Creating Alignment for Strategic MRO Inventory Optimization
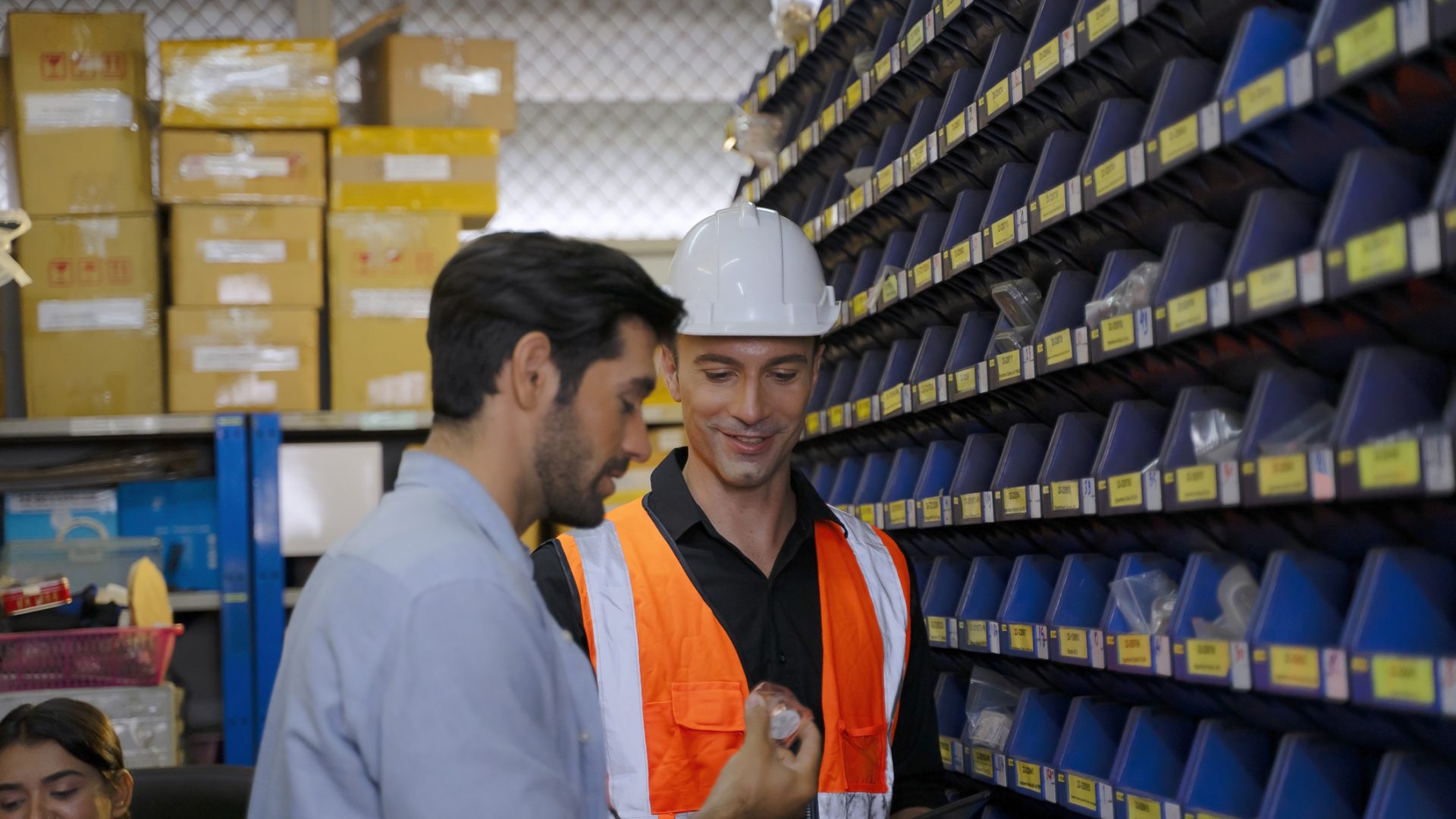
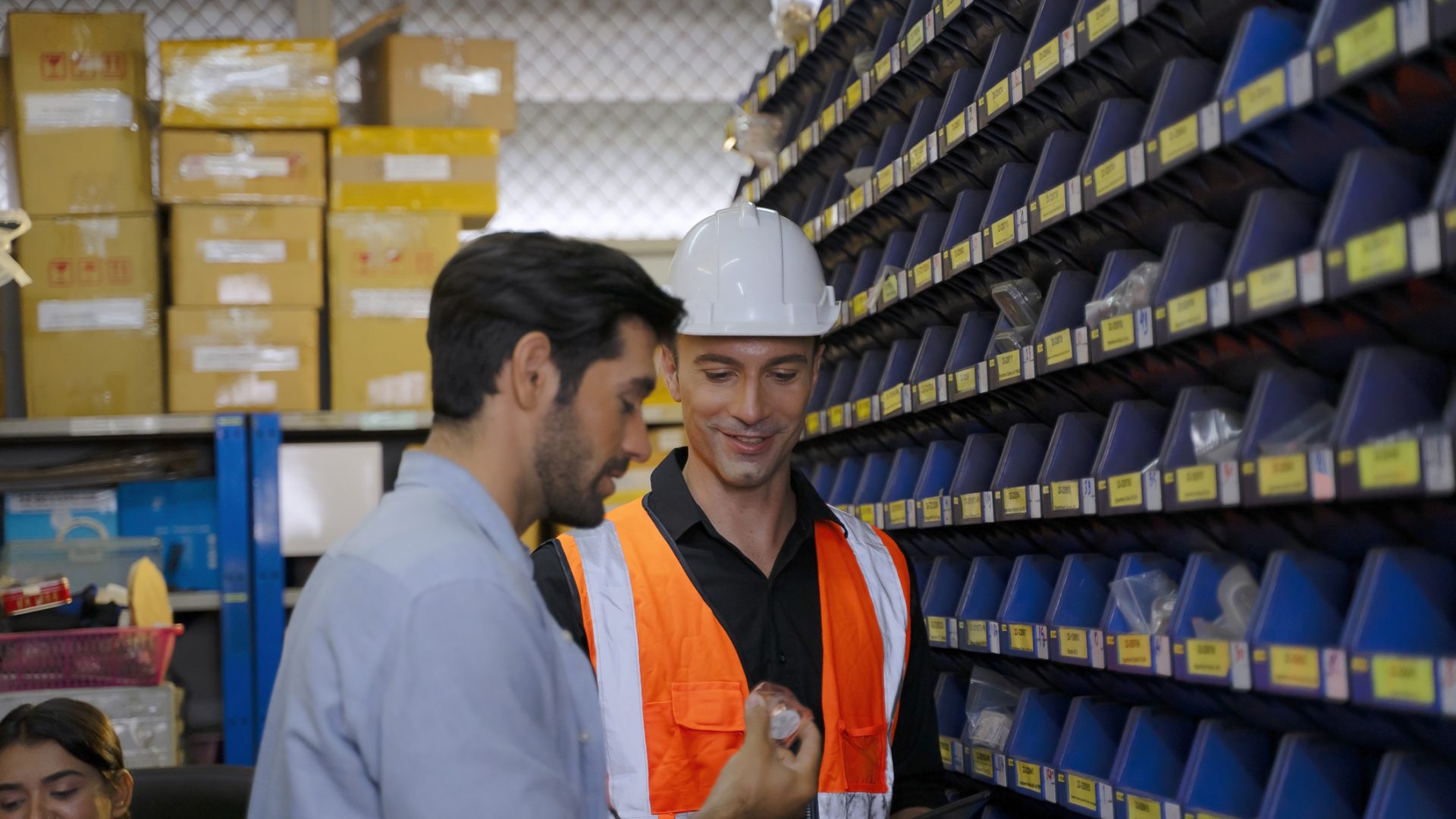
Achieving strategic MRO inventory optimization is a significant challenge for both procurement and maintenance professionals. The reliance on manual processes makes finding the right stocking levels for MRO inventory seem nearly impossible. Furthermore, when strategic MRO inventory optimization is not prioritized by the broader organization, it can feel like an uphill battle. In this blog, we break down the importance of creating cross-functional alignment to drive strategic MRO inventory optimization.
Lack of Top-Down Support for MRO Inventory Optimization
In many organizations, there are not enough resources to make MRO inventory optimization a strategic function of the business. This includes the professionals needed for ongoing evaluation of MRO needs, inventory analysis, purchasing, storeroom management, and maintenance. Each critical function is often stretched thin, causing inventory optimization initiatives to fall short.
Additionally, many organizations lack technology specifically designed for managing and optimizing MRO inventory. While some companies rely on ERP and EAM systems that promise MRO optimization capabilities, these systems are often data-dependent, siloed, and require multiple screens to review a single MRO material or spare part. The excessive time spent navigating these systems leads to overlooked excess inventory and critical stockouts.
Moreover, there may be a lack of leadership endorsement for MRO optimization efforts. Executives often prioritize optimizing direct materials and finished goods, overlooking the importance of MRO or deferring optimization efforts. As a result, MRO teams tasked with purchasing and managing MRO inventory feel shorthanded and undervalued.
Challenges Stemming from Reactive Maintenance
