Early Signs of Supply Chain Industry Turn-Around – Companies are driving real improvements in goods and component delivery
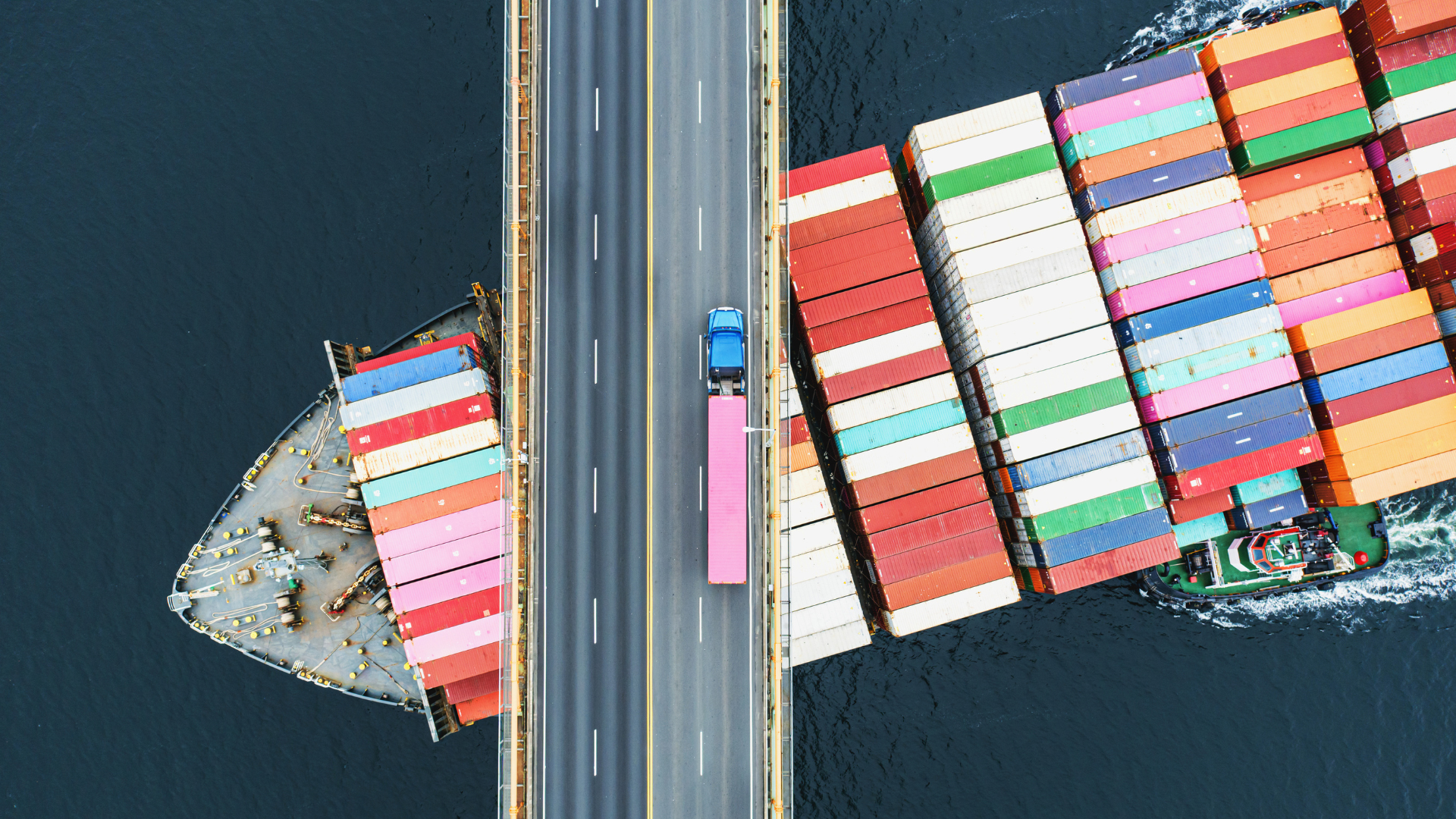
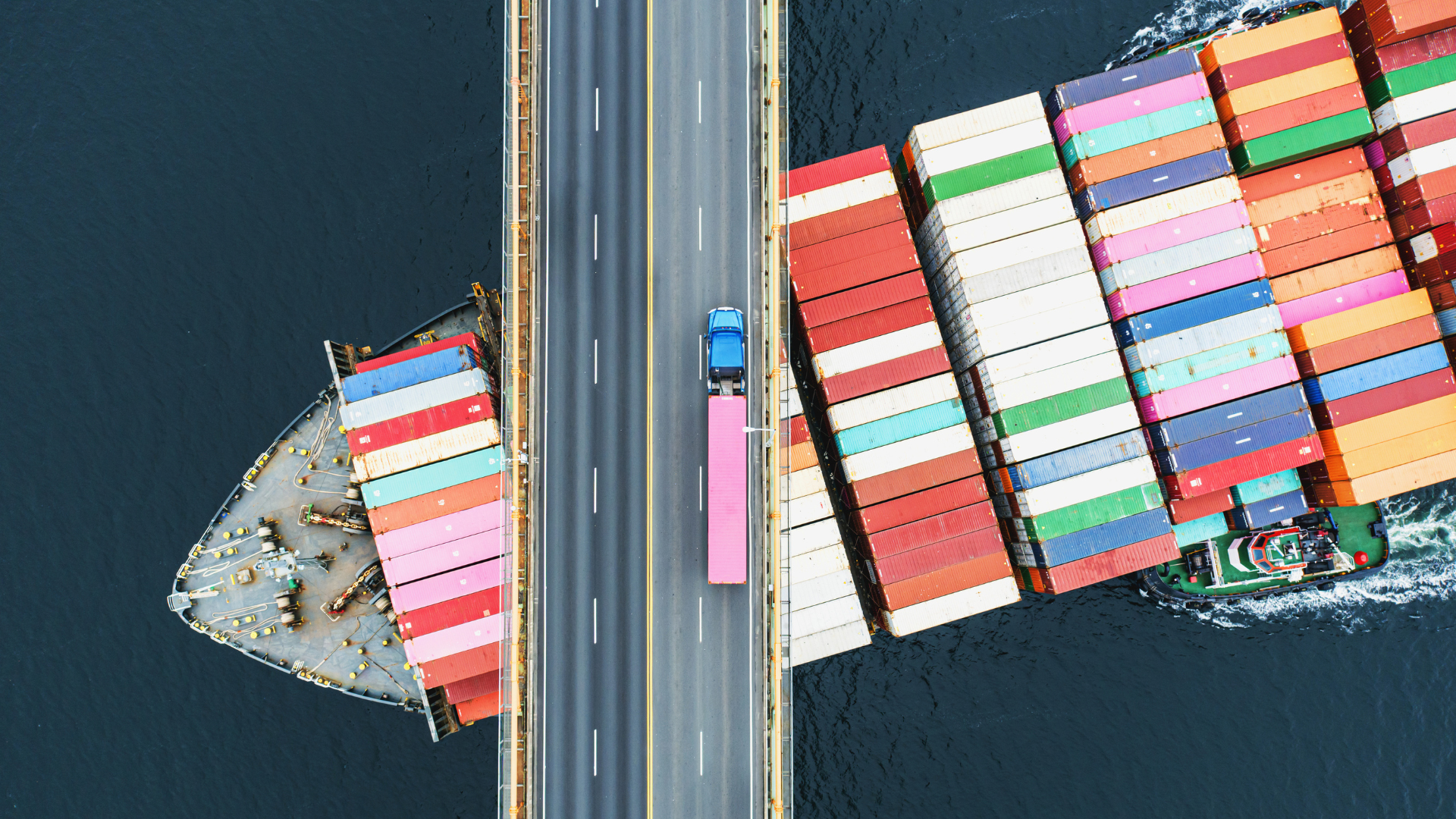
It’s been an eventful two years in the supply chain industry. While problems in supply chains still exist as we head into the fall of 2022, we are starting to see easing pressures in shipping and transportation, where things are moving faster and at higher volumes. That’s good news in a world where constant and unexpected negative change lies around every corner.
