Auto Manufacturers Brace for Fresh Supply Chain Challenges from War, Seek Better Answers
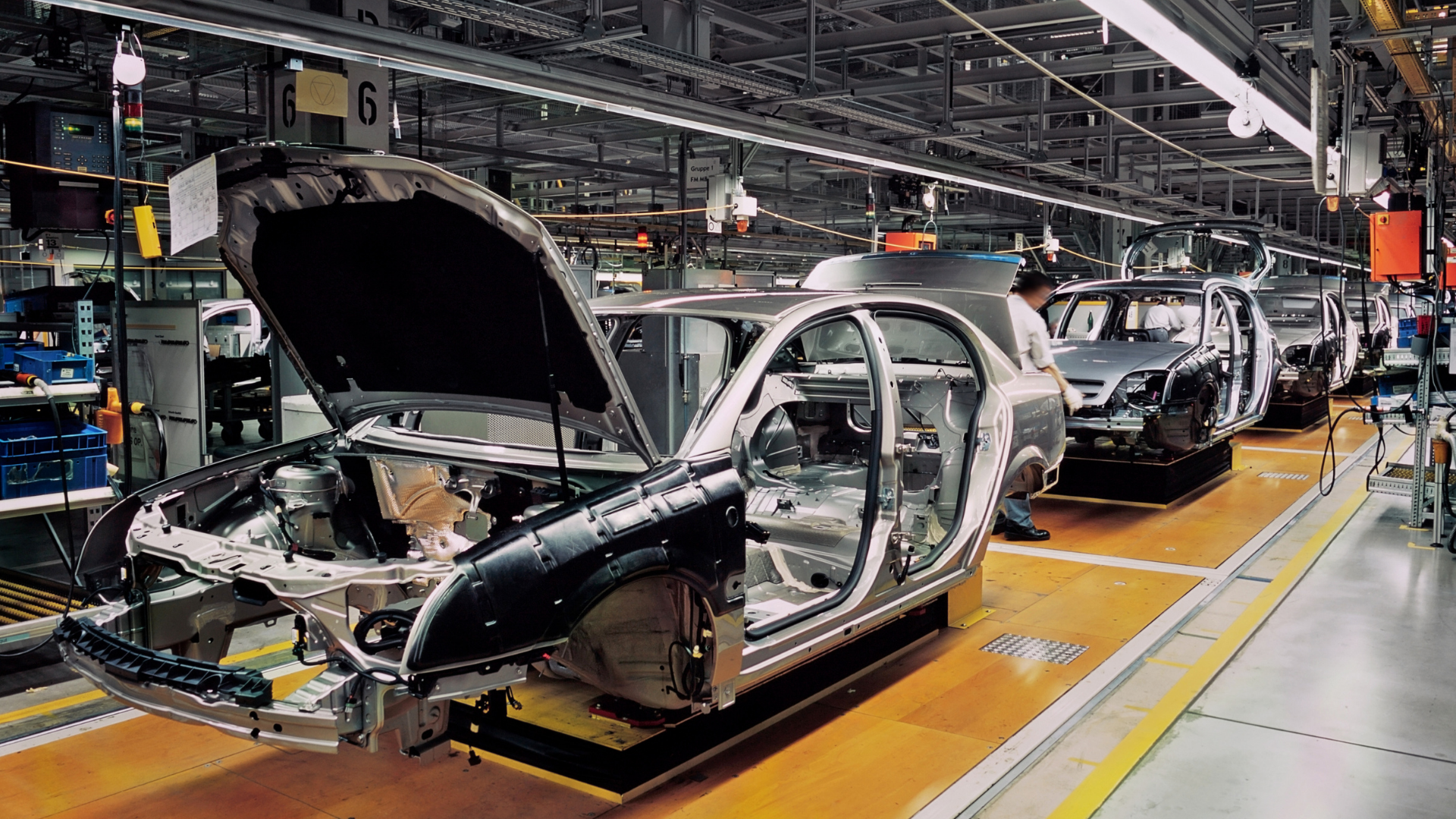
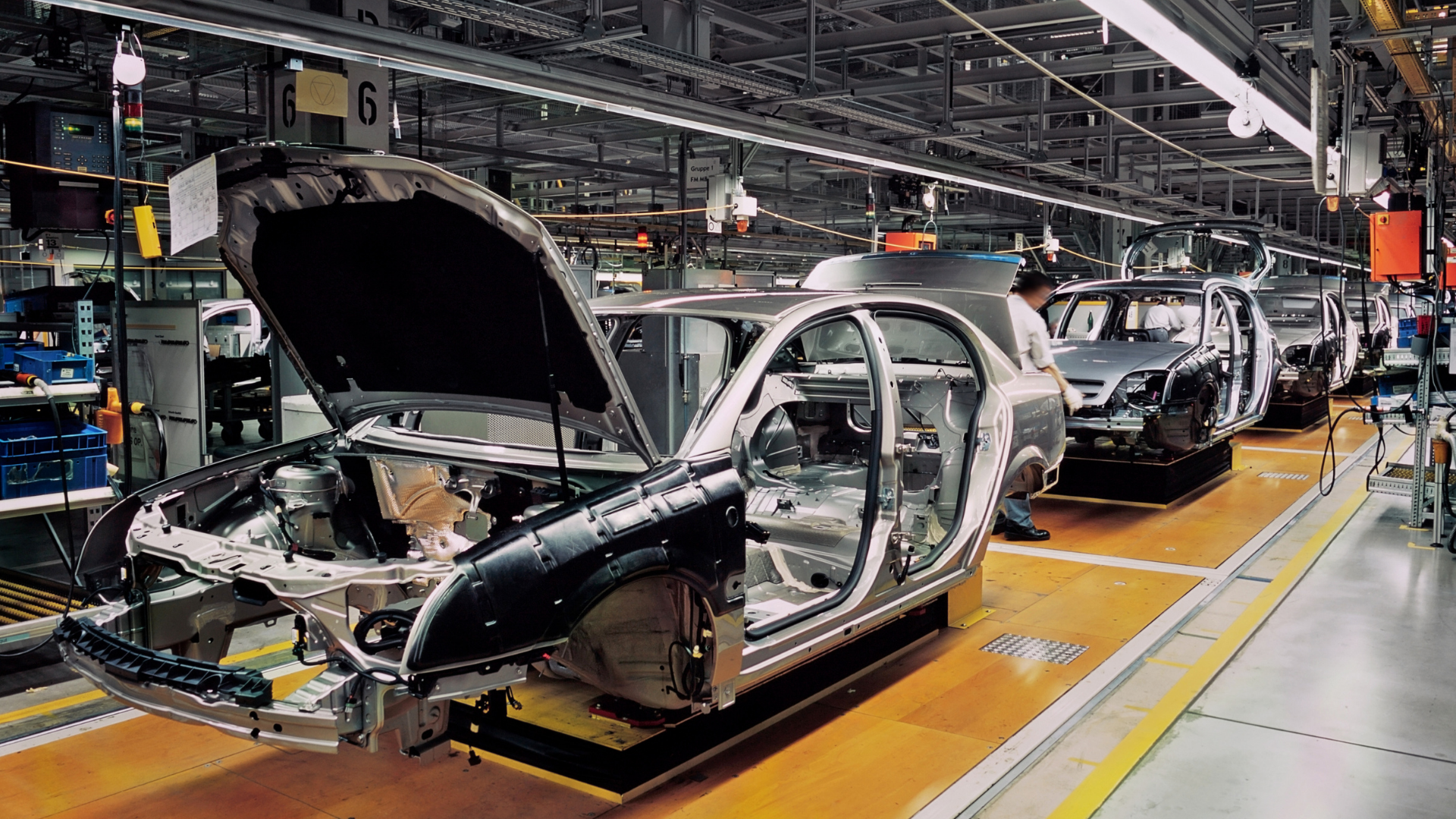
These are challenging times in the global auto industry. Constantly rising production costs and supply chain delays brought on by the war in Ukraine have combined to lower automakers’ annual sales forecasts. Final vehicle delivery is at the heart of the problem.
In fact, in March, S&P Global Mobility cut its global light vehicle production forecast by 2.6 million units for 2022 and 2023 to 81.6 million for 2022 and 88.5 million units for 2023 due to the Ukraine-Russia war. That’s a loss of some 5 million vehicles!
Consultants at LMC Automotive are even more pessimistic about auto sales in Western Europe. They noted recently that German automakers are shutting down plants due to the Russia-Ukraine war, to the tune of a loss of around 150K units in March alone. As a result, LMC also drastically lowered its percentage of 2022 auto sales in Western Europe to 3.6%, from an earlier rate of 8.3%. This further adds to supply chain woes stemming from the COVID-19 pandemic, which already featured a severe shortage of computer semiconductor chip parts and resulted in overall vehicle delivery being delayed by months for the past two years.
Such a sharp decrease in auto sales expectations has had a trickle-down effect on suppliers, partners, distributors, and other parties connected across the global auto industry’s supply chain. As a result, auto companies need to ratchet their operations in new ways. They must become agile and more resilient in their approach.
In a word, auto companies must optimize. Therefore, enhancing supply chain intelligence should be a top priority, using intelligent MRO optimization to elevate digital transformation.