Unplanned downtime is a reliability and maintenance team’s worst nightmare. Many organizations have suboptimal practices for managing these scenarios. Without a planned and preventative maintenance strategy, the likelihood of unplanned events increases. An emphasis on run-to-fail maintenance further elevates the risk of not having the right part on hand.
Without proactive processes, such as hub and spoke modeling or criticality reviews, organizations face increased costs from prolonged downtime, spare part expedites, and rogue purchasing. Adopting a proactive strategy that includes technology for both planned maintenance and MRO inventory optimization can significantly reduce downtime costs without increasing working capital.
MRO Inventory Often Considered a Cost Center
MRO operations and the corresponding inventory are often seen as a cost burden not directly tied to profitability, leading to underfunding and oversight. This fosters nonstrategic practices such as rogue purchasing, p-card purchasing, and a lack of data capture. Consequently, optimizing both processes and inventory becomes challenging at the plant level and across the enterprise network.
Not Aligned with Broader Business Goals
In many organizations, MRO innovation is not a priority, leading to a misalignment with broader business goals. This results in a reactive rather than proactive approach to MRO risk management, failing to anticipate and mitigate potential issues before they escalate. Additionally, the loss of knowledge from a retiring workforce is often overlooked. As seasoned employees retire, their expertise and insights into MRO processes are lost, complicating efforts to maintain and improve operational efficiency. Without integrating MRO inventory optimization with overarching business objectives, companies risk increased downtime, higher costs, and diminished overall performance.
Creating alignment for strategic MRO inventory optimization requires top-down support, investment in specialized technology, proactive maintenance strategies, and integrating MRO goals with broader business objectives. This approach ensures the right parts are available when needed, reduces downtime, and enhances overall efficiency.