There are plenty of problematic areas across the supply chain. Still, perhaps we should point out some of the positive improvements organizations have made in recent years to ensure continuity becomes commonplace moving forward. Positive signs are emerging in port locations and elsewhere. Shipping volumes are up, with more consistent demand for traditional activities. Other measures, like the cost of shipping rates or the length of time for goods to be shipped, seem to be easing globally.
And the main reason for easing supply chain issues is that more manufacturers and business leaders have begun using purpose-built solutions and AI-enabled tools to create greater efficiencies in supply chain management.
During the pandemic, amidst a shortage of workers and business needs going unmet, senior executives started to explore how AI systems and processes could work in the supply chain to increase automation and improve visibility. They found that these tools made a difference. As a result, more companies today are adopting AI in their operations, marking a shift in an industry that has traditionally been reluctant to adopt newer technologies.
Shorter Shipping Times
Flexport’s Ocean Timeliness Indicator tracks the length of time to ship goods from their original port to the destination port. July’s numbers indicated that the time period is about 95 days (per July 10). That was a positive sign over the previous year (Oct 2021), when it took some goods over 110 days to be delivered to the US from Asia.
August is showing even more improvement in shipping times. TPEB (Trans-Pacific East Bound) times fell to 89 days. That’s the lowest level in a year. The FEWB (Far East Westbound) route increased by one day to 91 days. Flexport estimates that shipping transit times have decreased by about 35%.
Increasing Port Volumes
In Long Beach, CA, port operators set new records for July, according to the Long Beach Business Journal. Recent stats showed dockworkers and terminal operators moved 835,412 shipping containers in July. That’s more than 83,000 containers than the previous June 2018 record and a 15.3% increase over June 2021.
Some major ports, like the Port of New York and New Jersey, are seeing record import volumes, with a nearly 12% cargo increase in 2022 compared to last year. It’s also a much higher 34% in cargo volume compared to the same period during pre-pandemic 2019.
Companies Are Finally Making Changes
In light of the supply chain obstacles over the past several years, companies are finally focusing on supply chain operations and increasing resiliency. For example, companies that relied heavily on only one location for much of their supply chain goods, such as from China, have started to diversify their sites and use alternate modes of sourcing and transport.
This recent Gartner report shows that companies are starting to use a hybrid regional model. Major companies in a global supply chain network are modifying networks in several ways. Some include combining local or regional elements or models with final regional assembly and local-for-local networks.
Additionally, Gartner reveals that 95% of those firms surveyed are either evaluating or executing changes to their China sourcing and manufacturing strategy. More than half have already put those plans into action.
While it doesn’t mean everything gets solved in just a few months, these bright spots show that the situation is easing.
We also see greater adoption by savvy companies in digitalization and interest in conquering their materials complexity. AI is no longer a black box to be afraid of, and there is an appetite to learn how they can attain greater supply chain resiliency and improve their bottom lines. Innovation is making a difference in supply chain operations.
A McKinsey study notes that AI-enabled supply-chain management has enabled adopters to improve logistics costs by 15%, inventory levels by 35%, and service levels by 65%.
MRO strategies for beating back supply chain bumps
Companies are also starting to embrace an MRO (Maintenance, Repairs, Operations) strategy for business operations enabling them to see the bigger picture on inventory and operational processes more accurately and efficiently.
A focused MRO strategy helps companies harmonize their data and create integrity and transparency across all their data catalogs, helping them avoid supply chain risks and achieve a better cost balance.
The Gartner report, “Improve Asset Performance by Segmenting MRO Spare Parts Inventory,” encourages companies to organize and segment their spare part inventories in line with overall critical business needs. This fiscally responsible approach will further serve to improve bottom line asset performance.
The report also notes that supply organizations must work with partners and experts to align their inventory investment with maintaining assets. Working through an industry-leading software platform can help plug previously unseen gaps in delivery and distribution and bring more real-time visibility to help alleviate supply chain bottlenecks. Companies that ‘get’ this and move forward quickly with the new AI tools available will likely be able to beat back any future supply chain bumps with greater ease in the coming years.
Supply chain leaders have been starting to make gains and overcome the industry’s obstacles for the past two years. Leveraging MRO inventory data for spare parts planning and asset performance of inventory investments is an achievable goal for companies. Slowly but surely, problems are being resolved as innovations take hold.
Founder & CEO of Verusen