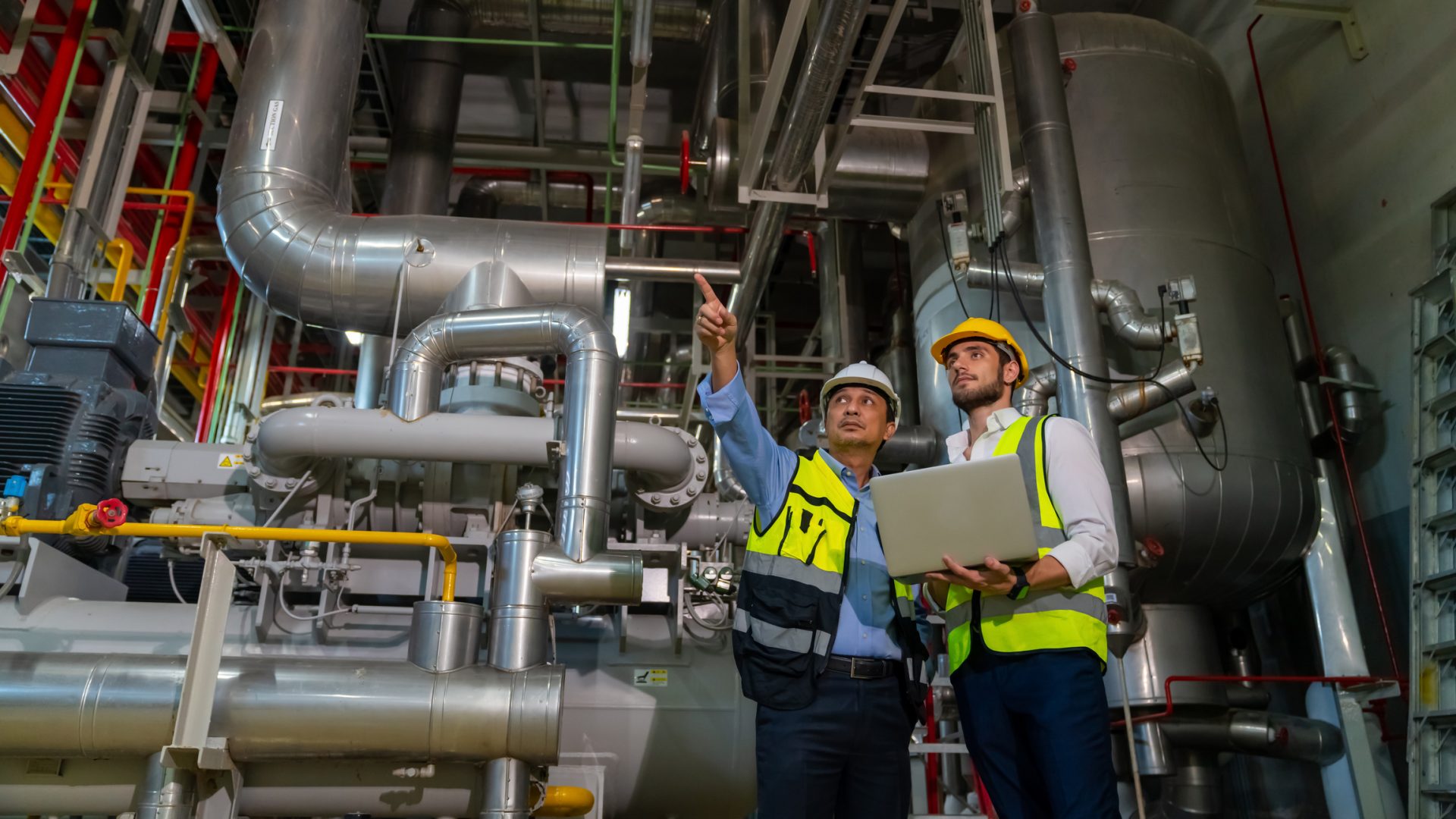
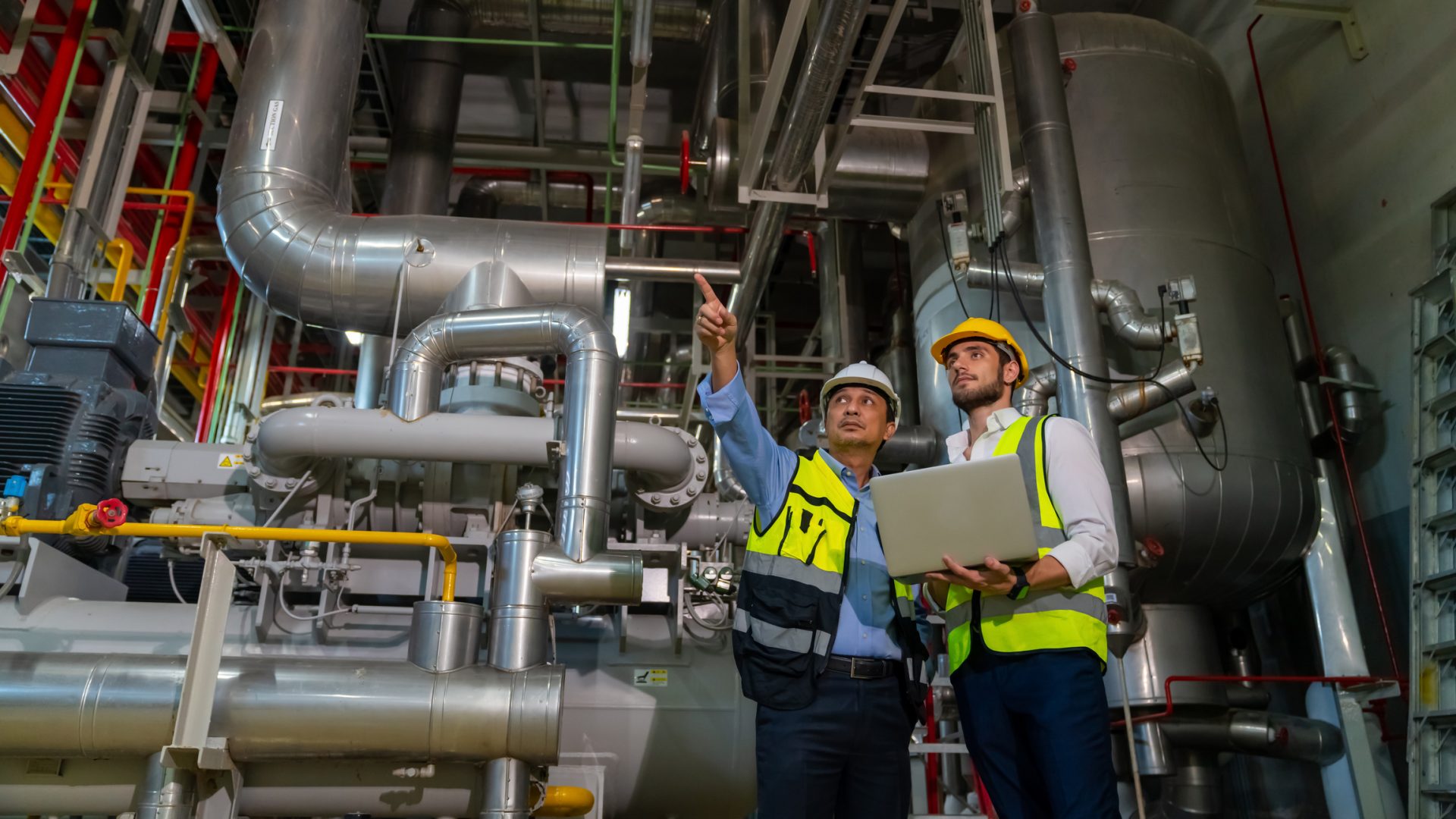
Managing MRO (Maintenance, Repair, and Operations) inventory is fraught with challenges due to the complexities of handling spare parts. As a result, many organizations experience analysis paralysis, unsure of how to optimize their MRO inventory management strategy. In this blog, we explore 4 common MRO inventory challenges hindering asset-intensive organizations and suggests solutions.
1. MRO Inventory Management Data Challenges
Data quality, completeness, and governance are major issues in MRO inventory management. Unfortunetely, organizations often rely on many different systems like ERP (Enterprise Resource Planning), EAM (Enterprise Asset Management), and P2P (Procure-to-Pay) to manage business data, leading to messy data that’s almost impossible to analyze. Furthermore, these problems get compounded by mergers, acquisitions, and system upgrades that bog down IT teams to the point that MRO data never really gets addressed. Add in supplier inconsistencies and internal classification issues, and your MRO data management just gets trickier.
While inconsistent MRO inventory entries make verifying actual stock levels difficult, manual data analysis, often done in spreadsheets, makes it impossible to draw definitive conclusions about MRO inventory SKUs. As a result, many organizations view MRO inventory management as an unavoidable cost center instead of a strategic function.
2. Aligning Operations and Procurement
Aligning procurement and operations teams is challenging due to their misaligned incentives, causing these teams to work in siloes. MRO procurement professionals focus on cost control and efficient spending, while operations and maintenance professionals prioritize asset uptime and production output. As a result, operations and maintenance teams often overstock parts to ensure availability during unplanned outages, leading to conflicting goals and ineffective collaboration.
Adversely, procurement teams may lack firsthand experience of plant floor urgency, which convinces maintenance teams to engage in rogue purchasing to maintain parts availability. Ultimately, this mistrust in MRO inventory data exacerbates misalignment, resulting in unchecked MRO inventory spending.
3. Risk of Stockouts and Outdated Criticality Assignments
