3 Must-Have Features for Inventory Optimization Solutions (and 2 to Avoid)
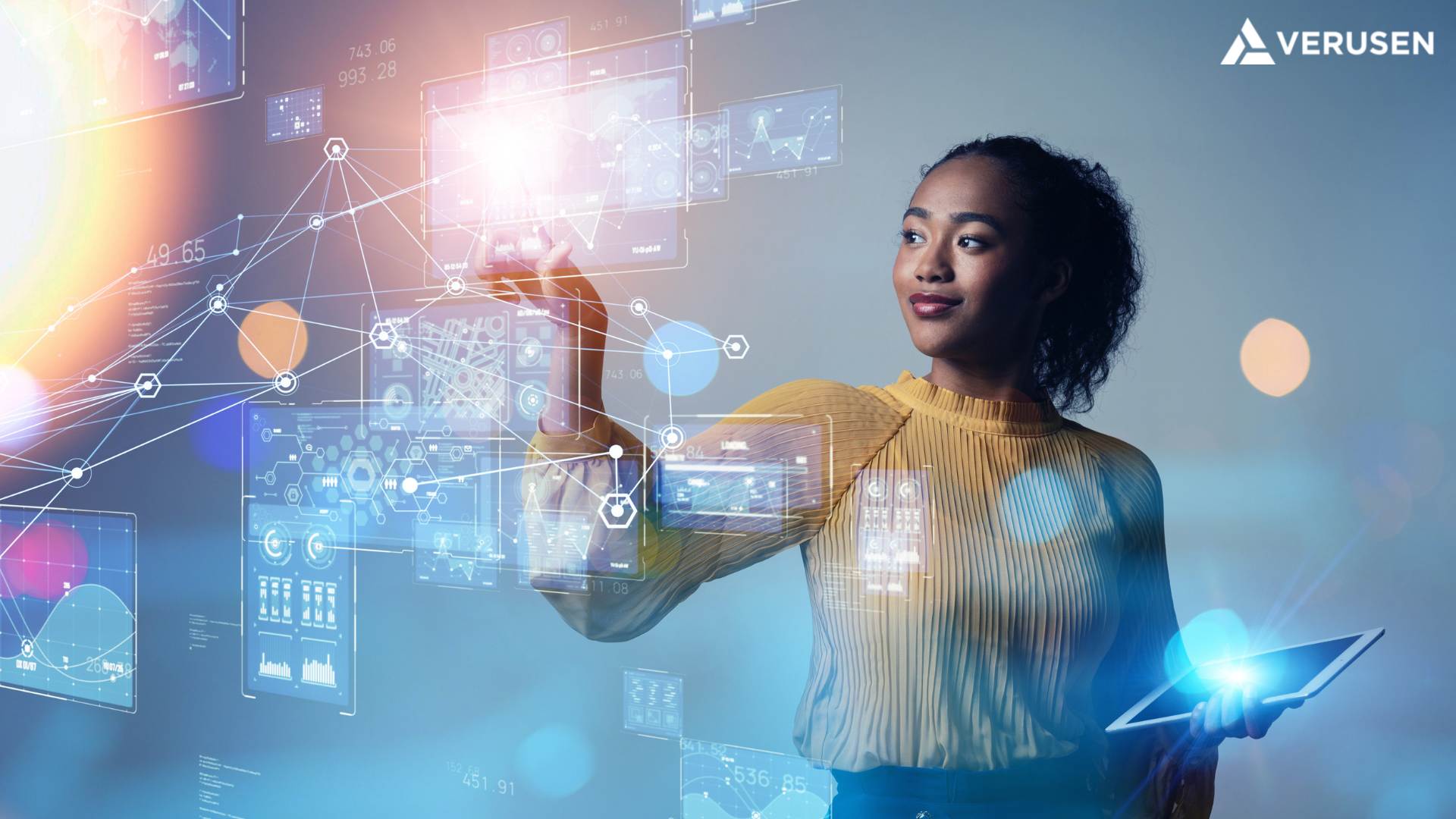
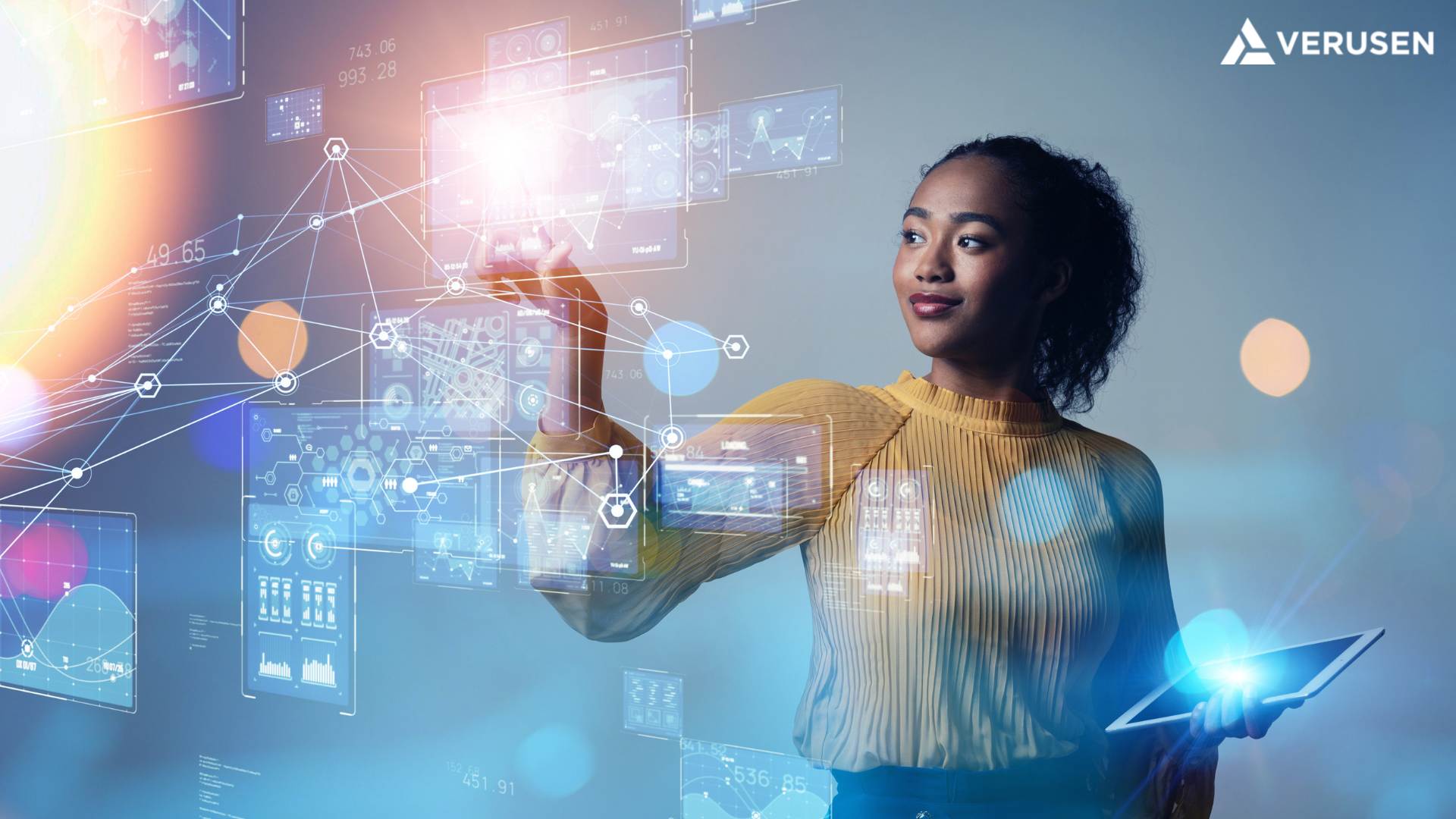
With real-time data insights, you can take decision-making and supply planning to the next level, reducing risk and saving you valuable resources.
Inventory Management Optimization is a modern process of supporting streamlined sales, operations, and supply planning that reduces the need for excess inventory and ultimately reduces risk within manufacturing processes.
There are a spectrum of benefits associated with adopting technologically advanced inventory management systems that historical systems have often lacked.
These benefits include better visibility across the supply chain, a reduction in storage and operational costs, improvement in service levels, and as mentioned previously, a reduction of risk across supply chain ecosystems.
This article examines the key characteristics your inventory optimization strategy should include, as well as the latest capabilities that are improving visibility within inventory management software. Moreover, we will explore what facets to avoid with inventory management software and why it may be wise to steer clear.
3 must-have features for inventory optimization software
Real-time data visibility
Overseeing and maintaining a comprehensive enterprise inventory management system is a foreboding task and one in which improved data visibility can provide a host of benefits.
Consistently meeting customer and business demand requires consistent and modern optimization to ameliorate MRO inventory tracking and utilization. As the complexity of regular business dealings increases, implementing tools that harmonize system data to increase visibility can keep your head above water and your operations running smoothly.
Data visibility metrics include transactions, SKU variances, and business unit distribution outlets that if regularly monitored and supported through inventory management visualization software can be optimized to more efficiently schedule critical maintenance and repair materials, eliminate stock-out situations or excessive inventory, and predict future company needs via historical use analyses.
