How AI Removes the Need for MRO Data Cleansing in Inventory Management
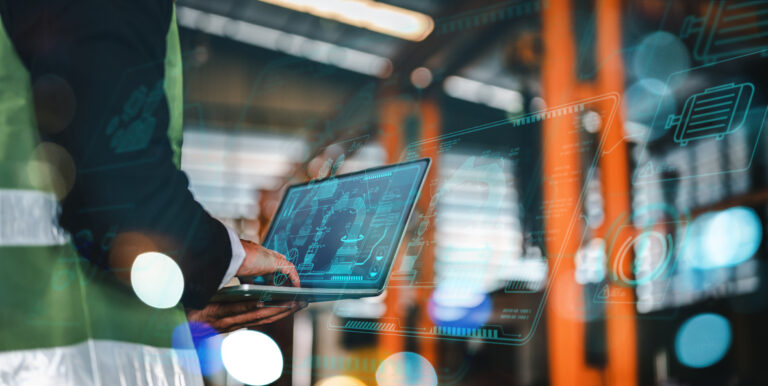
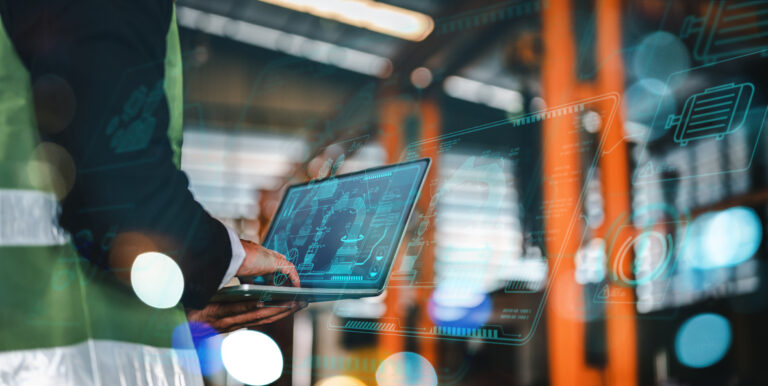
How AI Removes the Need for MRO Data Cleansing in Inventory Management
All asset-intensive organizations and manufacturing enterprises understand the importance of maintaining quality MRO (Maintenance, Repair, and Operations) inventory data so they can accurately manage critical spare parts and materials while controlling costs. But it’s just not that simple. Most organizations find themselves unable to keep up with disparate systems, manual processes, and heterogenous variations that challenge the MRO master data management (MDM) processes when it comes to MRO inventory management and purchasing.
Unfortunately, the common response to solving dirty data challenges is a traditional MRO data cleansing project. Yet they’re lengthy, costly, and rarely provide little real value. New capabilities in AI allow your organization to fill in the gaps using your existing MRO inventory data in its current state to achieve the results you want.
AI’s Ability To Bypass MRO Data Cleansing
AI models that are purposely built for MRO inventory optimization allow procurement, operations, and maintenance professionals to gain unmatched insights around their MRO inventory management and purchasing strategy.
Natural Language Processing (NLP) allow Large Language Models (LLM) to process disparate, heterogenous MRO inventory data for hundreds of thousands of SKUs to provide decisions around excess materials and duplicates, shortages, stocking policies, criticality assignments, purchases history, supplier management, part sharing, and more. The models can ingest data to identify commonalities in material IDs and part names to provide all relevant information in a single platform. Organizations using these capabilities achieve results in days, rather than months or years.
Benefits of AI-Powered MRO Inventory Optimization
Improved MRO Inventory Accuracy
With MRO inventory management often placed on the backburner, many organizations never uncover opportunities to reduce stockouts of critical inventory or areas where overstock situations have occurred. These issues typically stem from outdated stocking policies, the absence of “always on” criticality reviews, or runaway tail spend.
With AI allowing organizations to analyze inventory data without requiring MRO data cleansing, maintenance professionals can quickly review material recommendations to determine which critical items need higher inventory levels and where to update stocking policies to reduce overmax levels that result in write-offs or disposition. With these recommendations, and corresponding analytics in hand, purchasing teams can enhance demand forecasting and MRO supply planning to ensure they are reducing the risk of unplanned downtime while only carrying what they need.
Increased Operational Efficiency
Increased operational efficiency is the benchmark of successful MRO management. Achieving higher efficiency levels translates directly to smoother operations and a more reliable production environment. By optimizing MRO inventory management, organizations can significantly reduce costs, risk, and the time spent searching for parts, coordinating procurement, and managing inventory. These process improvements allow maintenance teams to focus on planned, preventive maintenance tasks, thereby extending equipment life and reducing the likelihood of unexpected breakdowns that result in delayed orders and minimized profits.
Streamlined MRO Inventory Procurement
Streamlining MRO inventory procurement processes ensures maintenance and reliability crews have the right parts at the right time. Simplified procurement workflows drastically reduce the time and resources spent on purchasing, creating quicker turnaround times for maintenance. By adopting AI-powered MRO materials management solutions that help to centralize supplier relationships, companies reduce administrative overhead, improve accuracy in stocking levels, and ensure compliance with procurement policies.
Reduced Unplanned Downtime and Maintenance Delays
Unplanned downtime is an ongoing challenge that can disrupt production schedules and lead to substantial financial losses. But it doesn’t need to be. For MRO teams, reducing unplanned downtime is a top priority, and optimized MRO inventory management plays a crucial role in this effort. By ensuring that critical spare parts are always available and that maintenance activities are planned and executed efficiently, companies can avoid the costly repercussions of unexpected equipment failures.
