Are We Finally Seeing the Death of the Data Cleanse?
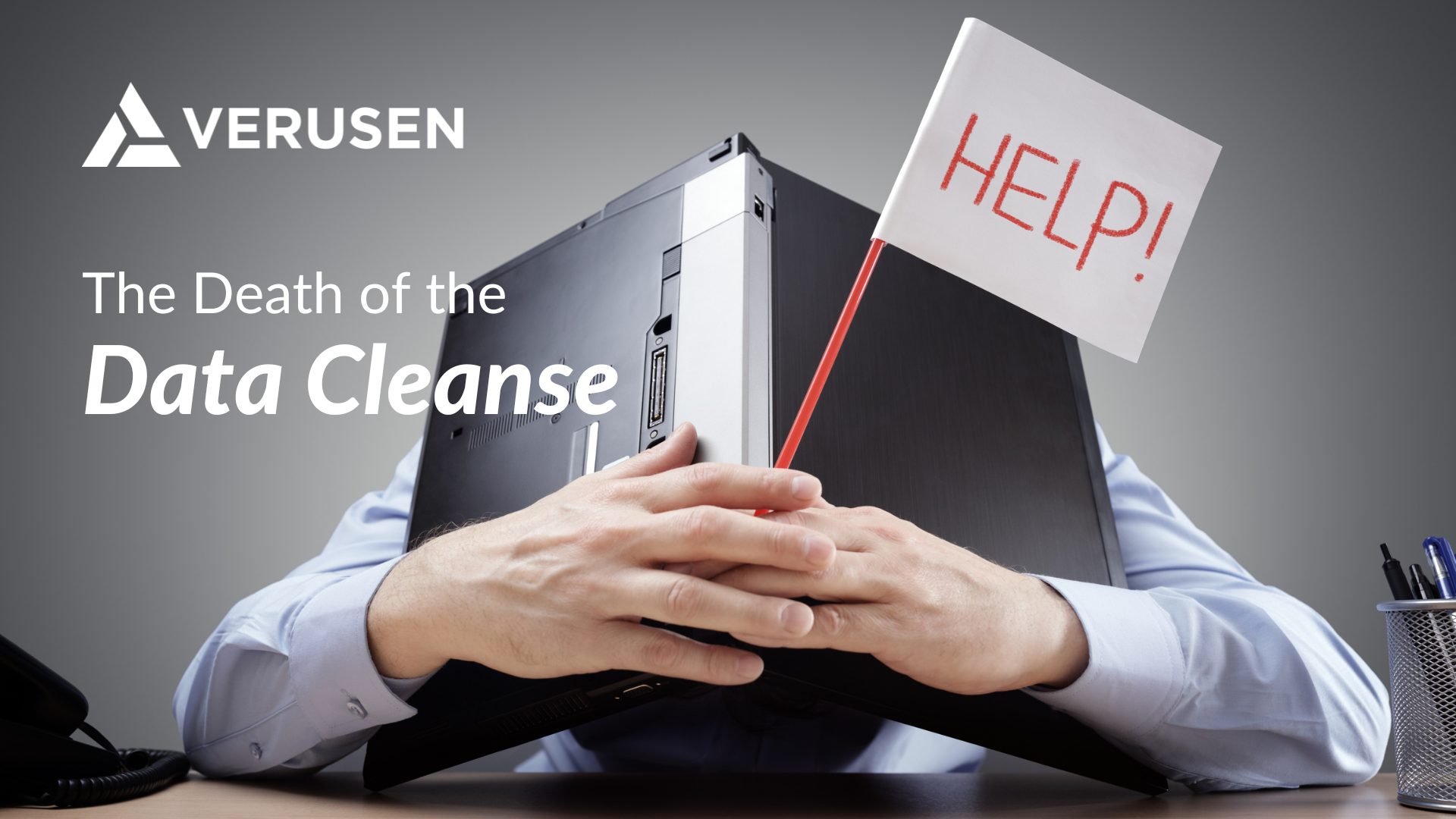
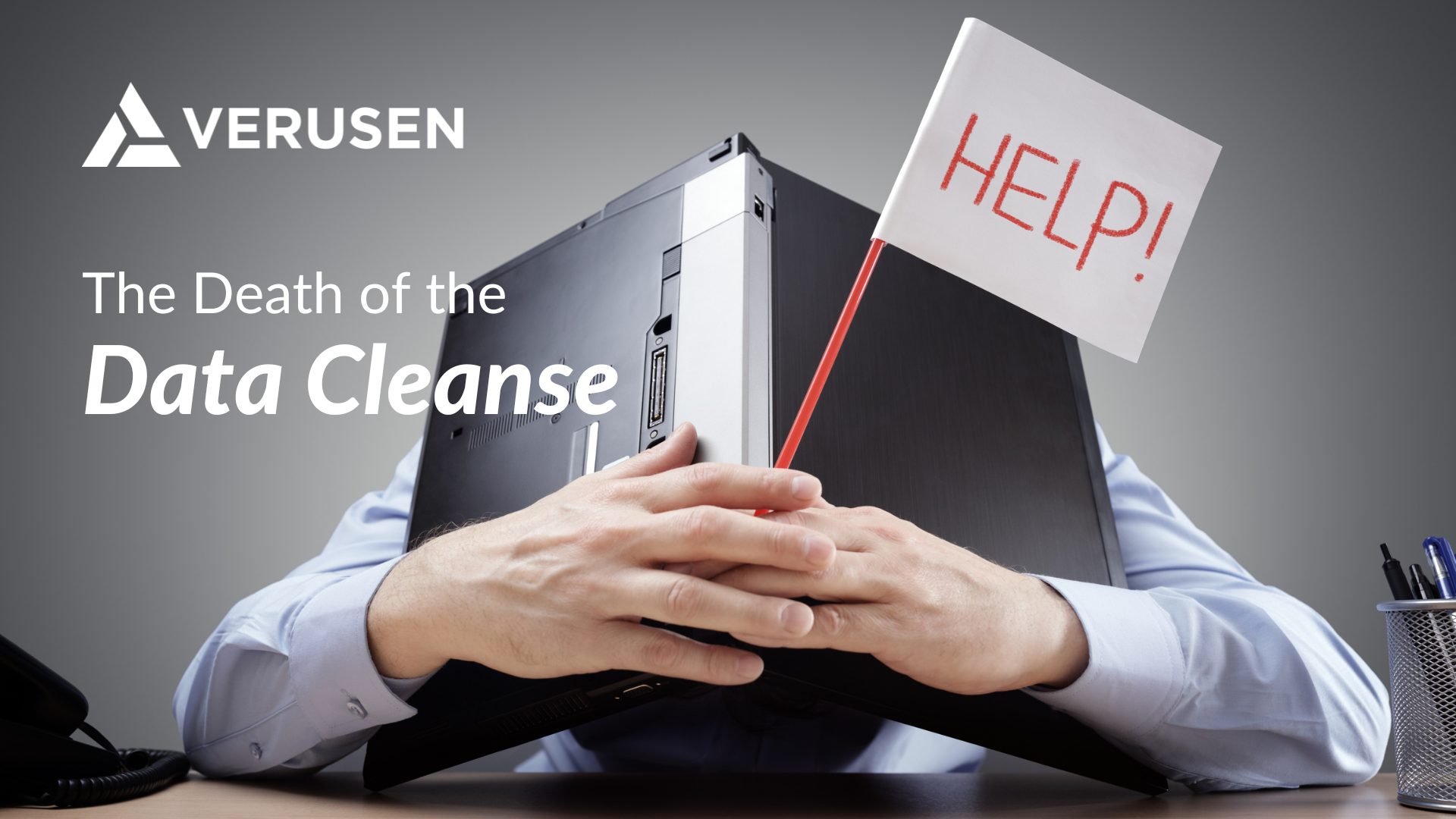
For some reason, the data cleansing initiatives manufacturers find themselves wasting money on time and time again just won’t go away. Not only is it a complex, multi-step process that requires a specialized set of software, people and procedures, it’s typically handled by internal resources whose time could be better spent on more pressing matters or expensive consulting firms who don’t really understand the nuances of your business. Whatever route is chosen, it’s a drain on human and financial capital, which is why this antiquated data cleaning process is in a death spiral. And it’s time to finally put it to rest.