AI-driven data analytics and decision support
Traditional analytics tools can only do so much for your data visibility and decision-making.
With recent improvements into data-driven inventory management, previous methods of inventory optimization fail to scale to address the complexity of company growth and lack the real-time insights needed to reduce redundancy, supplier variability, and critical stockouts.
The solution: AI and Machine learning. These modern optimization capabilities have seen significant improvements in recent years and can reach a level of speed, scale, and granularity that previous methods simply can’t compete with.
Employing big data analytics and real-time insights within your MRO inventory management processes allows for more informed decision-making and allows for strategic advantage over manual data cleanse exercises from legacy and disparate systems.
Not only will AI integration improve decision-making, ultimately optimizing costs and reducing wasted resources, but it will significantly reduce the risk to your business. AI is able to comb through piles of data to find where your business could be exposing itself to possible breaking points or excess spending.
Moreover, it provides businesses with dynamic MRO materials management. This is contrary to traditional methods; businesses historically set a static quantity or safety stock measurement for their inventory levels. With today’s increased customer expectations and enterprise engagements, it is often no longer feasible to employ general information to combat unexpected production downtime.
A centralized cloud-based solution
Another strong aspect of any modern inventory management software is cloud integration. Cloud-based providers guarantee total uptime at 99.9%, preventing system downtime and subsequently wasted resources and risk.
Since cloud-based tools operate under a software-as-a-service model, businesses can utilize these modern features while maintaining extra funds to invest in other services.
Additionally, a benefit of cloud computing is cross-enterprise access to data and decision-making. This allows for advanced cloud platforms to aggregate data from a multitude of disconnected systems to provide users with the necessary information regarding needed materials. For example, staff working in a production facility can scan and track inventory with their device and have the data uploaded instantaneously for an inventory manager’s viewing.
Not only does this provide boosted productivity for individual facilities and the overall enterprise, but plant managers and maintenance teams gain confidence through improved stocking and material visibility that a real-time analytics centralized cloud-based solution offers.
Operating a centralized model will ensure all facets of inventory management, such as delivery time or MRO items, are considered when scheduling maintenance schedules or dealing with emergency outages. This ability will be crucial for businesses implementing Industry 4.0 capabilities and aims to drive profitability and growth through smart solutions.
The Internet of Things (IoT) is a contemporary example as it drives how businesses track maintenance and asset management needs through the use of interconnected smart devices.
2 mistakes to avoid in inventory optimization software
Thinking an ERP system is sufficient
ERPs have several limitations due to lacking the detailed insight into company processes that other solutions or departments employ. By offering an all-in-one system, they attempt to manage everything at once and ultimately fail due to a lack of decision-assisting resources.
With an all-in-one model, ERPs lose the ability to manage company settings by channel account, quantities, business unit requirements, or location routing. As a result, the increased risk that ERPs alone bring to MRO inventory management can cause inventory inaccuracies such as duplicates or stockouts.
Features of modern systems, such as customizable reporting, are often absent in ERP systems. With an ERP system, businesses receive data that a provider assumes will be helpful – an often one-size-fits-all report that is service-level dependent and not reflective of the real-time data insights that improve MRO inventory management.
Lack of Performance Measures
While AI and machine-learning-driven solutions take most of the predictive analysis out of your hands, setting performance measures is still necessary to monitor system improvement and reduce waste.
To state the obvious, it’s difficult to address inventory shortfalls with no clean standard to measure them against. For example, common MRO material requirements like storage space efficiency or supplier management can appear as easy processes to improve, but without the real-time data that performance measures provide, implementing said upgrades is difficult and may not actually result in the outcome you desire.
Key Performance Indicators (KPIs) can ensure organizations track whether they are meeting optimized performance levels within inventory management processes.
Following a standard measure of tracking performance, these indicators can be used to find places for improvement. Examples of common metrics include better customer service, optimized inventory turnover, less MRO spending, and a host of other standards that can be tailored to your industry.
The ultimate aim of monitoring performance within these systems is to compare actual on-hand dollars versus forecasted usage of MRO materials. In conjunction with AI-driven inventory optimization software, performance measures allow you to find chinks in your company armor and plan ahead to reduce waste and risk.
Conclusion
The reduction in risk that a centralized cloud-based solution, AI-driven data analytics and decision support, and real-time data visibility provide can help manufacturers optimize costs, maintain production needs, improve customer service levels, and ensure the right materials are in the right place at the right time.
Ensure the safety and success of your business by implementing these modern solutions. By considering the factors listed above, businesses can do just that, and minimize supply-chain disruption while adding value through smart management practices. To learn more about reducing supply chain risk through MRO optimization, download the white paper on MRO optimization today.