Risk & Reward Through MRO: How AI Is Tackling Manufacturing’s Billion-Dollar Parts Problem
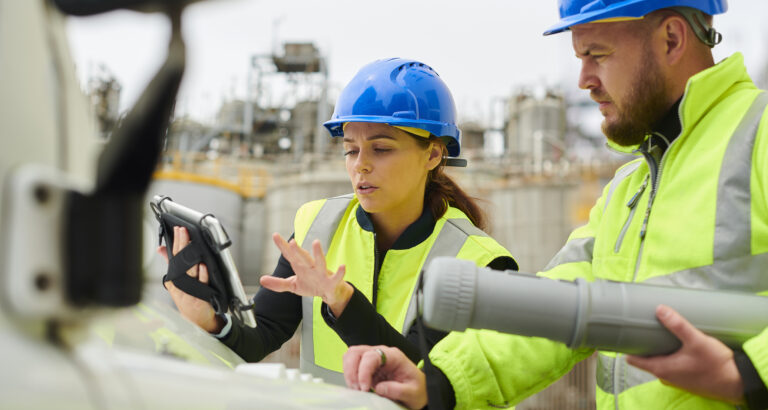
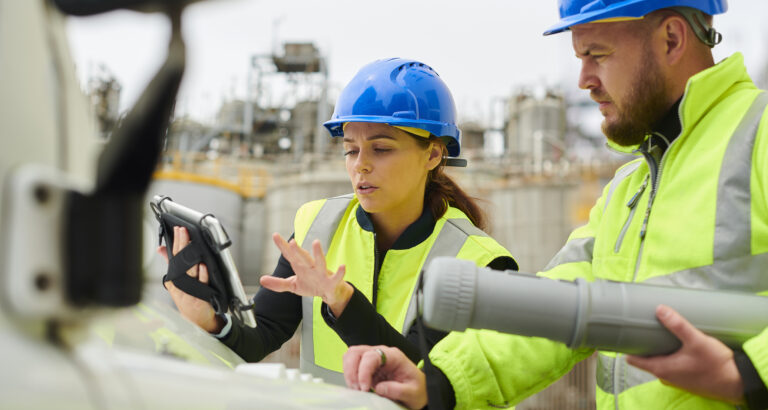
Risk and Reward Through MRO: How AI is Tackling Manufacturing’s Billion-Dollar Parts Problem
Industrial manufacturers producing on a global scale are often in a flurry of motion, pulling different levers for their businesses, working to automate processes, and seeking new ways to streamline activities to maximize uptime.
The pressure is on because tremendous amounts of capital are allocated and laid out across manufacturing sites and assets. Too often, the amount of working capital allocated to manage the risk of downtime is an afterthought and becomes out of balance.
While traveling abroad and attending the SAP SC Inno Days Event, I met with various large manufacturers for discussions and insights. The common theme that kept bubbling up to the top of our conversations was ‘how to bridge the gap between procurement and operations, account for dynamic lead times, and identify criticality across materials.’
A significant component of many of the largest companies’ global inventories is orchestrated into a system known as MRO (Maintenance, Repair and Operations). MRO takes into account all the supplies necessary for sustaining production. This involves managing equipment upkeep, troubleshooting, and addressing unexpected breakdowns to ensure uninterrupted operations. MRO covers procuring essential supplies like spare parts, tools, and consumables necessary for maintenance and repair.
Strategic executives are continuously challenged to strike a balance between working capital and risk. The real goal is to optimize production and minimize downtime.
Solving the Inventory Crisis
The inventory crisis is a critical issue for many large manufacturers, and with it comes a myriad of issues where working capital and risk are at stake.
U.S. Census data shows the global excess inventory amounts to trillions of dollars. As demand softens, this inventory is likely to become excess or obsolete. For example, the global oil and gas industry stockpiles billions in parts to keep their rigs, refineries, pipelines, and various facilities running.
According to a recent report, Fortune Global 500 manufacturing and industrial firms lose up to 3.3 million hours annually to unplanned downtime. The financial cost of this downtime to those organizations is $864 billion, the equivalent of eight percent of their annual revenues. As demand can fluctuate for any industry segment, downtime is a major concern. For these organizations, knowing real time consumption and how crucial one part or component can be to the output of finished products.
One way to avoid this crisis is to verify customer demand, quantities and delivery dates, inventory levels, production capacities, and lead times to meet that demand. This information, provided through intelligent software systems, allows supply chain managers to make better-informed decisions about production planning, inventory management, procurement, and logistics operations.
Another method is to establish ‘criticality for materials,’ determining what materials are needed in-house to keep production moving. Executives must assess the importance of different materials used in the production process. This involves making decisions about supply risk, asset reliability, costs, regulatory compliance, and delivery times.
Specifically, managing these critical production issues is based on knowing real-time consumption and how crucial one part or component can be to the manufacturing output and finished products. Obtaining those parts is also a major factor. For example, some parts, such as specialized/small motors, are critical and extremely difficult to source quickly.
Changing the Paradigm
AI and machine learning, when applied to existing data, can further assist industrials and manufacturers in reducing costs, reducing risk, and enhancing productivity, contributing to long-term success in their industry.
Manufacturers have been accustomed to the old approach to software. Large production facilities have used traditional data approaches with ERP software for years. In that time, they have statically tracked their inventories, cataloged and named thousands of parts and components spread throughout hundreds of sites–often inconsistently–with various information reflected in their inventory databases.
However, these systems, which were not built with MRO management in mind, are flawed and consistently fall short. They cannot resolve the reams of data about parts and supplies dynamically enough and cannot decipher when duplicates exist.
However, the industry environment is changing, and AI-powered MRO optimization is greatly improving inventory visibility and providing a new path to striking the right balance between procurement, operations and finance.
When manufacturers incorporate AI-powered MRO optimization, they find that the processes help improve margins, enhance routine maintenance needs, increase service levels, and minimize unplanned downtime—three critical factors that can significantly impact a company’s bottom line. With accurate inventory data and forecasting capabilities, industrial production facilities can streamline processes, lower excess inventory, and minimize stockouts.
Manufacturers are now more than ever able to take better approaches to software and data. With the benefit of machine learning, AI-powered MRO optimization systems can intelligently understand mislabeled parts and associate the inventories of hundreds of facilities in a single view. Such results were unachievable with previous generations of technology.
This brings renewed clarity to optimizing inventory, procurement and risk. AI-powered MRO systems can elevate and prioritize pressing issues that require immediate attention. This builds renewed efficiency as tasks are monitored and workloads are optimized through intelligent work queues and configurable layouts.
When using AI-powered MRO optimization, manufacturers can strike the perfect balance of capital to risk across their network. This results in better demand forecasting, stronger inventory planning and tracking, increased supply optimization, and more accurate reporting and analytics.
Moving Ahead with AI
It’s time to take control of the bloated insurance policy that is inventory and re-organize your MRO. Manufacturers can bring together and harmonize disparate material data across multiple enterprise systems with advanced AI tools. This helps your organization reduce risk, optimize working capital, and ensure production uptime to meet customer needs.
Purpose-built AI software for MRO materials provides continuous inventory balancing and increased sourcing intelligence. Plus, it can help reduce supply risk by striking the perfect balance of capital to risk across your network. And isn’t that what we all want to achieve?
Paul Noble,
Founder & CSO of Verusen