Verusen helps leading Industrial Equipment manufacturer identify $20.9M in savings opportunities without increasing risk
$20.9M
Identified reduction opportunities
$55K/hr
Verified reductions in first 6 months
~2000
Materials identified at risk of stockout
800+
Material stocking policies updated
Our Client
One of the world’s leading manufacturers of industrial equipment and machinery
Key Business Needs
- Identify duplicate materials and excess spare parts
- Right size inventory stock levels through improved data standardization practices
- Reduce supply risk and assure supply to support facility reliability (i.e improve OEE)
- Ensure lowest total cost of ownership for MRO materials supporting manufacturing
Business Challenge
- Multiple ERP instances lead to disjointed management processes
- Decentralization allowed for unstandardized data practices
- Little to no inventory visibility across multiple sites
- Inability to identify duplicate materials and excess materials
- Procurement lacked insights to effectively manage spend
Solution
Verusen’s AI-powered MRO optmization inventory platform harmonized MRO data in a single platform from multiple systems simultaneously.
Additionally, our client was able to establish cross site visibility to on hand inventory. This has allowed them to review over 3000 potential duplicate materials. The company has established cost savings and cost avoidance opportunties by revamping outdated stocking policies across sites.
Watch This 3 Minute Demo to Learn More
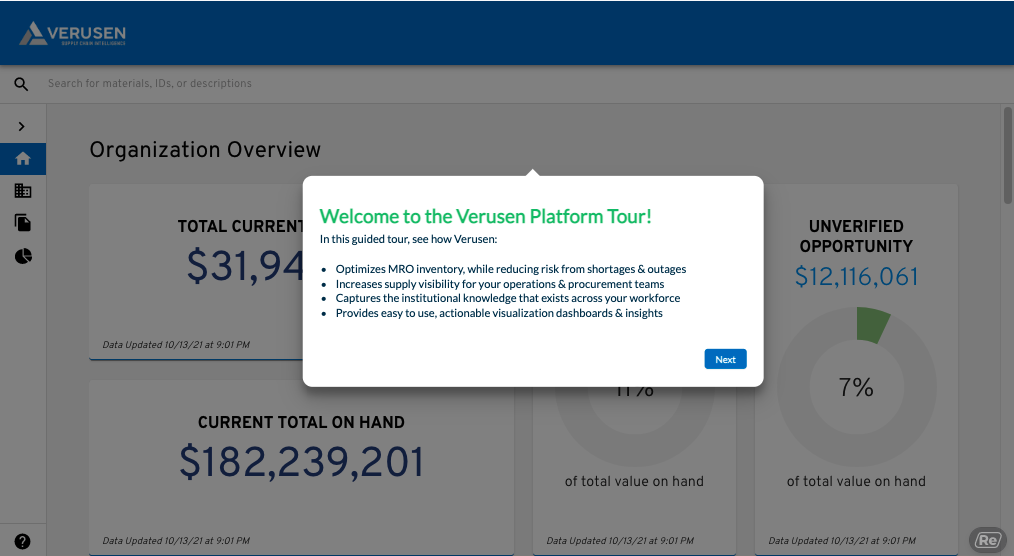
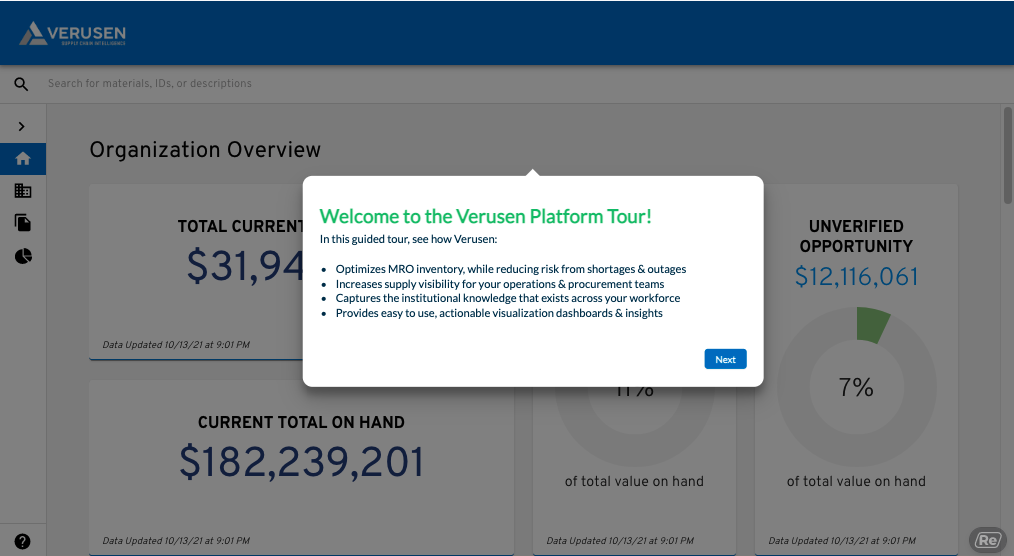