Data challenges, decentralization, and an inherent lack of trust in MRO materials data leads to poor visibility around potential stockouts, which puts teams at risk of extended unplanned downtime. With naming conventions and lack of standardization causing ERP systems unable to locate parts, maintenance teams order costly expedited replacement parts during outages.
Additionally, mislabeled or outdated criticality scores for parts increase the risk of stockouts for essential items that should be ordered and stocked in higher quantities. With these materials often being used across assets within a plant, it’s imperative that their critical assigments stay up to date to reduce risk within your production operations.
4. Changing Priorities from Leadership
Unsurprisingly, leadership priorities in large enterprises often shift, meaning strategic MRO inventory management optimization is postponed. Manufacturers and supporting technologies typically focus on optimizing direct materials and finished goods, leaving spare parts and MRO inventory management neglected.
With new ERP upgrades or migrations dominating budgets and IT resources, organizations can be hesitant to adopt additional technologies for fear of disrupting ongoing projects. Also, leadership teams often disconnected from daily asset maintenance processes may not prioritize MRO inventory management needs, putting them at risk of significant waste regarding excess inventory.
By addressing these common MRO inventory management challenges—improving data quality, fostering better alignment between procurement and operations, enhancing visibility into stock levels, and maintaining consistent leadership focus—organizations can begin to effectively optimize their MRO inventory management strategies.
The Power of AI
Fortunately, these common MRO inventory challenges are addressable using AI-powered solutions. With many vendors claiming to provide AI capabilities, it’s important to evaluate technology that has been purpose-built for MRO inventory management and optimization. This ensures that the AI powered models supporting the system have the complexities of MRO inventory management built-in and understand MRO challenges. With AI now considered a must have for organizations moving forward, choosing the right solution for your MRO optimization strategy will be crucial.