Spare Parts Criticality Evaluation & Optimization
De-risk Your Operations with AI for Critical Spare Parts Management
The Impact of Outdated Parts Criticality
Nearly half (46%) of industrial and manufacturing enterprises fail to incorporate spare parts criticality into their materials planning process. Without consistent spare parts management, you face the expense of overstocking and the risk of stockouts—preventing you from having the parts you need at the right place, time and price.
Inefficient Procurement
Processes
Item criticality data is often outdated, unreliable, and inaccurate, leading to challenges in making informed procurement decisions and resulting in an imbalance of excess inventory and stockouts.
Inexact Criticality Assignment
Item criticality is often derived from an asset's criticality, gut feelings, and a "set it and forget it" approach—leading to expensive and inefficient excess inventory.
Unplanned Downtime and
Profit Loss
Outdated item criticalities can cause stocking policies to become misaligned with market changes, leading to risk of unplanned downtime exacerbated by stockouts of critical spare parts.
An Always-On Approach to Critical Spare Parts Management
Strategic stocking policies start with accurately reassessing parts criticality. Our AI-driven Spare Parts Criticality continuously evaluates both demand and supply-side factors, such as asset usage, work orders, Bills of Materials (BOMs), and market conditions. It’s always on, dynamically assessing how you assign criticality, identifying changes, and recommending adjustments in real-time. This ensures your stocking policies are aligned with operational realities, optimizing inventory and improving efficiency.
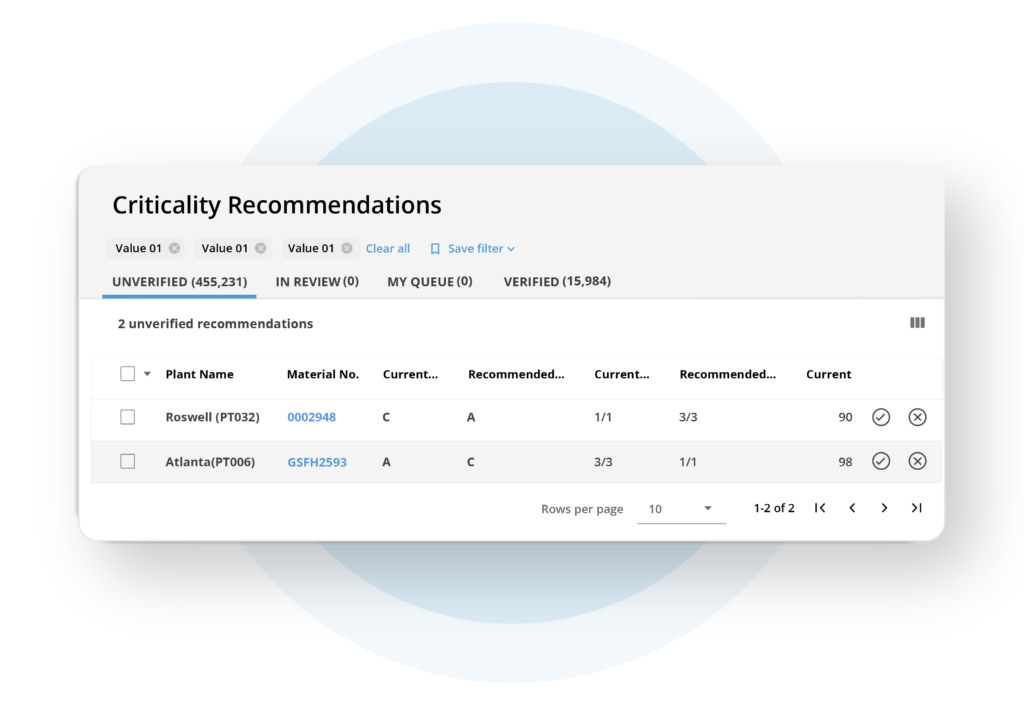
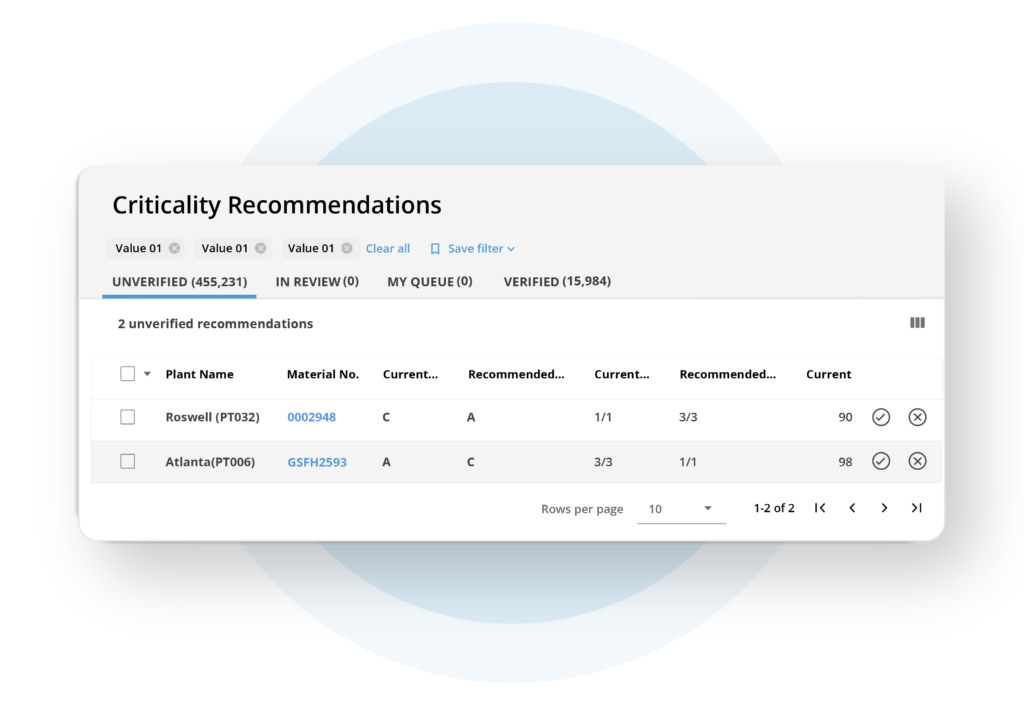
Our AI Platform
Ingests and understands the context of your material data
from your systems of record, such as work order and procurement history, supply constraints, lead times, etc.
Establishes and maintains item criticality