Improved Service Levels from Reduced Downtime
Reduced downtime is directly tied to improved service levels. For MRO procurement and maintenance teams, maintaining high service levels involves ensuring that the necessary parts and tools are on hand to meet planned maintenance needs and quickly address unplanned downtime when it occurs. When downtime is minimized, the production becomes more predictable, leading to consistent service level improvement.
Cost Savings
Cost savings in MRO operations come from several sources, including more efficient inventory management, reducing excess and waste, avoiding stockouts of critical materials, and better MRO procurement practices. MRO professionals can achieve significant savings by optimizing MRO inventory levels to match actual usage patterns, thereby avoiding overstocking and underutilization of parts. Cost reductions are also realized through strategic sourcing, bulk purchasing, reduced tail spend, and negotiated discounts with suppliers.
Lowered MRO Inventory Carrying Costs for Excess and Duplicated Spare Parts
Carrying excess and duplicated spare parts ties up capital, creating additional costs related to storage, handling, insurance, and taxes. For MRO procurement and maintenance teams, lowering carrying costs is often a primary directive from leadership. Implementing an AI-powered MRO inventory optimization solution provides the key information for balancing stock levels, ensuring that only necessary parts are held in inventory.
Reduced Risk of Critical Shortages and Expedites
Managing the risk of critical shortages and the need for expedited orders is a constant challenge for MRO teams. A shortage of essential spare parts can halt production, leading to costly downtime and disruptions. Maintenance and reliability professionals mitigate this risk by implementing regular criticality reviews to ensure critical parts are always available. Using predictive analytics and consumption history, companies can anticipate future needs and avoid the pitfalls of stockouts.
Minimized Waste and Spare Part Obsolescence
Waste and obsolescence of spare parts represent hidden costs that can erode profitability in MRO operations. For procurement and maintenance professionals, minimizing waste involves closely monitoring inventory levels and ensuring that slow moving parts are stocked appropriately and used before they become obsolete. Effective inventory management systems help track the lifecycle of spare parts, allowing for timely reordering or disposal.
Challenges in MRO Data Cleansing
MRO data cleansing is challenging, as it involves identifying and correcting errors in vast inventories of spare parts and materials. Furthermore, it fails to provide any sustainable value for MRO professionals who often struggle with inconsistent and inaccurate data due to the integration of information from multiple sources and systems. These errors can lead to improper stocking, misplaced parts, and inefficiencies in maintenance planning.
Using artificial intelligence to assist with updating and maintaining data accuracy over time requires continuous effort and provides the always-on solution many organizations need. Addressing these challenges is essential for ensuring that MRO inventory data remains reliable and actionable.
Identifying and Correcting Inventory Data Errors
Inventory data errors can severely impact MRO operations, leading to incorrect stock levels, misplacement of parts, and inefficient procurement processes. MRO professionals must be vigilant in identifying and correcting these errors to maintain an accurate inventory database. This involves regular audits, cross-referencing data with physical stock, and employing AI-powered tools that can detect anomalies. Correcting these errors promptly ensures that inventory records reflect actual conditions, enabling more effective inventory management and reducing the risk of shortages or overstock situations.
Integrating Data from Multiple Sources and Disparate Systems
Integrating data from multiple sources and disparate systems is a common challenge in MRO data management. MRO professionals often deal with various databases, each with its own format and structure, leading to inconsistencies and errors. The integration process typically involves standardizing inventory data, reconciling differences, and ensuring that all systems communicate effectively.
Successful integration with a purpose-built MRO tool that is powered by AI allows organizations to avoid traditional MRO data cleansing projects and provides a single source of truth. These solutions enable more accurate decision-making and streamlined operations by achieving a unified view of inventory and optimizing procurement and maintenance processes.
Tools and Technologies for MRO Inventory Optimization
MRO inventory optimization relies heavily on the right tools and technologies to ensure that inventory levels are aligned with operational needs. Professionals benefit from advanced MRO data cleansing tools that automate error detection and correction, as well as sophisticated inventory management solutions that offer real-time tracking, demand forecasting, and analytics capabilities. When selecting MRO inventory management solutions, it’s important to consider features such as integration capabilities, user-friendliness, and scalability to meet the specific needs of your operation.
Case Study: Successful MRO Inventory Optimization Using AI
A Fortune 500 paper and pulp manufacturer was experiencing $75-$100MM MRO inventory write-offs approximately every five years. Fed up with running into the same issues and not being able to address them with single serving data cleanses that took too long and cost too much, they turned to an AI-powered MRO solution. With AI able to analyze their data in its current state, they have been able to consolidate MRO inventory data from multiple systems and business units into a single platform.
The solution has allowed them to scale their MRO inventory optimization efforts across the organization and implement network inventory optimization. Furthermore, they have been able to centralize their procurement efforts, freeing time and productivity of hundreds of individuals who can now focus on other priorities and business needs. To date, the organization realized over $50M in working capital reduction while simultaneously avoiding stockouts of critical materials that often prolong unplanned downtime.
The Journey to Effective MRO Management
Using AI for MRO inventory optimization offers significant advantages over traditional MRO data cleansing methods by providing more accurate and actionable insights into inventory management. By embracing AI-driven solutions, your company can achieve substantial cost savings, reduce downtime, and enhance overall operational efficiency. The journey to effective MRO management begins with accurate data, and the right tools and technologies are key to unlocking the full potential of MRO inventory optimization.
Download our whitepaper for more in-depth information on how to avoid the consequences of bad MRO inventory data.