Tracking Data
In the auto manufacturing supply chain industry, keeping track of large and sprawling materials inventories across global sites is a massive challenge considering the extensive web of parts and components sourced from various places. Unfortunately, this automotive manufacturing supply chain challenge often goes unmet due to data being in silos, disparate ERP systems, a lack of digital transformation, and data cohesion across these enterprises.
Steps for Automotive Industry Supply Chain Companies Facing Challenges
Auto manufacturers can make a substantial difference in their business outcomes by undertaking five Maintenance, Repair and Operations (MRO) inventory strategies to achieve cost reductions and do so without increasing risk or disturbing current operations:
Here are the key automotive supply chain steps to get ahead:
1. Leverage decentralized cloud software reaching across all internal systems.
The first crucial step in an auto supply chain strategy that automakers should look at is Integrating cloud services into their inventory management strategy. Centralizing data via the cloud allows review of MRO spending and supplies, enabling complete visibility and control of the flow of goods across the organization and interconnected global supply networks.
Cloud-based supply chain intelligence offers a host of advantages over analog inventory management, especially for automotive supply chain challenges. For example, it provides visualization tools that provide enhanced analytics around production aspects such as item usage history, optimized ordering to prevent stockout, lower cash spending on standing inventory, improved access to vendor catalogs and performance metrics, and equipment management.
These advantages extend across all facets of the business to increase visibility and ensure regular communication between all inventory systems in complex production networks.
2. Use available raw data to gain actionable insights into MRO inventory data
Data is only useful when it’s available and visible amongst other data it needs to connect with for decision making. For auto manufacturers, machine learning and AI-driven software provide new and productive opportunities for increased collaboration between finance, maintenance, and asset management, consolidating data from all sectors. For example, much of an auto manufacturers’ MRO inventory management has traditionally relied upon spreadsheets and much slower methods of communication. These systems may store relevant data, but they need to integrate with AI-enabled software that provides a more holistic view into the complex web of parts and components making the business run.
Accessing company data through easy-to-consume business intelligence (BI) tools delivers ongoing status checks into data, provides more immediate results, and ensures the optimal level of inventory remains stocked.
3. Implement cognitive computing technology with specific supply chain intelligence to identify duplicated materials and components
Eliminating redundancy and understanding inventories is the shortest path to streamlined production. However, a wide range of adverse side-effects of a partially visible supply chain, such as duplications, exist within the company procurement process. This happens primarily as changes in the supplier base allow for the introduction of updated model numbers, replacements, or substitutes listed under new part names or numbers, despite no substantial change to the actual items.
AI-integrated systems that identify and compare existing SKUs can provide methods of advanced inventory data creation and visibility with a significantly diminished probability of error.
AI-driven monitoring of MRO inventory items aids companies in locating and eliminating duplicates by providing increasingly accurate material visibility across the entire enterprise. Additionally, AI helps bridge the gap between past company processes and the present. Eliminating knowledge disparities ensures inventory data stays consistent during team member or company transition.
4. Using Real-Time Reporting and Analytics
Introducing process automation into regular business processes enables better tracking, planning, and management of inventory. In short, analyzing routine processes can help determine which strategic advantages can be gained. In addition, implementing centralized supply chain intelligence solutions, like an AI and machine learning platform, facilitates more accurate organization of materials, data, equipment, supplies and brings a plethora of other MRO cost improvements.
Using AI-driven automation to track MRO Inventory items improves supply and materials plans, allowing the company to predict future needs better. A preemptive step can prevent both stockouts or overstock. Shifts from typical supply chain operations to counteract an upcoming maintenance event or disruption are often a beneficial result of real-time reporting.
The increased visibility afforded by deep learning recognition makes AI an integral part of supply chain dynamics. With more control and dissemination, data is utilized to its true potential for companies to make better-informed decisions around their manufacturing operations.
5. Optimize inventories on an ongoing basis with deep learning along with human augmentation
Intelligent inventory decision-optimization adapts to current operational conditions, supplier trends, and user inputs. In addition, the integration of deep learning capabilities through AI takes this a step further to predict MRO material needs so that production downtime is minimal.
Realizing true material accuracy via supply intelligence support helps eliminate the guessing game concerning facility maintenance and repair by preventing costly inventory pitfalls like overstocking and furthering data-backed systemic changes to optimize supply chain processes.
Achieving MRO optimization requires real-time AI inventory management, enabling the tracking of critical performance metrics, such as replenishment lead times and equipment age, to start preemptive maintenance that helps reduce downtime, preserve service levels, and lower costs. Read more on supply chain strategy and challenges in the automotive industry at Verusen and how to improve MRO here.
Paul Noble, Founder & CEO of Verusen