for your every spare part, while understanding dynamic market changes and operational risks
Analyzes and prioritizes
the most critical spare parts, ensuring optimal stocking policies for continuous operations
What's In ItFor You
Real-time insights into parts criticality and operational risk to drive data-informed stocking strategies
Risk-Based Approach
Align procurement and operations teams by evolving from gut feelings to data-driven objective assessments, ensuring you will have the right parts at the right time at the right place and price.
Bottom Line Impact
Prevent overstock and stockouts while unlocking savings by reassessing updated parts criticality of materials.
Confidence in Data
Ensure inventory materials are assigned optimal, up-to-date criticalities with our always-on solution to reflect their true priority to operations.
Transform Your MRO Supply Chain
Achieve data-driven procurement while holding operations accountable for balancing inventory needs, reducing redundancy, and minimizing waste.
Continuous, Automated, Always-On AI
Verusen’s AI platform uses advanced natural language processing (NLP) to tackle MRO inventory challenges. With over 20 million SKUs ingested, it enables immediate optimization without the need for data cleansing or third-party assistance, utilizing your existing data as-is.
Frequently AskedQuestions
Most Verusen customers are fully operational within 45 days from the time we receive the initial data transfer.
Typically, customer resources dedicate just 2-4 hours per week during the onboarding process. This is significantly less than what is required with traditional SaaS solutions, which often demand upwards of 30 hours from IT teams.
Verusen integrates seamlessly with a wide range of ERP, EAM, and P2P systems, using our comprehensive suite of certified, optional connectors to provide the insights and results you need.
Verusen doesn’t use seat licenses, so you get unlimited access for all relevant team members. Admins, chosen by you, can easily grant access to anyone in your organization who needs it.