Internal data cleansing is a monumental waste of valuable team resources
From an internal point of view, your Master Data Management (MDM) or Information Systems (IS) team is charged with keeping materials data clean and free of redundancies, while providing guidance based on insights gleaned throughout the process. These teams are on the front lines of managing bad data, so they spend vast amounts of time, effort, and money on a laborious manual process that typically involves serious spreadsheet management. This effort is an ongoing battle that not only remains a constant drain on valuable company resources, it robs your talented team of opportunities to work on projects that truly matter to your organization..
Costly external cleansing compromises your data
You may be a company that opts to hire external consulting firms that often use offshore resources to clean your data and provide data exports. Their teams spend cycles manually checking the data and then cleaning it up for export back into the company’s ERP or other inventory management system—and that can take months. The real issue is that once the cleansed data is uploaded back to the system, it quickly becomes dirty again if controls aren’t put into place to avoid bad data habits, such as inconsistent part naming across the organization.
The other downside of this approach is the hefty bill it brings. Depending on what’s included, the typical cost for data cleansing for a database of 10,000 records ranges from $5,000 to $15,000.
Although the expense is high, the cost of having unreliable data, production, and order deliveries is even higher. The manual nature of these short-term approaches begs for a better solution. Luckily it’s out there.
Getting past “AI” as just another buzzword
Artificial intelligence (AI) has been around for quite some time now, even if it still feels like a buzzword when it comes to enterprise technology. IBM’s Watson and Apple’s Siri have been in the hands of users for years, yet it’s not uncommon for technology adopters to be skeptical when they see AI listed in the feature specs. The reality is that AI is far more mature than many organizations realize and offers companies the option to accurately and efficiently self-cleanse their materials data in real time.
The average Fortune 500 manufacturer has anywhere from $40-$60 million in wasted working capital tied up in excess parts (and up to $100 million for just four weeks of inventory in some industries). “Dirty” data is a huge part of this costly problem. Redundant and disorganized MRO inventory results in over-ordering, obsolete and overstocked items, and inaccurate inventory forecasts. For these reasons, manufacturers often choose the archaic data cleanse project, but it’s time and resource heavy, which is why turning to a purpose-built solution for its inventory optimization project.
With software designed to optimize materials data, companies have been able to lay the appropriate data foundation by structuring its materials management (MM) data in weeks instead of a full year. The AI and machine learning platform automates the material entry process and harmonizes the inventory data across all MM catalogs. It also provided an accurate, trustworthy view of enterprise MRO inventory as required.
The platform adds additional value by ultimately cleansing the MRO data, allowing the company to begin its own “self-cleansing” data strategy, as well as an internal “buy-from-self-first” inventory optimization strategy. Additionally, once the data is cleansed, the platform delivers optimized insights on where inventory could be reduced as well as how to avoid creating additional excess. Not only does this save time and money, it provides your team with the ability to make strategic decisions for the business, essentially making them happier about the work they are doing.
AI Tolls the Bell for the Traditional Data Cleanse
With new technology driving actionable results quickly and easily , the death knell is obviously ringing for data cleansing as it’s currently known. The static traditional methods lack the injection of human intelligence as well as the ability to learn and infer. With the operational enhancements manufacturers receive from AI for data cleansing, companies continuously build knowledge and improve their inventory management without draining financial or human capital. It’s a win for your organization; it’s a win for your team.
To learn more about how you can move on from traditional data methods, check out our ebook on why MRO inventory is critical to advancing your enterprise network.